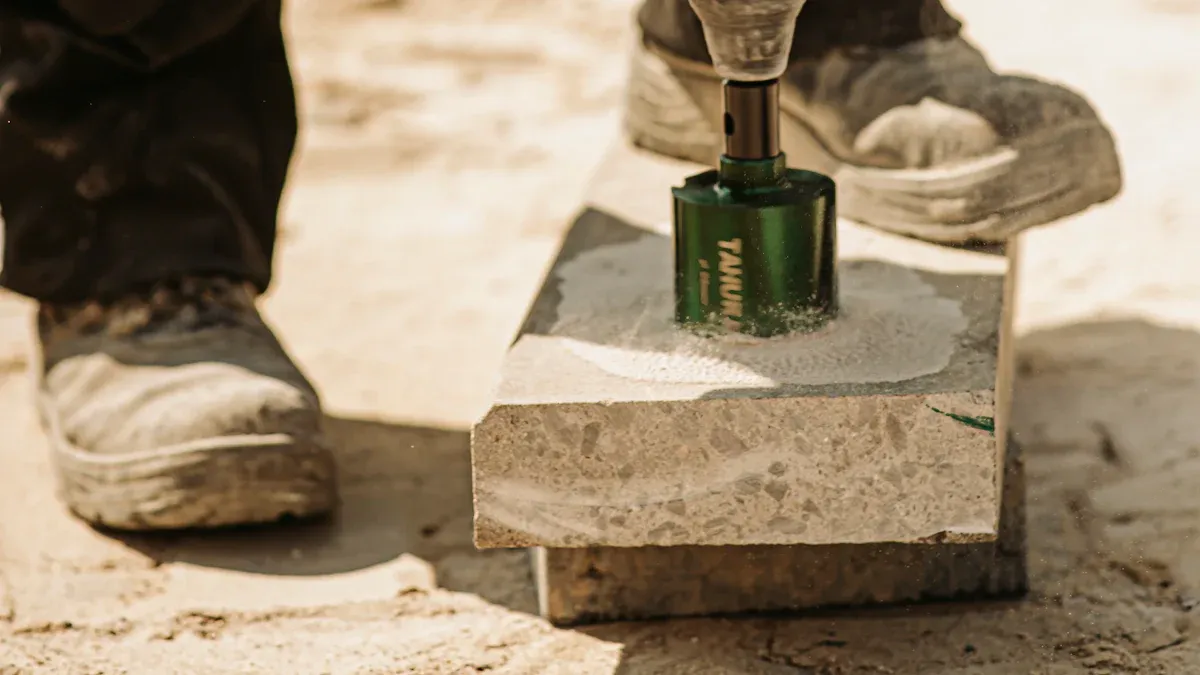
Excavator hammer parts play a vital role in construction and demolition tasks. A lack of understanding of these components can lead to issues like power loss, excessive vibration, and overheating. You may also face reduced efficiency due to incorrect hydraulic pressure settings or worn tool bits. By familiarizing yourself with these parts, you can prevent such problems and ensure smooth operation. This knowledge helps you maintain optimal performance and extend the lifespan of your equipment.
Key Takeaways
Knowing excavator hammer parts helps avoid problems like overheating.
Check and care for parts like the piston and seals often.
Pick the correct tool for your hammer to work better.
Watch the nitrogen pressure to improve performance and protect parts.
Make a schedule to check and replace parts on time.
