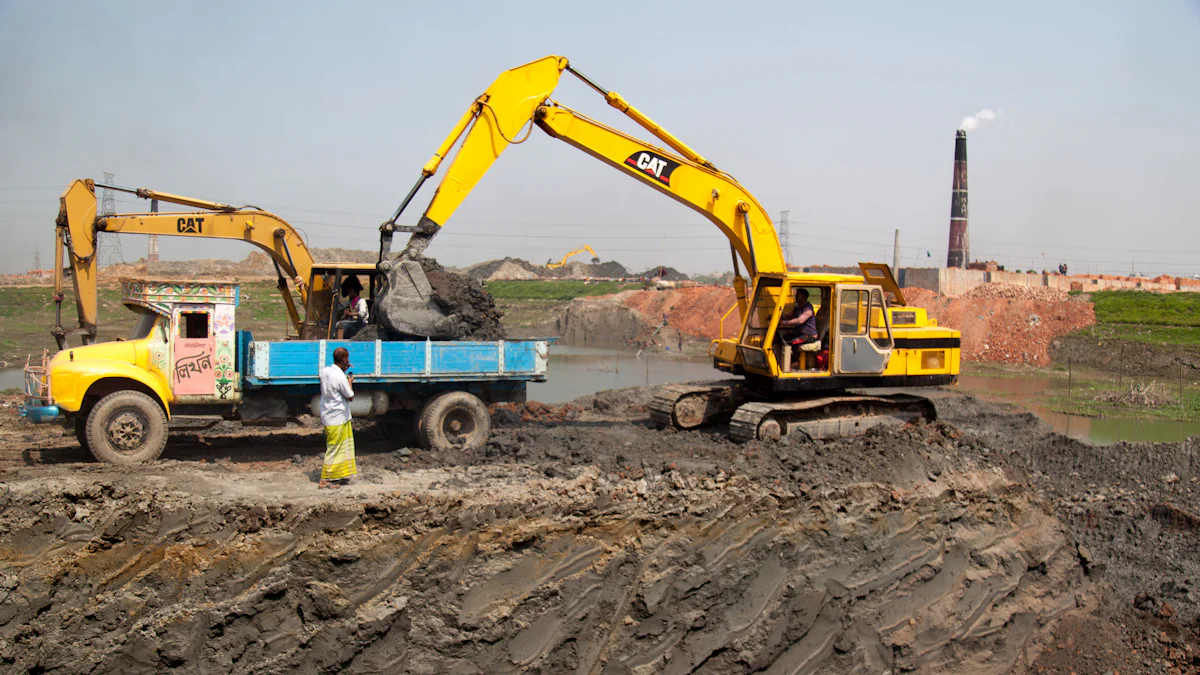
Mining and excavating wear parts play a vital role in ensuring the efficiency and durability of heavy equipment. These components endure extreme conditions, protecting your machinery from wear and tear during demanding operations. High-quality wear parts, including various types of mining wear parts and excavating wear parts, not only enhance the performance of heavy equipment and machinery but also reduce downtime and maintenance costs. With advancements in material science, modern wear parts are engineered to withstand the rigorous demands of mining environments, making them indispensable for earth-moving heavy equipment. Choosing the right types of mining wear parts and excavating wear parts ensures optimal functionality and long-term cost-effectiveness for your equipment.
Key Takeaways
High-quality mining and excavating wear parts are essential for enhancing equipment performance and reducing downtime, ultimately leading to cost savings.
Understanding the specific types of wear parts, such as bucket attachments, hydraulic shovels, and crusher components, allows for informed decisions that optimize operational efficiency.
Regular inspection and timely replacement of wear parts prevent unexpected breakdowns, ensuring smooth operations and safety in mining environments.
Choosing the right materials like hardened steel or tungsten carbide for wear parts enhances durability and performance under harsh conditions.
Proper maintenance practices, including cleaning and lubrication, significantly extend the lifespan of wear parts and improve overall equipment reliability.
Investing in high-quality wear parts may have a higher upfront cost but leads to long-term savings through reduced maintenance and increased productivity.
YNF Machinery offers comprehensive support and high-quality solutions tailored to meet the demands of mining operations, ensuring your equipment runs efficiently.
