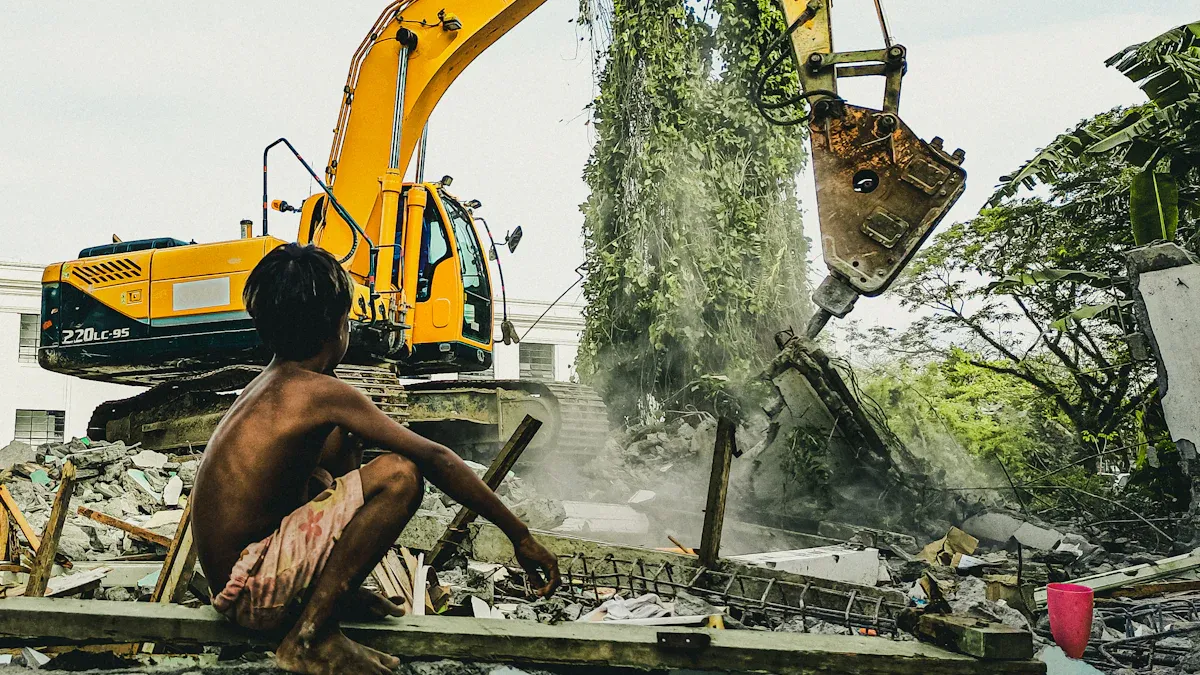
Excavator breakers are powerful tools designed to break through tough materials like concrete and rock, and they rely on various excavator breaker parts to function effectively. For instance, the breaker’s weight should match 10% of the excavator’s weight for optimal performance. A 10-ton excavator would require a 1-ton breaker, while smaller machines like skid steers need proportionally lighter breakers. Hydraulic systems play a key role, with oil flow rates and operating pressure ensuring smooth operation. Matching the hydraulic requirements of the excavator breaker parts with the excavator’s capabilities is critical for efficiency. Each part contributes to the breaker’s ability to deliver high-impact blows.
Key Takeaways
The breaker should weigh about 10% of the excavator’s weight.
Check all main parts often to find damage or wear early.
Add grease to the chisel and bushings every two hours to make them last longer.
Pick the correct chisel type for the material and job to work better.
Keep hydraulic fluid clean and at the right level to stop overheating and keep it running smoothly.