Key Excavator Hammer Parts and Their Functions
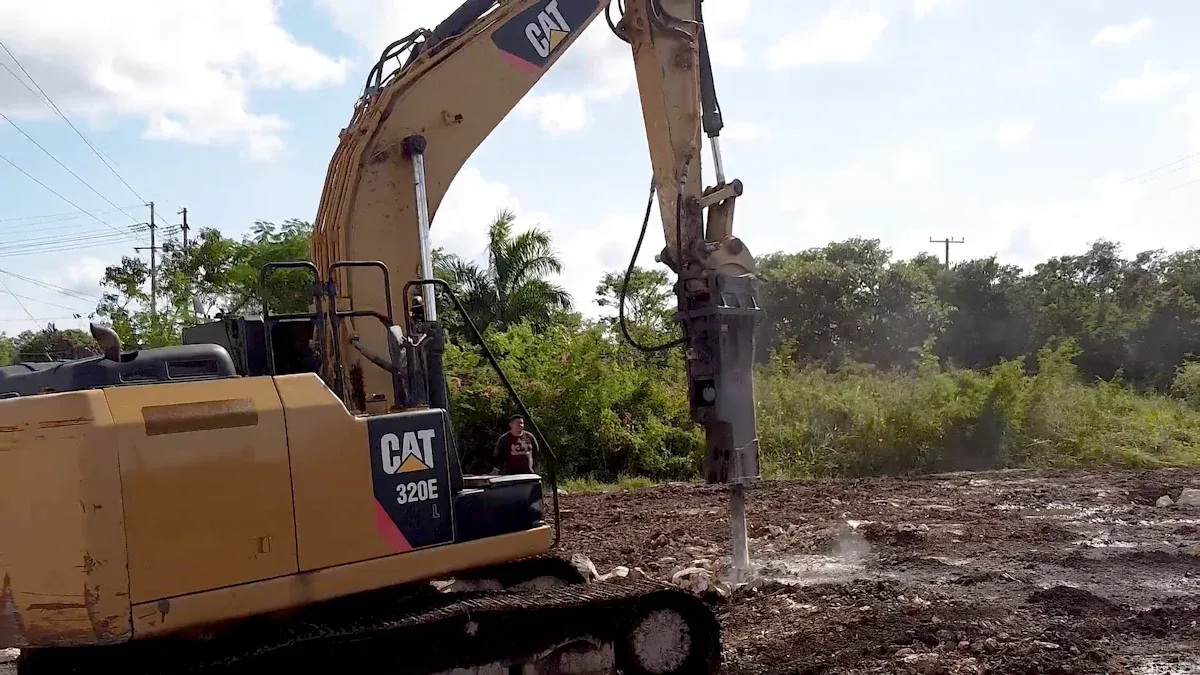
Housing
The housing serves as the protective shell for your excavator hammer. It shields the internal components from external damage caused by debris, dust, or accidental impacts. This robust casing ensures the hammer remains functional even in harsh environments. Its durability allows you to operate the equipment in challenging conditions without worrying about frequent repairs or replacements.
Piston
The piston is the powerhouse of your excavator hammer. It converts hydraulic energy into mechanical force, enabling the hammering action that breaks through tough materials. Here’s how it works:
Hydraulic breakers rely on hydraulic principles, where pressure applied to a fluid transmits force throughout the system.
Oil flows into the hammer via a valve, building pressure in the upper chamber during the upward stroke.
When the lower chamber releases pressure, the piston moves upward. The upper chamber then becomes high-pressure, driving the piston downward to deliver powerful blows.
This process ensures consistent and efficient performance, making the piston a critical component of your excavator hammer parts.
Tool (Chisel or Moil Point)
The tool, often a chisel or moil point, is the working end of the hammer. It directly impacts the material, breaking it apart. The choice between a chisel and a moil point depends on the task at hand:
Tool Type | Design Features | Application |
---|---|---|
Chisel | Sharp, pointed end | Precise breaking, commonly used for foundations |
Moil | Blunt, pyramid-shaped end | General-purpose breaking, suitable for walls |
Selecting the right tool shape is essential for effective operation. A pointed tool works best for hard surfaces, while a flat tool is ideal for breaking up concrete. By choosing the appropriate tool, you can maximize the hammer’s efficiency and minimize wear.
Tip: Regularly inspect the tool for wear and replace it when necessary to maintain optimal performance.
Nitrogen Chamber
Supplies power and absorbs shock during operation
The nitrogen chamber plays a crucial role in your excavator hammer’s performance. It stores compressed nitrogen gas, which acts as a secondary power source. This gas amplifies the force generated by the hydraulic system, ensuring each hammer strike delivers maximum impact. Without the nitrogen chamber, the hammer would rely solely on hydraulic pressure, reducing its overall efficiency.
Another important function of the nitrogen chamber is shock absorption. When the hammer strikes a hard surface, the impact generates significant vibrations. These vibrations can damage internal components over time. The nitrogen gas cushions these shocks, protecting the hammer’s internal parts and extending its lifespan.
Note: Always check the nitrogen pressure regularly. Low pressure can reduce the hammer’s power and increase wear on other components.
Enhances the hammer’s efficiency and performance
A well-maintained nitrogen chamber ensures your excavator hammer operates at peak efficiency. By providing additional power, it reduces the workload on the hydraulic system. This not only improves the hammer’s performance but also minimizes fuel consumption, saving you money in the long run.