Types of Mining Wear Parts and Their Applications
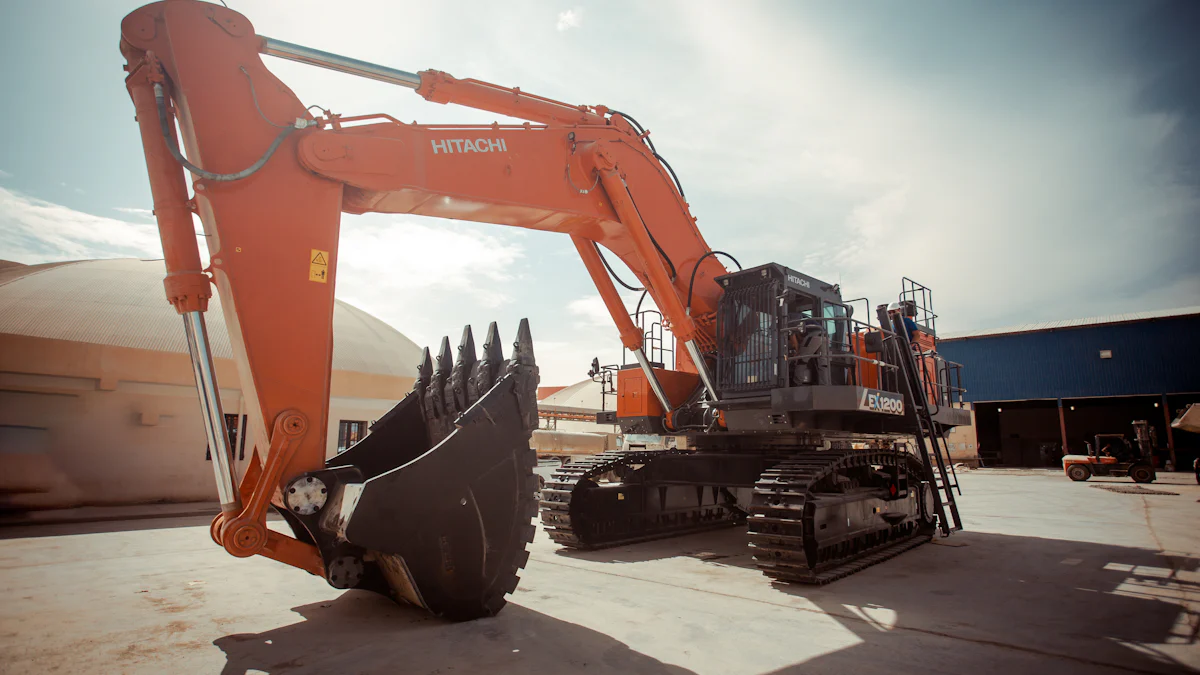
Mining operations demand durable and efficient wear parts to ensure the longevity and performance of your equipment. Understanding the various types of mining wear parts and their applications can help you make informed decisions for your operations.
Bucket Attachments for Mining Equipment
Types of bucket attachments (e.g., rock buckets, coal buckets)
Bucket attachments are among the most versatile tools in mining. These attachments come in different types, each designed for specific tasks. Rock buckets are built with reinforced edges to handle abrasive materials like rocks and gravel. Coal buckets, on the other hand, feature larger capacities to move lighter materials such as coal efficiently. These specialized designs ensure that your equipment performs optimally in diverse mining environments.
Uses in material handling and digging operations
Buckets play a critical role in material handling and digging operations. They scoop, carry, and unload materials like dirt, sand, and stone. In surface mining, buckets help remove overburden and extract valuable minerals. For underground mining, they assist in clearing debris and transporting materials through confined spaces. By choosing the right bucket attachment, you can enhance the productivity and efficiency of your mining equipment.
Hydraulic Shovels in Mining
Key wear components (e.g., teeth, edges, liners)
Hydraulic mining shovels, also known as hydraulic excavators, are essential for large-scale mining operations. These machines rely on key wear components to maintain their performance. Teeth, edges, and liners endure constant abrasion and impact during digging. Teeth penetrate hard surfaces, while edges and liners protect the bucket from wear. Regular inspection and replacement of these components ensure the longevity of your hydraulic mining shovels.
Applications in large-scale mining operations
Hydraulic mining shovels excel in large-scale operations due to their ability to move massive amounts of material quickly. These machines dig through and remove tons of earth, making them indispensable for surface mining projects. They also play a vital role in loading materials onto trucks or conveyor systems, streamlining the material transportation process. Their efficiency and power make them a cornerstone of modern mining equipment.
Dragline Excavators and Their Wear Parts
Dragline bucket components and their functions
Dragline excavators are among the largest types of heavy equipment used in mining. Their massive buckets rely on several wear parts to function effectively. Chains, teeth, and drag ropes work together to scoop and lift materials. Chains provide the necessary strength, while teeth break through tough surfaces. Drag ropes ensure smooth operation by controlling the bucket’s movement. These components must withstand extreme stress to keep the equipment operational.
Benefits in surface mining and earthmoving
Dragline excavators are particularly beneficial in surface mining. Their large buckets allow you to move vast quantities of overburden and ore in a single pass. This capability reduces the time and effort required for earthmoving tasks. Additionally, their long reach minimizes the need to reposition the equipment frequently, enhancing operational efficiency. By maintaining the wear parts of your dragline excavators, you can maximize their performance and lifespan.
