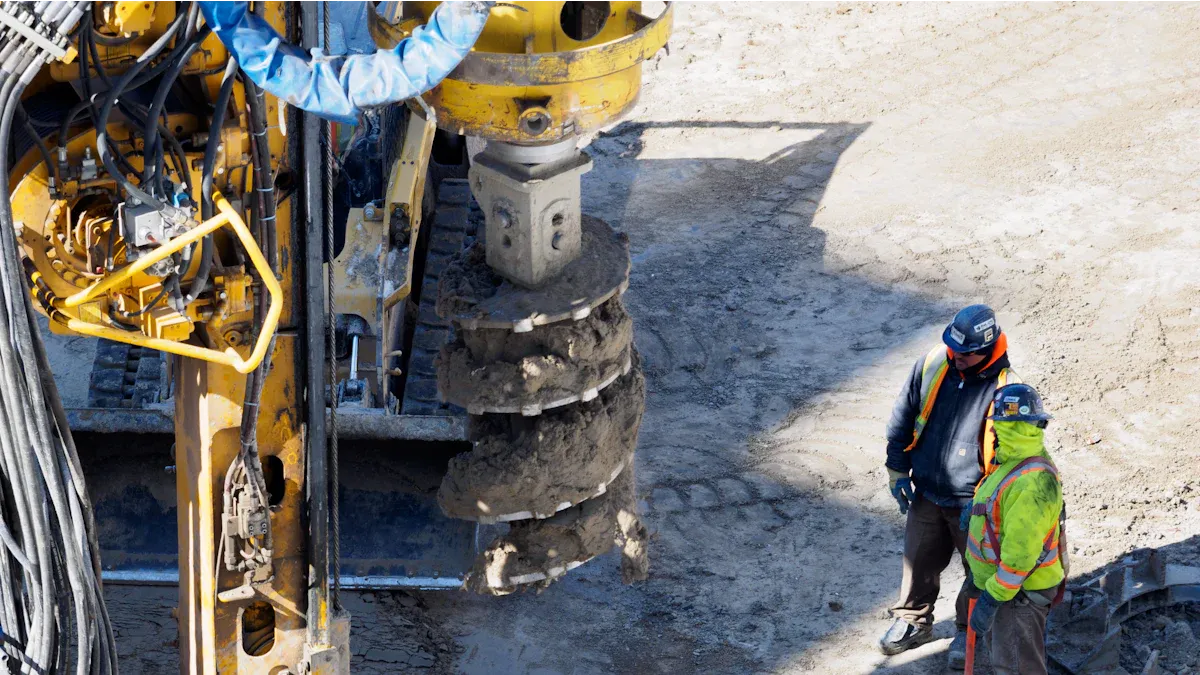
Understanding the excavator parts list is essential for keeping your machine in top condition. Regular excavator maintenance can improve performance by up to 30%, ensuring faster project completion and reduced fuel consumption. Neglecting minor issues often leads to costly repairs or downtime, which can range from $448 to $760 per day. Accurate identification of parts from the excavator parts list allows you to address problems early, extending the lifespan of your equipment and maximizing return on investment. YNF Machinery supports you with high-quality excavator parts, making repairs and replacements seamless and efficient.
Key Takeaways
Regular maintenance can make excavators work 30% better. This helps finish jobs faster and saves fuel money.
Finding and changing old parts early stops big repairs. It also makes your excavator last longer.
Check hydraulic fluid and engine parts often. This finds problems before they get worse.
Use good-quality parts from trusted brands like YNF Machinery. This makes repairs reliable and efficient.
Keep the cabin safe and comfy for operators. Comfortable designs help workers stay productive and less tired.