The nitrogen chamber also contributes to consistent hammering action. It maintains steady pressure levels, ensuring each strike is as powerful as the last. This consistency is especially important when working on tough materials like reinforced concrete or rock.
Key Benefits of the Nitrogen Chamber:
Increases hammering force for better material breaking.
Reduces wear and tear on hydraulic components.
Improves fuel efficiency by optimizing power usage.
Tip: Use a pressure gauge to monitor the nitrogen chamber. Maintaining the correct pressure level is essential for optimal performance.
By understanding the nitrogen chamber’s role, you can ensure your excavator hammer remains efficient and reliable during demanding tasks.
Hydraulic System Components in Hydraulic Hammers
Accumulator
Stores hydraulic energy for consistent hammering
The accumulator plays a vital role in maintaining the performance of your hydraulic hammer. It absorbs pressure pulsations generated by the hydraulic pump, ensuring consistent hammering action. This feature minimizes vibrations in the hydraulic circuit, allowing for smoother operation. By cushioning shocks from sudden impacts or valve closures, the accumulator protects sensitive components from damage.
Key Benefits of the Accumulator:
Reduces vibration and shock in the system.
Extends the lifespan of hydraulic hammer components.
Reduces pressure spikes in the system
Pressure spikes can cause significant issues, such as vibration, shock, and even damage to your hydraulic hammer. These spikes often result from quick deceleration of cylinders or sudden valve closures. The accumulator absorbs these pulsations, mitigating shocks and preventing damage to connectors and joints. This not only reduces maintenance costs but also ensures a longer lifespan for your equipment.
Tip: Regularly inspect the accumulator for wear or leaks to maintain optimal performance.
Hydraulic Hoses
Transmit hydraulic fluid between the excavator and the hammer
Hydraulic hoses serve as the lifeline of your hydraulic hammer, transmitting fluid between the excavator and the hammer. High-quality hoses ensure smooth fluid flow, which is essential for consistent hammering performance.
Must be durable to handle high pressure and wear
Durability is crucial for hydraulic hoses. They are constructed using synthetic rubber with reinforcement layers made from steel wire or textile braids. This design allows them to withstand high pressure, temperature fluctuations, and abrasion. Protective covers shield the hoses from UV radiation and physical damage, ensuring long-lasting performance.
Note: Replace worn or damaged hoses promptly to avoid hydraulic fluid leaks.
Control Valve
Regulates the flow of hydraulic fluid
The control valve ensures precise operation by regulating the flow of hydraulic fluid. It directs the fluid to the hammer at the correct pressure, enabling efficient hammering action.
Ensures precise operation of the hammer
A malfunctioning control valve can lead to issues like water hammer, leakage, or overheating. Signs of trouble include abnormal noises, difficulty in operation, or visible leaks. Addressing these problems promptly ensures your hydraulic hammer operates smoothly and efficiently.
Tip: Clean the control valve regularly to prevent contamination and mechanical failure.
Wear and Impact Parts in Excavator Hammer Parts
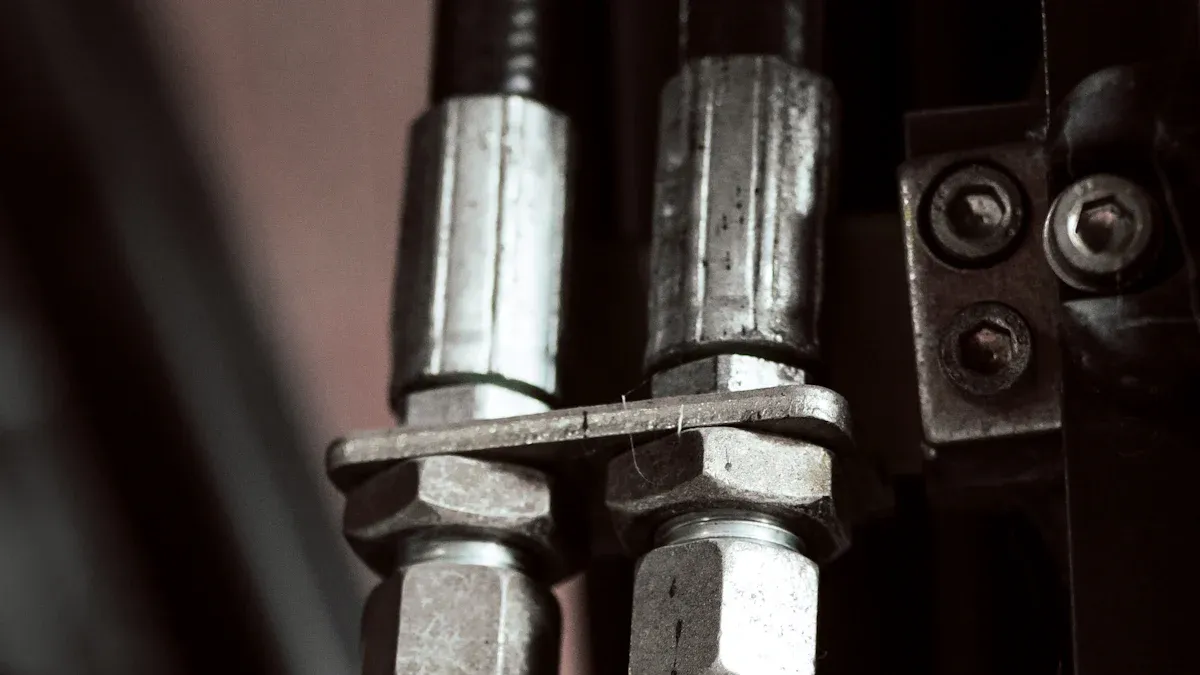
Bushings