Crusher Wear Parts for Mining
Types of crusher wear parts (e.g., jaw plates, mantles, concaves)
Crusher wear parts are essential components in mining operations. These parts include jaw plates, mantles, and concaves, each designed to handle specific tasks. Jaw plates are used in jaw crushers to crush large rocks into smaller pieces. Mantles and concaves, found in cone crushers, work together to grind materials into finer particles. These wear parts endure constant pressure and abrasion, making their durability critical for efficient ore processing.
You will find that selecting the right type of crusher wear part depends on the material being processed. For example, jaw plates are ideal for breaking down hard rocks, while mantles and concaves excel in reducing softer materials. By understanding the specific roles of these components, you can optimize your mining equipment’s performance and reduce unnecessary wear.
Role in ore processing and material reduction
Crusher wear parts play a pivotal role in ore processing and material reduction. They break down raw materials into manageable sizes, preparing them for further processing or transportation. In surface mining, crushers handle overburden and ore, ensuring efficient material flow. For underground mining, crushers reduce the size of extracted materials, making them easier to transport through narrow tunnels.
Efficient crushers equipped with high-quality wear parts minimize downtime and improve productivity. Regular maintenance and timely replacement of these parts ensure consistent performance. By investing in durable crusher wear parts, you enhance the longevity of your equipment and maintain smooth operations in demanding mining environments.
Conveyor Wear Parts in Mining
Common wear parts (e.g., rollers, belts, idlers)
Conveyors are indispensable in mining operations, and their wear parts are vital for maintaining functionality. Common conveyor wear parts include rollers, belts, and idlers. Rollers support the conveyor belt and ensure smooth movement. Belts transport materials across long distances, while idlers maintain belt alignment and reduce friction. These components face constant stress from heavy loads and abrasive materials, making their quality crucial for reliable performance.
You should choose wear parts that match the specific demands of your mining operation. For instance, reinforced belts are ideal for handling sharp or heavy materials, while durable rollers and idlers ensure stability during material transportation. Proper selection and maintenance of these parts can significantly extend the lifespan of your conveyor system.
Importance in material transportation
Conveyor wear parts are critical for efficient material transportation in mining. They move extracted materials from one point to another, streamlining the workflow in both surface mining and underground mining operations. In surface mining, conveyors transport overburden and ore to processing plants or storage areas. For underground mining, they navigate confined spaces, ensuring continuous material flow.
Well-maintained conveyors reduce operational delays and improve overall productivity. Regular inspection and replacement of worn parts prevent unexpected breakdowns. By prioritizing high-quality conveyor wear parts, you can enhance the efficiency of your mining equipment and minimize downtime, ultimately saving time and costs.
Types of Excavating Wear Parts and Their Uses
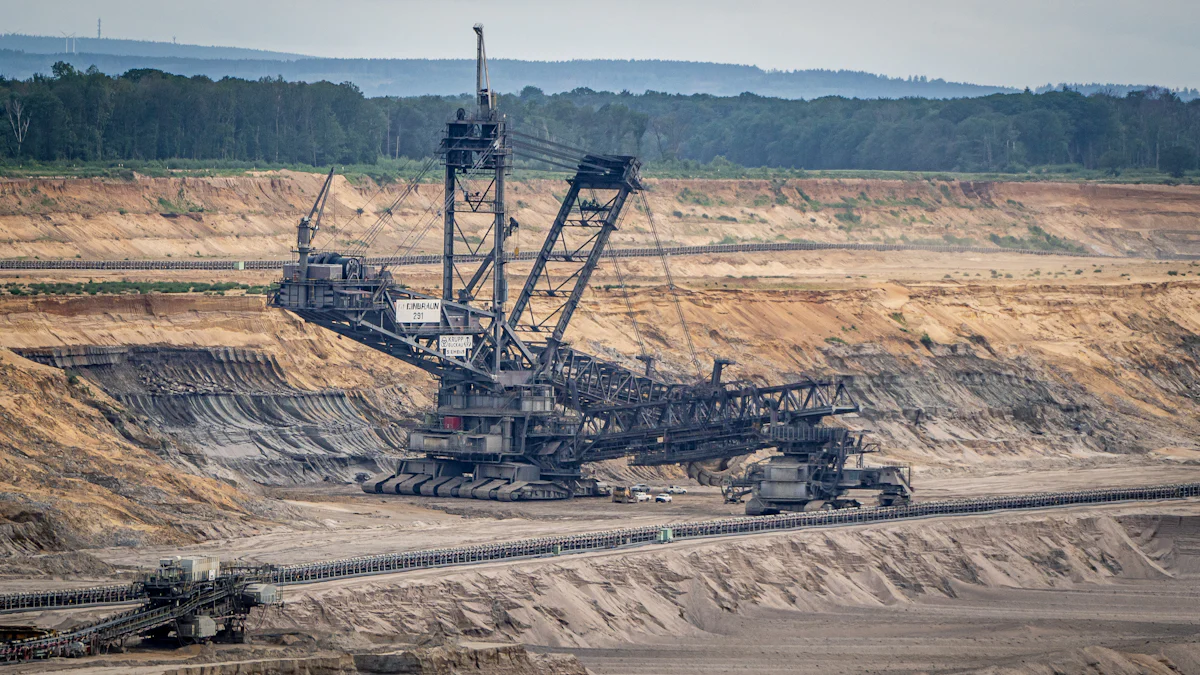
Excavating wear parts are essential for maintaining the efficiency and durability of heavy equipment used for digging and earth-moving tasks. These components endure harsh conditions, ensuring that your machinery operates at peak performance. Understanding the types of excavating wear parts and their uses can help you select the right components for your equipment.