Excavator Parts List and Their Functions
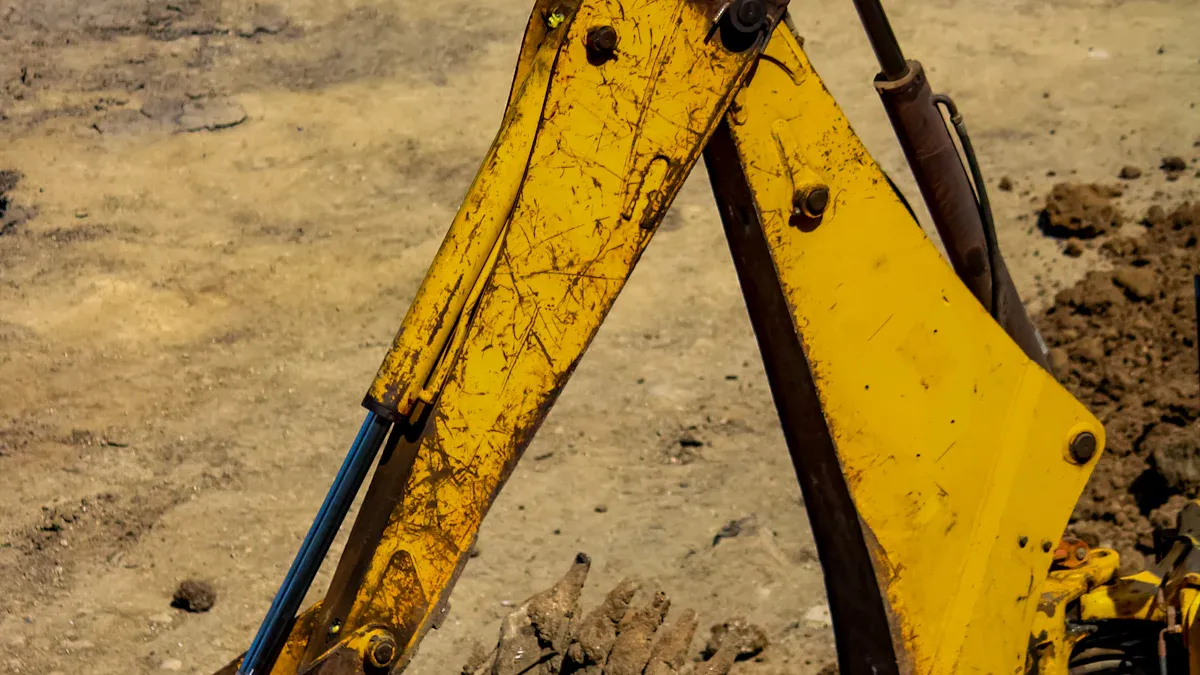
Engine System
Excavator Engine Parts Overview
The engine system serves as the powerhouse of your excavator, converting fuel into mechanical energy to drive the machine. Diesel engines are commonly used due to their efficiency and durability in heavy-duty applications. Accurate identification of engine parts ensures smooth operation and prevents costly breakdowns. Components like pistons, crankshafts, and bearings work together to maintain the engine’s performance. Reading and interpreting diagrams can help you locate these parts quickly, making repairs more efficient. High-quality diagrams also simplify identifying specific parts, ensuring you select the correct replacement.
Key Components: Pistons, Crankshafts, and Bearings
Pistons compress the air-fuel mixture, enabling combustion that powers the engine. Crankshafts convert this energy into rotational motion, driving the excavator’s functions. Bearings reduce friction between moving parts, ensuring smooth operation. Regular inspection of these components is vital. Identifying specific parts early can prevent engine failure and extend the lifespan of your equipment.
Hydraulic System
Hydraulic Cylinder Seal Kits and Their Role
The hydraulic system enables your excavator to perform tasks like digging, lifting, and moving heavy materials. Hydraulic cylinder seal kits prevent oil leaks, ensuring the system operates efficiently. These kits consist of high-grade materials designed to withstand pressure and vibration. Accurate identification of leaks and timely replacement of seals can prevent further damage. This maintenance step is crucial for keeping your excavator in optimal condition.
Hydraulic Pumps and Control Valves
Hydraulic pumps generate the pressure needed to operate the cylinders, while control valves direct the fluid flow. This combination allows precise movement of the excavator’s arm and attachments. The system minimizes energy loss and maximizes power output, enhancing operational efficiency. Correct identification of these components ensures seamless repairs and replacements, reducing downtime.
Undercarriage Components
Tracks and Rollers
The undercarriage supports the excavator’s weight and ensures mobility. Tracks provide traction and stability, while rollers brace the track chains and distribute the machine’s weight. Proper maintenance of these components extends the life of your excavator undercarriage. Cleaning the tracks and monitoring wear can prevent costly repairs.