Hydraulic System in Excavator Breaker Parts
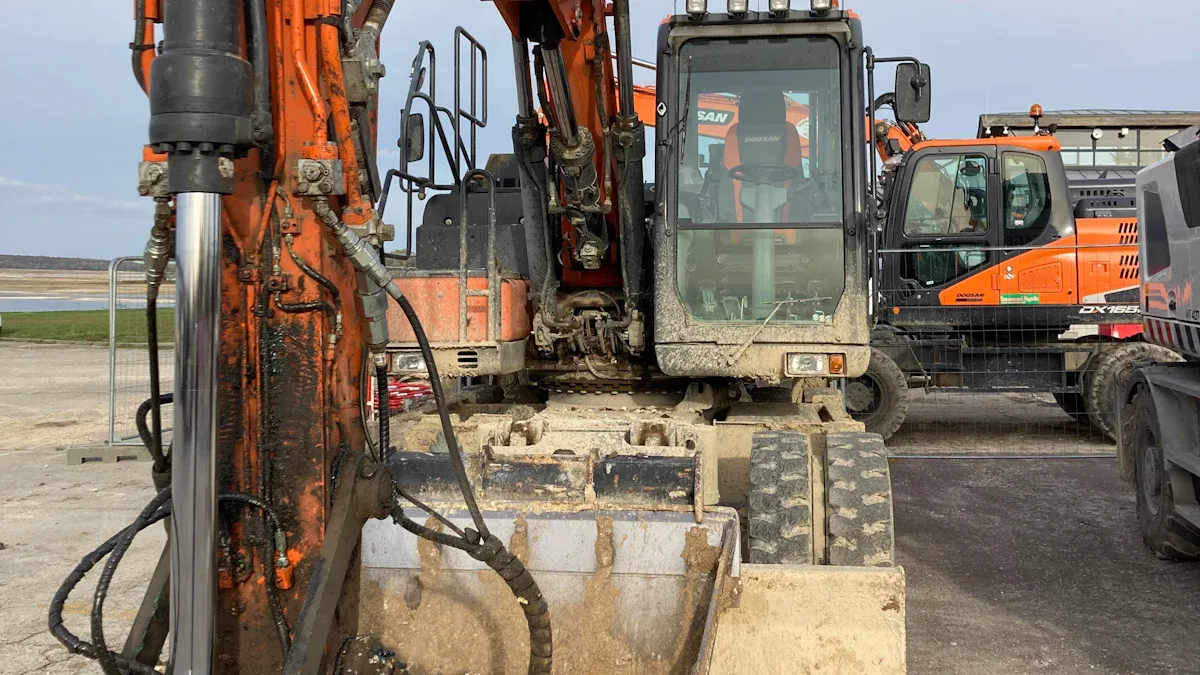
The hydraulic system is the backbone of excavator breakers, converting hydraulic energy into the mechanical force needed to break tough materials. This system consists of several critical components that work together to ensure efficient operation.
Hydraulic Pump
The hydraulic pump is one of the most vital excavator components. It pressurizes the hydraulic fluid, which powers the breaker. This pressurized fluid drives the piston inside the cylinder, creating the high-impact blows necessary for breaking concrete or rock. For instance, a typical hydraulic pump in an excavator breaker operates with an oil flow rate of 230 liters per minute and an operating pressure of 180 bar. These specifications ensure the pump delivers consistent power to the breaker.
Hydraulic Hoses
Hydraulic hoses transport the pressurized fluid from the pump to the breaker. These hoses must withstand high pressure and extreme conditions. Their durability ensures the hydraulic system operates without interruptions. The efficiency of the hoses directly impacts the performance of the excavator breaker. Without reliable hoses, the hydraulic fluid cannot reach the breaker, leading to a loss of power.
Control Valves
Control valves regulate the flow and pressure of the hydraulic fluid within the system. They ensure the fluid reaches the breaker at the right pressure and flow rate. This regulation is crucial for maintaining the efficiency of the breaker. For example, the input power of a hydraulic system is 69 kW, while the output power is 42 kW, resulting in an efficiency of approximately 61%. Properly functioning control valves help achieve this level of efficiency by optimizing fluid distribution.
The hydraulic system is one of the major parts of an excavator. Its components, including the pump, hoses, and valves, play a crucial role in the overall performance of the excavator breaker. Understanding these parts of an excavator can help you maintain and operate your equipment effectively.