Cutting Edges and Blades for Heavy Equipment
Types of cutting edges (e.g., straight, serrated)
Cutting edges and blades are critical wear parts for heavy equipment like bulldozers, loaders, and backhoe loaders. They come in various types to suit specific tasks. Straight cutting edges provide a clean and precise cut, making them ideal for grading and leveling. Serrated cutting edges, with their jagged design, excel in breaking through compacted soil or frozen ground. Each type is engineered to handle the demands of different terrains and materials.
Uses in grading, leveling, and trenching
Cutting edges and blades play a vital role in grading, leveling, and trenching operations. When grading, they create smooth surfaces for roads or construction sites. During leveling, they ensure even ground for building foundations. In trenching, these wear parts cut through soil efficiently, preparing the ground for pipelines or cables. By choosing the appropriate cutting edge, you can enhance the precision and productivity of your heavy equipment.
Teeth and Adapters for Excavators
Types of teeth (e.g., chisel, tiger, flare)
Teeth and adapters are indispensable for excavators and other heavy equipment used for digging. These wear parts come in various designs to tackle specific challenges. Chisel teeth are perfect for general-purpose digging and breaking soft materials. Tiger teeth, with their sharp points, penetrate hard surfaces like rock or compacted soil. Flare teeth feature a wide profile, making them suitable for scooping and moving loose materials. Each type ensures optimal performance in diverse conditions.
Applications in digging and breaking hard materials
Teeth and adapters are crucial for digging and breaking hard materials. Excavators equipped with the right teeth can easily break through tough surfaces, such as rocky terrain or frozen ground. These wear parts also improve the efficiency of trenching and material handling tasks. Regular inspection and replacement of worn teeth ensure that your equipment maintains its digging power and reduces operational delays.
Ripper Attachments for Excavators
Components of ripper attachments
Ripper attachments are powerful tools for breaking up compacted soil and rock. These attachments consist of several key components, including the shank, tooth, and mounting bracket. The shank provides the strength needed to penetrate tough surfaces. The tooth at the tip breaks through the material, while the mounting bracket secures the attachment to the excavator. Each component must withstand extreme stress to ensure reliable performance.
Benefits in breaking up compacted soil and rock
Ripper attachments offer significant benefits in breaking up compacted soil and rock. They make it easier to prepare the ground for construction or mining operations. By loosening hard materials, rippers reduce the strain on other equipment, such as skid steers or backhoes. This not only extends the lifespan of your machinery but also improves overall efficiency. Investing in high-quality ripper attachments ensures that your excavators can handle the toughest tasks with ease.
Side Cutters and Protectors for Excavator Buckets
Role in protecting bucket edges
Side cutters and protectors are essential components for maintaining the integrity of your excavator buckets. These wear parts shield the bucket edges from damage caused by abrasive materials, sharp rocks, and heavy impacts. By acting as a barrier, they prevent excessive wear and tear on the bucket itself, ensuring that your mining equipment remains operational for longer periods.
When you use side cutters, you reduce the risk of cracks or deformations along the bucket edges. This protection is particularly important in mining operations, where buckets frequently encounter harsh conditions. Protectors further enhance this defense by absorbing the impact forces that would otherwise compromise the bucket’s structure. Regular inspection and timely replacement of these components can save you from costly repairs and downtime.
Enhancing durability and reducing wear
Side cutters and protectors significantly enhance the durability of your heavy equipment. They distribute the stress evenly across the bucket, minimizing localized wear. This feature is especially beneficial for earth-moving tasks, where consistent performance is critical. By reducing wear, these components extend the lifespan of your buckets, allowing you to focus on productivity rather than maintenance.