Sprockets and Their Maintenance
Sprockets engage with the track chains, maintaining alignment and functionality. They also repel dirt, reducing wear and tear. Regular inspection and replacement of worn sprockets are essential for smooth operation. Accurate identification of sprocket issues can save you from unexpected breakdowns.
Attachments
Buckets and Quick Couplers
Attachments enhance the versatility of your excavator, allowing it to perform a wide range of tasks. Buckets are among the most common attachments. They come in various types, such as rock buckets for heavy-duty excavation and grading buckets for fine leveling. Quick couplers simplify the process of switching between attachments, saving time and effort during operations. Regular inspection of these components ensures they remain functional and safe to use.
Specialized Attachments for Versatility
Excavators can be equipped with specialized attachments to handle specific tasks efficiently:
Hammers: Ideal for demolition, capable of breaking through concrete, asphalt, and rock.
Thumbs: Assist in material handling, enabling precise picking and placing of large objects.
Grapples: Useful for sorting and moving bulky materials like logs and debris.
Augers: Designed for drilling holes in landscaping or construction projects.
Choosing the right attachment for your excavator ensures optimal performance and reduces wear on the machine.
Electrical System
Batteries and Wiring Harnesses
The electrical system powers essential functions of your excavator, including starting the engine and operating lights. Batteries supply the necessary energy, while wiring harnesses distribute it to various components. Regularly check the battery voltage and inspect wiring for signs of wear or damage. Proper maintenance prevents electrical failures and ensures uninterrupted operation.
Sensors and Their Importance
Sensors play a critical role in monitoring the performance of your excavator. They detect issues like overheating, low hydraulic pressure, or engine malfunctions. Faulty sensors can lead to inaccurate readings, compromising safety and efficiency. Replacing malfunctioning sensors promptly ensures your excavator operates at peak performance.
Operator’s Cabin
Control Panels and Joysticks
The operator’s cabin serves as the command center of your excavator. Control panels and joysticks allow precise operation of the machine. Ergonomically positioned controls reduce strain on the operator, improving productivity. Regular cleaning and inspection of these components ensure they function smoothly.
Comfort Features: Seats and Ergonomics
Modern excavator cabins prioritize operator comfort and safety. Features like climate control systems protect operators from extreme weather. Ergonomic seating with lumbar support minimizes fatigue during long hours of operation. The table below highlights key ergonomic features:
Feature | Description |
---|---|
Climate Control Systems | Protects operators from extreme weather conditions, enhancing comfort during operation. |
Visibility Enhancements | Armored glass windows and ample cabin space improve visibility, crucial for safety. |
Ergonomic Seating | Seats with lumbar support and various configurations cater to individual comfort needs. |
Advanced Control Systems | Ergonomically positioned controls reduce strain and improve ease of operation. |
Investing in a well-maintained cabin enhances operator efficiency and reduces the risk of accidents.
Maintenance Tips for Excavator Parts
Engine System Maintenance
Regular Oil Changes and Air Filter Replacements
Maintaining the engine system is crucial for your excavator’s performance. Regular oil changes every 250 to 500 operating hours prevent wear and overheating. Clean oil ensures smooth operation and reduces the risk of engine damage. Similarly, replacing air filters keeps debris out of the engine, improving combustion efficiency. Check fluid levels, including engine oil and coolant, during daily maintenance checks. These simple steps extend the lifespan of your engine and reduce the need for costly repairs.
Inspecting Excavator Engine Assembly Components
Inspecting the engine assembly components ensures your excavator operates efficiently. Focus on pistons, crankshafts, and bearings, as these parts endure high stress. Look for signs of wear or damage, such as unusual noises or reduced power. Accurate identification of issues early on prevents engine failure. Use high-quality diagrams to locate components quickly and ensure proper replacement. Scheduling professional inspections can also help catch hidden problems before they escalate.
Hydraulic System Maintenance
Checking Hydraulic Cylinder Seal Kits for Leaks
Hydraulic systems power your excavator’s movements, making leak prevention essential. Regularly inspect hydraulic cylinder seal kits for signs of oil leakage. Early detection prevents further damage and ensures system efficiency. Tighten loose connections and replace worn seals promptly. Using quality replacement parts minimizes the risk of future leaks. A structured maintenance schedule helps you stay on top of these tasks.