Chisel or Working Tool
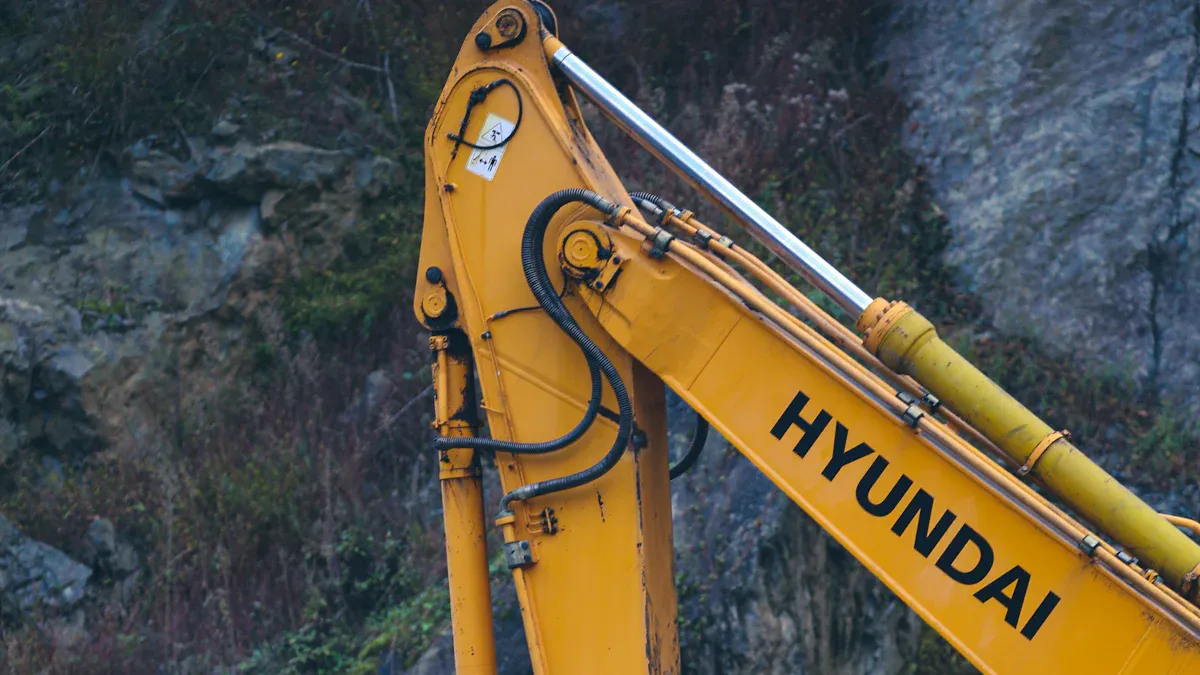
The chisel, also known as the working tool, is one of the most critical components of an excavator breaker. It directly interacts with the material being broken, making it essential for efficient operation.
Types of Chisels
Excavator breakers use different types of chisels, each designed for specific tasks. Common types include:
Moil Point Chisels: Ideal for general-purpose breaking, especially in concrete and rock.
Flat Chisels: Best suited for cutting and shaping materials.
Blunt Chisels: Used for crushing and compacting hard surfaces.
Specialty Chisels: Designed for unique applications, such as trenching or demolition.
Choosing the right chisel depends on the material and the task. For example, moil point chisels excel in breaking hard rock, while flat chisels are better for precision work.
Function of the Chisel
The chisel plays a vital role in transferring energy from the hydraulic system to the material. Hydraulic breaker hammers convert hydraulic energy into mechanical energy, which the chisel delivers as powerful blows. Made from hardened steel, the chisel withstands extreme forces and temperatures during operation.
Advanced chisels often include energy recovery systems. These systems utilize rebound energy from strikes, improving efficiency and reducing wear. For instance, manufacturers like Soosan focus on maximizing the transfer of hydraulic energy into kinetic energy, ensuring minimal energy loss due to heat or vibration.
The Association of Equipment Manufacturers (AEM) has developed a universal testing system to compare hydraulic breakers objectively. This system highlights the importance of factors like impact rate and working tool diameter in evaluating performance. A hydraulic breaker with an oil flow rate of 230 l/min and an operating pressure of 180 bar achieves an input power of 69 kW, showcasing the efficiency of well-designed chisels.
By selecting the appropriate chisel and maintaining it properly, you can enhance the performance of your excavator breaker and complete tasks more efficiently.
Housing and Protection
Outer Casing
The outer casing of an excavator breaker serves as a protective shield for its internal components. It ensures that the power cell and other critical parts remain safe from external damage during operation. This design is especially important when working in harsh environments where debris and impacts are common.
Modern hydraulic breakers often feature monobloc designs, which are crafted from a single piece of durable steel. This construction enhances the durability of the breaker while reducing maintenance needs. Fewer moving parts mean fewer opportunities for wear and tear, allowing you to focus on the task at hand. Additionally, the weight of the breaker head, determined by its casing and materials, directly impacts its efficiency in breaking through tougher materials like concrete and rock.