Protect the hammer housing from wear caused by the tool
Bushings act as a protective barrier between the hammer housing and the tool. They absorb the friction and wear caused by the tool’s movement, ensuring the housing remains intact during operation. Without bushings, the hammer housing would face rapid deterioration, leading to costly repairs.
Extend the lifespan of the hammer
The durability of bushings depends on the material used. Selecting the right material ensures long-lasting performance. Here’s a comparison of common bushing materials:
Material | Pros | Cons |
---|---|---|
PTFE/Teflon | Resistant to corrosion, low friction, withstands high temperatures | Dimensional changes may lead to failure, not as durable as steel |
PEEK | Exceptional stiffness, can endure high temperatures, excellent chemical resistance | Expensive, limited by low melting point |
UHMW PE | Low coefficient of friction, versatile for various uses | More expensive than other plastics, challenging to work with |
PPS | Strong electrical insulating properties, high chemical and thermal resistance | Difficult to machine, fairly expensive |
Nylon | Affordable, long-term performance | Poor UV and moisture resistance, not ideal for harsh environments |
Tip: Regularly inspect bushings for wear and replace them promptly to maintain the hammer’s efficiency.
Retainer Pins
Secure the tool in place during operation
Retainer pins hold the tool securely in position, ensuring it doesn’t shift or dislodge during use. This stability is crucial for safe and effective operation.
Prevent accidental tool ejection
Failures in retainer pins can lead to tool ejection, posing safety risks. Common causes of failure include:
Operation with worn-out retaining pins
Blank-firing
Twisting the tool
Note: Replace retainer pins at the first sign of wear to avoid operational hazards.
Seals
Prevent hydraulic fluid leaks
Seals play a vital role in maintaining the hydraulic system’s integrity. They prevent fluid leaks, ensuring the hammer operates without interruptions.
Maintain system pressure and efficiency
Different types of seals offer unique benefits:
O-rings: Effective in both static and dynamic applications, made from materials like silicone and nitrile.
Piston seals: Prevent fluid bypass in hydraulic cylinders, maintaining pressure.
Spiral wound gaskets: Ideal for high-pressure and high-temperature applications.
PTFE seals: Known for chemical resistance and low friction, suitable for aggressive fluids.
Tip: Inspect seals regularly and replace them to avoid pressure loss and maintain efficiency.
Maintenance Tips for Excavator Hammer Parts
Regular Inspection
Check for wear and damage on key components
Regular inspection is essential to keep your hydraulic hammer in top condition. Examine critical components like the piston, bushings, and seals for visible signs of wear or damage. Look for cracks, loose fittings, or shiny marks on the tool, as these can indicate improper lubrication or excessive friction. Identifying issues early prevents more significant problems, such as hydraulic leaks or performance loss.
Replace worn parts promptly to avoid further issues
Delaying the replacement of worn parts can lead to costly repairs and downtime. For example, worn bushings can cause excessive clearance, damaging the piston and cylinder. Replace these parts as soon as you notice wear to maintain the efficiency and longevity of your hydraulic hammer.