In addition to durability, side cutters and protectors improve the efficiency of your equipment. They maintain the bucket’s shape and cutting edge, ensuring smooth digging and material handling. Whether you’re operating bulldozers, loaders, or backhoes, these wear parts help you achieve better results with less effort. Investing in high-quality side cutters and protectors is a cost-effective way to enhance the performance of your mining equipment.
Wear Liners for Excavator Buckets
Types of liners (e.g., rubber, steel)
Wear liners are indispensable for protecting excavator buckets from abrasion and impact. These liners come in various materials, each suited for specific applications. Rubber liners offer excellent resistance to impact and vibration, making them ideal for handling softer materials. Steel liners, on the other hand, provide superior durability and abrasion resistance, making them perfect for mining operations involving hard and abrasive materials.
The choice of liner depends on the type of material you handle and the conditions of your operation. For instance, rubber liners are commonly used in applications where noise reduction and flexibility are priorities. Steel liners, with their robust construction, are better suited for high-impact environments. By selecting the right type of liner, you can optimize the performance of your excavators and other heavy equipment.
Applications in protecting excavator buckets and chutes
Wear liners play a crucial role in protecting excavator buckets and chutes from premature wear. In mining operations, buckets often encounter abrasive materials like gravel, sand, and ore. Liners act as a shield, absorbing the impact and reducing the friction between the bucket and the material. This protection ensures that your buckets retain their structural integrity, even under demanding conditions.
Chutes, which transport materials in mining equipment, also benefit from wear liners. These liners prevent material buildup and reduce the risk of blockages, ensuring smooth and efficient operation. Whether you’re using skid-steers, loaders, or bulldozers, wear liners enhance the reliability and longevity of your equipment. Regular maintenance and replacement of liners can help you maintain peak performance and minimize downtime.
How YNF Machinery Supports Mining and Excavation Operations
YNF Machinery’s Excavator Couplings
Role in efficient power transmission
Efficient power transmission is essential for the smooth operation of mining equipment. YNF Machinery’s excavator couplings ensure that power flows seamlessly between the engine and the hydraulic pump system. These couplings are designed to handle the high torque demands of heavy equipment, making them indispensable for mining operations. By maintaining a secure connection, they minimize energy loss and enhance the overall efficiency of your machinery. This reliability allows you to focus on productivity without worrying about mechanical failures.
Benefits of durability and easy maintenance
Durability is a key feature of YNF Machinery’s excavator couplings. Built from high-quality materials, these components withstand the harsh conditions of mining environments. They resist wear and tear caused by constant use, ensuring a longer lifespan for your equipment. Additionally, their design simplifies maintenance. You can easily install or replace these couplings, reducing downtime and keeping your operations running smoothly. With YNF Machinery’s couplings, you invest in components that save time and costs while boosting performance.
YNF Machinery’s Excavator Engine Parts
Importance of high-quality engine components
The engine serves as the heart of any heavy equipment, especially in mining. High-quality engine components are crucial for maintaining the performance and reliability of your machinery. YNF Machinery’s excavator engine parts include pistons, cylinders, and crankshafts, all crafted to meet or exceed industry standards. These components endure extreme temperatures and pressures, ensuring that your equipment operates efficiently even in demanding conditions. By choosing reliable engine parts, you reduce the risk of breakdowns and extend the life of your machinery.
Enhancing performance and reducing downtime
Performance and uptime are critical in mining operations. YNF Machinery’s engine parts enhance the power and efficiency of your equipment, allowing it to handle heavy loads and challenging tasks with ease. These parts also contribute to fuel efficiency, lowering operational costs. Regular maintenance and timely replacement of worn components prevent unexpected failures, minimizing downtime. With YNF Machinery’s engine parts, you can keep your mining equipment running at peak performance, ensuring uninterrupted productivity.
Why Choose YNF Machinery for Heavy Equipment Wear Parts
Competitive pricing and rigorous quality standards
When it comes to mining equipment, cost-effectiveness and quality go hand in hand. YNF Machinery offers wear parts at competitive prices without compromising on quality. Each product undergoes rigorous quality inspections to meet the highest standards. This commitment ensures that you receive durable and reliable components for your heavy equipment. Whether you need bucket teeth, cutting edges, or other wear parts, YNF Machinery provides solutions that deliver exceptional value for your investment.
Comprehensive support and global reach
YNF Machinery stands out for its comprehensive support and global reach. The company provides detailed documentation and logistics assistance, making the purchasing process seamless. Their user-friendly platform allows you to order parts quickly and efficiently, no matter where you are. With over 35 years of experience, YNF Machinery has built a reputation for reliability and customer satisfaction. By choosing YNF Machinery, you gain access to high-quality wear parts and expert support that keeps your mining operations running smoothly.