Key Benefits of Outer Casing:
Protects the power cell from damage.
Reduces maintenance requirements due to robust design.
Enhances the longevity of the breaker through durable steel construction.
By ensuring the outer casing is in good condition, you can maximize the lifespan and performance of your excavator breaker.
Noise and Vibration Dampening
Noise and vibration dampening are essential features of modern excavator breaker designs. These features not only improve operator comfort but also make the equipment suitable for use in noise-sensitive areas, such as urban construction sites.
Breakers with boxed housings are specifically designed to suppress noise levels. For instance, models like Epiroc’s EC breakers use polyurethane-lined boxes to dampen both noise and vibration. Without such mitigation, hydraulic breakers typically operate in the 90- to 100-decibel range, which can be disruptive. Advanced vibration-reduction technology also minimizes the stress transmitted to the excavator’s arm, prolonging its lifespan and reducing operator fatigue.
Advantages of Noise and Vibration Dampening:
Quieter operation for urban and residential projects.
Enhanced operator comfort through reduced vibrations.
Prolonged excavator arm lifespan due to lower stress levels.
By prioritizing these features, you can ensure a safer and more efficient working environment while protecting your equipment from unnecessary wear.
Piston and Cylinder Mechanism
The piston and cylinder mechanism is the heart of an excavator breaker. These components work together to convert hydraulic energy into the mechanical force needed to break tough materials like concrete and rock. Understanding their roles can help you optimize the performance of your equipment.
Piston
The piston is a critical part of the mechanism. It moves within the cylinder, delivering high-impact blows to the chisel. Pressurized hydraulic fluid from the excavator propels the piston, creating the force required for breaking materials. This movement is essential for transferring energy efficiently.
Manufacturers design pistons to withstand extreme forces. For example, some hydraulic breakers use a small piston to generate immense breaking force. This force is then amplified through mechanical advantage, allowing the breaker to handle even the toughest materials. To enhance durability, many pistons are made from hardened steel and feature simplified designs with fewer components. This reduces wear and tear, ensuring a longer lifespan.
Field testing often evaluates piston performance under real-world conditions. These tests focus on energy transfer, ensuring the piston converts hydraulic energy into kinetic energy effectively. Advanced designs also include features like blank firing protection, which prevents wear during misfires by using a hydraulic cushion.
Cylinder
The cylinder houses the piston and plays a vital role in the mechanism. It provides the space for the piston to move and ensures the hydraulic fluid remains pressurized. The cylinder’s design directly impacts the efficiency and durability of the breaker.
Different types of cylinders offer unique advantages. For instance, double-acting cylinders provide force in both directions, making them versatile for various applications. Tie-rod cylinders, on the other hand, are easier to disassemble, simplifying maintenance and repair.
Performance metrics like mechanical and volumetric efficiency help compare cylinder designs. Mechanical efficiency reflects torque losses, while volumetric efficiency measures the impact of leakage flow on performance. A well-designed cylinder minimizes leakage, reducing power loss and operational costs.
To maximize durability, some manufacturers use single-casting construction methods for cylinders. This approach improves strength and reduces the risk of failure. For example, Epiroc’s Solid Body breakers utilize this technique to enhance longevity.
By maintaining the piston and cylinder mechanism, you can ensure your excavator breaker operates at peak efficiency. Regular inspections and proper lubrication are essential for preventing wear and extending the life of these components.
Maintenance Tips for Major Parts of an Excavator Breaker
Proper maintenance ensures your excavator breaker operates efficiently and lasts longer. By focusing on regular inspection, lubrication, and cleaning, you can prevent costly repairs and downtime.
Regular Inspection
Frequent inspections are essential for keeping your excavator in top condition. Check all major components daily, including the hydraulic system, chisel, and housing. Look for signs of wear, leaks, or damage.
“Frequent inspections are the cornerstone of effective maintenance, ensuring your excavator operates smoothly and safely.”
Performing these checks allows you to identify and address issues early. For example, inspecting the chisel for cracks or deformation ensures it remains effective during operation. Regularly changing the engine oil and filter, as recommended by the manufacturer, also contributes to smooth performance.