Tip: Create a maintenance schedule to ensure regular inspections and timely replacements.
Proper Lubrication
Ensure moving parts are well-lubricated to reduce friction
Lubrication minimizes friction between moving parts, such as the piston and bushings, reducing wear and extending their lifespan. Grease your hydraulic hammer every two hours during operation, or adjust based on the hammer’s size and working conditions. High-quality grease, like high-moly grease, withstands temperatures above 500°F and ensures optimal performance.
Best Practices for Lubrication:
Use enough grease to fill the tool-bushing area.
Check for shiny marks on the tool, which indicate insufficient lubrication.
Consider auto-lube systems for larger hammers to maintain consistent lubrication.
Use the recommended grease for your hammer model
Always follow the manufacturer’s recommendations for grease type and application frequency. Using the wrong grease can lead to overheating, excessive vibration, and premature wear. Proper lubrication ensures smooth operation and prevents hydraulic system failures.
Note: Insufficient lubrication can cause oil leakage, excessive vibration, and overheating, all of which reduce the hammer’s efficiency.
Common Issues and Solutions
Address hydraulic leaks by inspecting seals and hoses
Hydraulic leaks are a common issue in excavator hammers. Inspect seals and hoses for visible damage, such as cracks or wear. Loose fittings can also cause leaks, so tighten them as needed. Promptly repair or replace damaged components to prevent fluid loss and maintain system pressure.
Resolve performance issues by checking the accumulator and control valve
Performance issues, such as loss of power or excessive vibration, often stem from problems with the accumulator or control valve. Ensure the accumulator maintains proper pressure to absorb shocks and provide consistent hammering force. Inspect the control valve for blockages or wear, as it regulates hydraulic fluid flow. Addressing these issues promptly restores your hydraulic hammer’s efficiency.
Common Performance Problems and Fixes:
Loss of efficiency: Check hydraulic pressure and tool bits for wear.
Overheating: Maintain proper hydraulic oil levels and inspect the cooling system.
Excessive vibration: Adjust hydraulic pressure and inspect dampening pads.
Tip: Regular maintenance of seals, hoses, and the hydraulic system prevents most performance issues.
YNF Machinery’s Role in Providing High-Quality Excavator Hammer Parts
Hydraulic Cylinder Seal Kits for Leak Prevention
Ensure smooth operation and prevent oil leaks in hydraulic systems.
Hydraulic Cylinder Seal Kits are essential for maintaining the efficiency of your excavator’s hydraulic system. These kits prevent oil leaks, ensuring smooth operation and reducing the risk of downtime. YNF Machinery offers seal kits made from high-grade materials like NBR and PTFE. These materials provide durability and flexibility, allowing the kits to withstand shocks and vibrations during heavy-duty tasks.
Tip: Regularly inspect your hydraulic seals to avoid unexpected leaks and maintain system pressure.
Designed to meet international quality standards.
YNF Machinery’s seal kits meet international quality standards, making them reliable for global applications. Their precise manufacturing ensures a perfect fit, reducing the chances of misalignment. This attention to detail enhances the lifespan of your hydraulic components and minimizes maintenance costs.
Excavator Couplings for Efficient Power Transmission
Enhance the performance and longevity of hydraulic hammers.
Excavator couplings play a critical role in transmitting power between the engine and the hydraulic pump. YNF Machinery provides couplings designed to handle high torque and vibration. These couplings improve the performance of your hydraulic hammer by ensuring smooth power transfer. Their robust construction minimizes wear, extending the lifespan of your equipment.
Key Features of YNF Couplings:
High flexibility to compensate for misalignment.
Durable materials that withstand harsh conditions.
Easy installation and maintenance.
Available in various types to suit different applications.
YNF Machinery offers a wide range of couplings, including Centaflex-A and Bowex types. Each type caters to specific needs, such as vibration isolation or high-speed applications. This variety ensures you can find the perfect coupling for your excavator, enhancing its efficiency and reliability.
Excavator Engine Parts for Reliable Performance
Provide the necessary power and torque for heavy-duty operations.
Your excavator’s engine is its powerhouse, and high-quality engine parts are crucial for optimal performance. YNF Machinery supplies components like pistons, crankshafts, and turbochargers that deliver the power and torque needed for demanding tasks. These parts are engineered to handle high temperatures and pressures, ensuring consistent performance.