How to Choose the Right Wear Parts for Mining and Excavation
Selecting the right wear parts is essential for maintaining the efficiency and durability of your mining equipment. By understanding your operational needs, evaluating material quality, and ensuring compatibility, you can optimize the performance of your heavy equipment and reduce downtime.
Assessing Operational Needs
Factors to consider (e.g., material type, operating conditions)
When choosing wear parts, start by assessing the specific requirements of your operations. Consider the type of material your equipment handles. For example, abrasive materials like rocks and gravel demand wear parts made from highly durable materials such as tungsten carbide or hardened steel. Softer materials may require less robust components but still need to withstand consistent use.
Operating conditions also play a significant role. Equipment used in high-impact environments, such as mining, requires wear parts that can endure extreme stress and abrasion. Temperature fluctuations, moisture levels, and exposure to corrosive elements should influence your decision. By aligning wear parts with your operational needs, you ensure that your mining equipment performs efficiently under all conditions.
Evaluating Material and Build Quality
Importance of durable materials (e.g., hardened steel, tungsten carbide)
The quality of wear parts directly impacts the longevity and performance of your heavy equipment. Durable materials like hardened steel and tungsten carbide are engineered to withstand the harsh demands of mining operations. These materials resist wear and tear, reducing the frequency of replacements and minimizing maintenance costs.
High-quality wear parts also enhance safety by maintaining the structural integrity of your equipment. For instance, protective wears like Poly-Cer not only extend wear life but also align maintenance cycles, reducing downtime and ensuring the safety of maintenance personnel. Investing in superior materials ensures that your equipment operates reliably, even in the most challenging environments.
Compatibility with Mining Equipment
Ensuring proper fit and functionality
Compatibility is a critical factor when selecting wear parts for mining equipment. Ill-fitting components can lead to inefficiencies, increased wear, and even equipment failure. Always verify that the wear parts match the specifications of your machinery. This includes checking dimensions, mounting systems, and material compatibility.
Properly fitted wear parts ensure seamless operation and optimal functionality. For example, wear liners designed for excavators protect buckets from abrasion while maintaining their shape and cutting edge. Similarly, crusher wear parts like jaw plates and mantles must fit precisely to ensure efficient ore processing. By prioritizing compatibility, you maximize the performance and lifespan of your mining equipment.
Cost vs. Longevity
Balancing upfront costs with long-term durability
When selecting wear parts for mining and heavy equipment, balancing upfront costs with long-term durability is crucial. While lower-cost options may seem appealing initially, they often lack the resilience needed to withstand the harsh conditions of mining operations. These parts wear out quickly, leading to frequent replacements, increased downtime, and higher maintenance expenses over time.
Investing in high-quality wear parts, such as those made from durable materials like tungsten carbide or high-grade steel, ensures better performance and longevity. For example, protective wears like Poly-Cer not only extend the lifespan of mining equipment but also align maintenance cycles, reducing operational interruptions. This durability minimizes the need for constant replacements, saving you money in the long run.
Durable wear parts also enhance the efficiency of your mining equipment. Components like crusher wear parts or excavator bucket liners maintain their structural integrity under extreme stress, ensuring consistent performance. By choosing reliable parts, you reduce the risk of unexpected breakdowns, which can disrupt mining operations and lead to costly delays.
To make an informed decision, consider the specific demands of your mining environment. Equipment used in high-impact or abrasive conditions requires wear parts engineered for maximum durability. While these parts may have a higher initial cost, their extended lifespan and reduced maintenance needs make them a cost-effective choice. Prioritizing quality over short-term savings ensures that your mining equipment operates efficiently and reliably, even in the most challenging conditions.
Benefits of Using High-Quality Wear Parts in Heavy Equipment
Enhanced Equipment Performance
Improved efficiency and productivity
High-quality wear parts significantly enhance the performance of your heavy equipment. These components are designed to endure the harsh conditions of mining operations, ensuring that your machinery operates at peak efficiency. For example, durable bucket teeth or cutting edges allow excavators to dig and move materials with precision and speed. This efficiency translates into higher productivity, enabling you to complete tasks faster and with less effort.
Reliable wear parts also reduce energy loss during operation. Components like hydraulic couplings, such as those offered by YNF Machinery, ensure seamless power transmission between the engine and other systems. This smooth transfer of energy minimizes mechanical strain, allowing your mining equipment to perform consistently under demanding conditions. By investing in high-quality wear parts, you maximize the output of your machinery while maintaining operational stability.
Reduced Downtime in Mining Operations
Minimizing maintenance and replacement frequency
Frequent maintenance and part replacements can disrupt your mining operations, leading to costly delays. High-quality wear parts help you minimize these interruptions by offering superior durability and resistance to wear and tear. For instance, robust crusher wear parts, such as jaw plates and mantles, withstand constant pressure and abrasion, reducing the need for frequent replacements.