Lubrication
Lubrication plays a critical role in maintaining the parts of an excavator breaker. Apply grease to the chisel and bushings every two hours during operation to reduce wear caused by vibration and heat. Use the correct type of grease, such as molybdenum-based grease or chisel paste, for optimal results.
Molybdenum-based grease withstands high temperatures, exceeding 500°F.
Chisel paste, with copper and graphite particles, provides enhanced lubrication for hydraulic breaker tool steel.
Proper lubrication prevents contamination and extends the service life of your equipment. Always follow the manufacturer’s guidelines for lubrication intervals and grease types.
Cleaning
Keeping your excavator breaker clean prevents dirt and debris from damaging its components. After each use, remove any accumulated material from the chisel, housing, and hydraulic hoses. Store the breaker in a clean, dry location to avoid contamination.
“By performing these daily maintenance checks, operators can detect and address any issues promptly, ensuring that the excavator is in optimal condition for safe and efficient operation throughout the workday.”
A clean breaker not only performs better but also lasts longer. Regular cleaning minimizes the risk of corrosion and ensures all parts function as intended.
By following these maintenance tips, you can maximize the performance and longevity of your excavator breaker while reducing ownership costs.
Hydraulic Fluid Maintenance
Maintaining hydraulic fluid is essential for keeping your excavator breaker running smoothly. The hydraulic system relies on clean and sufficient fluid to deliver power efficiently. Neglecting this maintenance can lead to overheating, reduced performance, and costly repairs. By following a few key steps, you can ensure your equipment operates at its best.
Check Hydraulic Fluid Levels Regularly
Always monitor the fluid levels before starting your equipment. Low levels can cause the system to overheat and lose power. Topping up the fluid as needed prevents these issues and ensures consistent performance.Inspect Hoses and Connections
Examine hydraulic hoses and connections for any signs of leaks or damage. Even small leaks can reduce system pressure and affect the breaker’s efficiency. Replacing damaged hoses promptly helps maintain optimal performance.Clean Hydraulic Filters
Dirty or clogged filters can block fluid flow, reducing the system’s responsiveness. Regularly cleaning or replacing filters ensures the hydraulic fluid circulates freely, keeping the system in peak condition.
Tip: Use only the hydraulic fluid recommended by the manufacturer. Using the wrong type can damage the system and void warranties.
Hydraulic fluid plays a critical role in the operation of your excavator breaker. It powers the hydraulic pump, piston, and other components, ensuring smooth and responsive control. Without proper maintenance, the system can overheat, leading to reduced power and efficiency. Regular checks and cleaning keep the fluid free of contaminants, extending the life of your equipment.
By prioritizing hydraulic fluid maintenance, you can avoid unnecessary downtime and maximize the performance of your excavator breaker. A well-maintained hydraulic system not only saves money but also ensures your equipment is ready for any challenge.
Excavator breakers rely on well-designed parts to deliver consistent performance and durability. Using fewer moving components enhances reliability, while high tensile strength materials absorb power effectively without compromising stability. Regular maintenance ensures long-term performance and reduces downtime.
Key Benefits of Maintenance:
Identifies minor issues early, preventing costly repairs.
Prolongs equipment lifespan and enhances safety for operators.
Understanding how each part functions protects your investment and ensures reliable operation. For professional guidance, consult an equipment specialist to maximize your breaker’s efficiency and longevity.
“A well-maintained excavator breaker is your key to efficient and safe operations.”
FAQ
What is the most important part of an excavator breaker?
Each part is crucial, but the hydraulic system stands out. It powers the breaker and ensures efficient operation. Without it, the breaker cannot deliver the high-impact blows needed for breaking tough materials.
How often should you lubricate the chisel?
You should apply grease to the chisel and bushings every two hours during operation. This reduces wear caused by heat and vibration, ensuring the breaker performs efficiently.
Can you use any hydraulic fluid for your breaker?
No, always use the hydraulic fluid recommended by the manufacturer. Using the wrong type can damage the system and void warranties. Check the manual for specific fluid requirements.
How do you reduce noise from an excavator breaker?
Choose a breaker with noise-dampening features like boxed housings or polyurethane liners. These reduce noise levels, making the equipment suitable for urban or residential projects.
Why is regular inspection important?
Frequent inspections help you identify wear, leaks, or damage early. Addressing these issues promptly prevents costly repairs and ensures your breaker operates safely and efficiently.
Tip: Keep a checklist for daily inspections to avoid missing critical components.