Note: Always choose engine parts that match your excavator’s specifications to avoid compatibility issues.
Manufactured to withstand harsh working conditions.
YNF Machinery’s engine parts are built to endure tough environments. Their robust design reduces the risk of failure, even under extreme conditions. By investing in durable engine parts, you can minimize downtime and keep your operations running smoothly.
Factors to Consider When Choosing Engine Parts:
Durability to withstand wear and tear.
Compatibility with your excavator model.
Ease of maintenance and availability of spare parts.
By selecting YNF Machinery’s high-quality products, you ensure reliable performance and long-term value for your excavator.
Excavator Engine Assembly for Comprehensive Solutions
Includes complete engines and specific components for various brands.
When you need a reliable solution for your excavator’s engine, a complete engine assembly can save you time and effort. YNF Machinery offers comprehensive engine assemblies that include all essential components. These assemblies are designed to meet the demands of various excavator brands, such as Caterpillar, Komatsu, Hitachi, and Volvo. Whether you need a full engine replacement or specific parts like pistons, crankshafts, or turbochargers, YNF Machinery has you covered.
A complete engine assembly provides several advantages. It eliminates the hassle of sourcing individual parts, ensuring you get a fully compatible and functional unit. This approach reduces the risk of mismatched components, which can lead to performance issues. By choosing a pre-assembled engine, you can focus on getting your excavator back to work without unnecessary delays.
Tip: Always verify the compatibility of the engine assembly with your excavator model. This ensures optimal performance and prevents installation challenges.
Ensures compatibility and ease of installation.
Compatibility is a critical factor when selecting an engine assembly. YNF Machinery ensures that its products are tailored to fit a wide range of excavator models. Each assembly undergoes rigorous testing to guarantee it meets the specifications of the intended brand and model. This attention to detail simplifies the installation process, saving you valuable time.
Ease of installation is another key benefit. With a pre-assembled engine, you avoid the complexities of assembling individual components. This not only reduces downtime but also minimizes the risk of errors during installation. YNF Machinery’s engine assemblies come with clear instructions, making the process straightforward even for less experienced technicians.
Note: Proper installation is essential for maximizing the lifespan of your engine assembly. Follow the provided guidelines carefully to avoid potential issues.
By choosing YNF Machinery’s engine assemblies, you gain a reliable, efficient, and hassle-free solution for your excavator’s engine needs.
Understanding excavator hammer parts is essential for maintaining the efficiency of your hydraulic hammer. Each component, from the housing to the hydraulic system, plays a critical role in ensuring smooth operation and durability. Proper maintenance of these parts reduces downtime and extends the lifespan of your equipment.
YNF Machinery provides high-quality solutions for your hydraulic hammer needs. Their offerings include Hydraulic Cylinder Seal Kits, excavator couplings, and engine parts. These products ensure your hydraulic system operates efficiently, delivering reliable performance in demanding conditions. By choosing YNF Machinery, you invest in the longevity and productivity of your equipment.
FAQ
What are the signs of a worn-out excavator hammer tool?
Look for visible cracks, shiny marks, or uneven wear on the tool. These signs indicate excessive friction or improper lubrication. A worn tool reduces efficiency and can damage other components.
Tip: Replace the tool immediately to maintain optimal performance and prevent further damage.
How often should you inspect hydraulic hoses?
Inspect hydraulic hoses every 50 to 100 hours of operation. Check for cracks, leaks, or bulges. Damaged hoses can lead to hydraulic fluid loss and reduced hammer efficiency.
Note: Regular inspections prevent unexpected failures and costly downtime.
Why is nitrogen pressure important in the hammer?
Nitrogen pressure amplifies the hammer’s impact force and absorbs shocks. Low pressure reduces efficiency and increases wear on internal components.
Tip: Use a pressure gauge to monitor and maintain the correct nitrogen levels.
How do you choose the right coupling for your excavator?
Consider the excavator model, torque requirements, and working conditions. Flexible couplings like Centaflex-A work well for misalignment, while Bowex couplings suit high-speed applications.
Note: Consult your equipment manual or supplier for compatibility details.
What should you do if your hydraulic hammer overheats?
Check the hydraulic oil level and cooling system. Overheating often results from low oil or clogged filters. Clean or replace filters as needed.
Tip: Use the recommended hydraulic oil to ensure proper cooling and lubrication.