Durable components also extend the lifespan of your mining equipment. Protective wear liners for buckets and chutes shield critical areas from damage, ensuring that your machinery remains functional for longer periods. With fewer breakdowns and maintenance requirements, you can focus on maintaining a steady workflow. YNF Machinery’s innovative spare parts, designed to endure harsh conditions, provide a reliable solution for minimizing downtime in your operations.
Cost Savings for Mining and Excavation
Long-term savings through durability and reliability
Investing in high-quality wear parts may seem costly upfront, but it offers substantial long-term savings. Durable components reduce the frequency of replacements, lowering your overall maintenance expenses. For example, wear parts made from materials like hardened steel or tungsten carbide resist abrasion and impact, ensuring that they last longer even in the toughest mining environments.
Reliable wear parts also improve fuel efficiency by maintaining the structural integrity of your equipment. Smooth operation reduces energy consumption, helping you save on operational costs. Additionally, fewer breakdowns mean less downtime, allowing you to maximize productivity and revenue. YNF Machinery’s commitment to providing innovative and durable spare parts ensures that you achieve cost-effectiveness without compromising on quality.
By choosing high-quality wear parts, you not only enhance the performance of your heavy equipment but also secure long-term financial benefits. These components protect your investment, ensuring that your mining operations remain efficient and profitable.
Maintenance Tips for Mining and Excavating Wear Parts
Proper maintenance of wear parts is essential to ensure the efficiency and longevity of your mining equipment. By following these practical tips, you can minimize downtime, reduce costs, and keep your heavy equipment operating at peak performance.
Regular Inspection of Wear Parts
Identifying signs of wear and damage
Frequent inspections are crucial for identifying early signs of wear and damage in mining and excavating wear parts. Look for visible cracks, deformation, or thinning in components like bucket teeth, cutting edges, and liners. Pay attention to unusual noises or vibrations during operation, as these may indicate internal issues. Regular checks allow you to address problems before they escalate, preventing costly repairs or equipment failure.
Pro Tip: Create a maintenance schedule to inspect wear parts after every significant operation or at regular intervals. This proactive approach ensures that no damage goes unnoticed.
Proper Installation of Heavy Equipment Components
Ensuring secure and correct attachment
Incorrect installation of wear parts can lead to inefficiencies and even equipment breakdowns. Always follow the manufacturer’s guidelines when attaching components like hydraulic couplings, bucket teeth, or ripper attachments. Use the appropriate tools to secure parts tightly and ensure proper alignment. Misaligned or loosely attached parts can cause uneven wear, reducing the lifespan of your mining equipment.
Quick Reminder: Double-check all connections after installation. A secure attachment not only enhances performance but also ensures safety during operation.
Cleaning and Lubrication of Wear Parts
Preventing corrosion and wear
Cleaning and lubrication are vital for maintaining the durability of wear parts in mining equipment. Dirt, debris, and moisture can accelerate corrosion and wear, especially in harsh mining environments. Clean components like conveyor belts, rollers, and bucket liners regularly to remove abrasive materials. Apply high-quality lubricants to moving parts to reduce friction and prevent overheating.
Maintenance Tip: Use specialized cleaning solutions and lubricants designed for heavy equipment. These products offer better protection against the extreme conditions encountered in mining operations.
By implementing these maintenance practices, you can extend the lifespan of your wear parts and improve the overall performance of your excavators and other heavy equipment. Consistent care not only reduces operational costs but also ensures that your mining equipment remains reliable and efficient.
Timely Replacement of Mining Wear Parts
Avoiding equipment failure and operational delays
Timely replacement of mining wear parts is essential for maintaining the efficiency and safety of your operations. Wear parts, such as bucket teeth, cutting edges, and liners, endure constant stress during mining activities. Over time, these components degrade, reducing their effectiveness and putting your equipment at risk of failure. By replacing worn parts promptly, you can prevent unexpected breakdowns that disrupt workflows and lead to costly delays.
Fact: Reliable wear parts protect critical components from premature damage, ensuring your mining equipment operates smoothly under demanding conditions.
Delaying the replacement of worn parts can result in severe consequences. Damaged wear parts compromise the performance of heavy equipment, increasing the strain on other components. For example, worn bucket teeth reduce digging efficiency, forcing excavators to work harder and consume more energy. This inefficiency not only slows down operations but also accelerates wear on other parts of the machine.
To avoid these issues, establish a proactive maintenance schedule. Regularly inspect your mining equipment for signs of wear, such as cracks, thinning, or deformation. Replace parts before they reach the end of their lifespan to maintain optimal performance. High-quality wear parts, designed to withstand harsh mining environments, offer extended durability and reduce the frequency of replacements.
Pro Tip: Keep spare wear parts in stock to ensure quick replacements and minimize downtime during critical operations.
Investing in timely replacements also enhances safety. Worn components increase the risk of equipment malfunctions, which can endanger operators and other personnel. By prioritizing the upkeep of wear parts, you create a safer working environment while maximizing the productivity of your mining equipment.
Mining and excavating wear parts are essential for maintaining the performance and durability of your heavy equipment. These components ensure that your mining equipment operates efficiently, even in the harshest conditions. By selecting the right types of mining wear parts and excavating wear parts, you can enhance productivity and reduce downtime. YNF Machinery provides high-quality solutions tailored to meet the demands of mining operations. Regular maintenance and timely replacement of wear parts protect your equipment and ensure long-term cost-effectiveness, keeping your operations running smoothly.
FAQ
What are wear parts, and why are they important in mining?
Wear parts are components designed to endure the harsh conditions of mining and heavy equipment operations. They protect critical machinery parts from abrasion, impact, and wear, ensuring smooth functionality. In mining, wear parts play a vital role in maintaining the efficiency and safety of equipment. By reducing the risk of breakdowns, they help you save on maintenance costs and extend the lifespan of your machinery.
Quick Fact: Reliable wear parts contribute to higher productivity by safeguarding equipment from premature damage.
How do I choose the right wear parts for my mining equipment?
To select the right wear parts, consider the type of material your equipment handles and the operating conditions. For abrasive materials like rocks, opt for parts made from durable materials such as hardened steel or tungsten carbide. Ensure compatibility with your equipment by checking dimensions and specifications. High-quality wear parts not only improve performance but also reduce downtime.
Pro Tip: Always consult your equipment manual or supplier for guidance on compatible wear parts.
How often should I replace wear parts in heavy equipment?
The replacement frequency depends on the intensity of use and the type of material being handled. Regular inspections can help you identify signs of wear, such as cracks, thinning, or deformation. Replace parts promptly to avoid equipment failure and operational delays. High-quality wear parts typically last longer, reducing the need for frequent replacements.
Reminder: Establish a maintenance schedule to monitor wear parts and ensure timely replacements.
Can high-quality wear parts save costs in mining operations?
Yes, investing in high-quality wear parts can lead to significant cost savings.
Did You Know? Reliable wear parts optimize operational expenses, allowing you to allocate funds to other critical areas.
What materials are commonly used in mining wear parts?
Mining wear parts are often made from materials like hardened steel, tungsten carbide, and rubber. Hardened steel offers excellent abrasion resistance, while tungsten carbide provides superior durability for high-impact environments. Rubber liners are ideal for reducing vibration and noise. The choice of material depends on the specific demands of your mining operation.
How do wear parts enhance the safety of mining equipment?
Wear parts protect critical components from damage, reducing the likelihood of equipment malfunctions. This protection ensures that your machinery operates smoothly, minimizing the risk of accidents. For example, well-maintained bucket teeth and cutting edges improve digging precision, preventing unexpected failures during operation.
Safety Tip: Regularly inspect wear parts to maintain a safe working environment for operators.
What maintenance practices can extend the lifespan of wear parts?
To extend the lifespan of wear parts, follow these maintenance practices:
Inspect wear parts regularly for signs of damage.
Clean components like bucket liners and conveyor belts to remove debris.
Lubricate moving parts to reduce friction and prevent overheating.
Replace worn parts promptly to avoid further damage.
Pro Tip: Use specialized cleaning solutions and lubricants designed for heavy equipment to ensure optimal performance.
Why is compatibility important when selecting wear parts?
Compatibility ensures that wear parts fit seamlessly with your mining equipment. Ill-fitting components can cause inefficiencies, uneven wear, and even equipment failure. Always verify dimensions, mounting systems, and material compatibility before purchasing wear parts. Properly fitted parts enhance functionality and extend the lifespan of your machinery.
How do technological advancements improve wear parts?
Advancements in material science have led to the development of more durable and efficient wear parts. Modern materials like tungsten carbide and advanced alloys offer superior resistance to abrasion and impact. These innovations maximize the lifespan of mining equipment, contributing to higher productivity and operational efficiency.
Fact: Technological improvements in wear parts reduce maintenance needs and enhance overall equipment performance.
Can YNF Machinery provide support for selecting wear parts?
Yes, YNF Machinery offers comprehensive support to help you choose the right wear parts for your mining and heavy equipment. With over 35 years of experience, they provide high-quality components tailored to meet the demands of mining operations. Their expert team ensures that you receive reliable solutions to keep your equipment running efficiently.