Maintaining Hydraulic Fluid Levels
Maintaining optimal hydraulic fluid levels is vital for preventing cavitation and ensuring smooth operation. Use high-quality hydraulic fluid that meets the manufacturer’s specifications. Monitor fluid levels daily and top up as needed. Replace hydraulic fluid every 1,000 to 2,000 operating hours to maintain system efficiency. Proper fluid management reduces wear on components and extends the life of your excavator.
Undercarriage Maintenance
Cleaning Tracks and Monitoring Wear
The undercarriage supports your excavator’s weight and ensures mobility. Daily cleaning removes dirt and debris that can accelerate wear. Inspect tracks for signs of damage or uneven wear. Check sprockets, rollers, and idlers for loose or missing parts. Monitoring these components prevents unexpected breakdowns. Keep the undercarriage clean and maintain proper track tension to ensure smooth operation.
Replacing Worn Rollers and Sprockets
Worn rollers and sprockets can compromise your excavator’s performance. Inspect these parts regularly for wear or damage. Accurate identification of issues allows timely replacement, reducing downtime. Use heavy equipment replacement parts that meet high-quality standards to ensure durability. Replacing these components as needed keeps your excavator undercarriage in top condition.
Attachment Maintenance
Greasing Pivot Points
Proper lubrication of pivot points is essential for reducing friction and wear on your excavator’s attachments. Grease these points regularly to ensure smooth movement and prevent premature damage. Use high-quality lubricants that meet the manufacturer’s specifications. During daily maintenance checks, inspect the pivot points for signs of wear or insufficient lubrication. Neglecting this step can lead to costly repairs and reduced efficiency.
To enhance the longevity of your attachments, follow these practices:
Clean the attachment thoroughly to remove dirt and debris.
Apply a rust inhibitor or protective oil to exposed metal surfaces.
Store attachments in a dry, covered area to prevent moisture exposure.
Inspecting Attachments for Cracks
Regular inspections help you identify minor cracks or damage before they escalate into major issues. Focus on wear parts like bucket teeth and cutting edges. Replace these parts based on wear levels or manufacturer guidelines. Consider the intensity of usage and operating conditions when determining replacement frequency. Early identification of cracks ensures safe operation and reduces the risk of accidents. Using heavy equipment replacement parts that meet high-quality standards guarantees durability and reliability.
Electrical System Maintenance
Testing Battery Voltage
The electrical system powers critical functions of your excavator. Testing the battery voltage regularly ensures consistent performance. Use a multimeter to check the voltage and confirm it meets the recommended range. Secure all wiring connections and inspect for signs of corrosion. If you encounter blown fuses, identify the root cause before replacing them to prevent recurring issues. Regular inspections of the electrical system help you catch problems early, minimizing downtime and repair costs.
Ensuring Proper Sensor Functionality
Sensors monitor vital parameters like hydraulic pressure and engine temperature. Faulty sensors can lead to inaccurate readings, compromising safety and efficiency. Inspect sensors during routine excavator maintenance to ensure they function correctly. Replace malfunctioning sensors promptly with quality replacement parts to maintain optimal performance. This proactive approach prevents common excavator maintenance issues and enhances operational reliability.
Cabin Maintenance
Cleaning and Inspecting Controls
The operator’s cabin is the command center of your excavator. Clean the control panels and joysticks regularly to remove dust and debris. Inspect these components for signs of wear or malfunction. Proper maintenance of controls ensures precise operation and reduces the risk of errors. Keeping the cabin clean also improves visibility and safety during operation.
Ensuring Operator Comfort and Safety
A comfortable operator is a productive operator. Modern cabins feature ergonomic seating and climate control systems to enhance comfort. For example, the Cabin Cool system can reduce the surrounding air temperature by up to 25 degrees, minimizing fatigue and improving productivity. Adjustable settings allow operators to customize their environment, ensuring safety and comfort during long hours of operation. Maintaining these features reduces the need for frequent breaks and enhances overall efficiency.
Signs That Excavator Parts Need Replacement
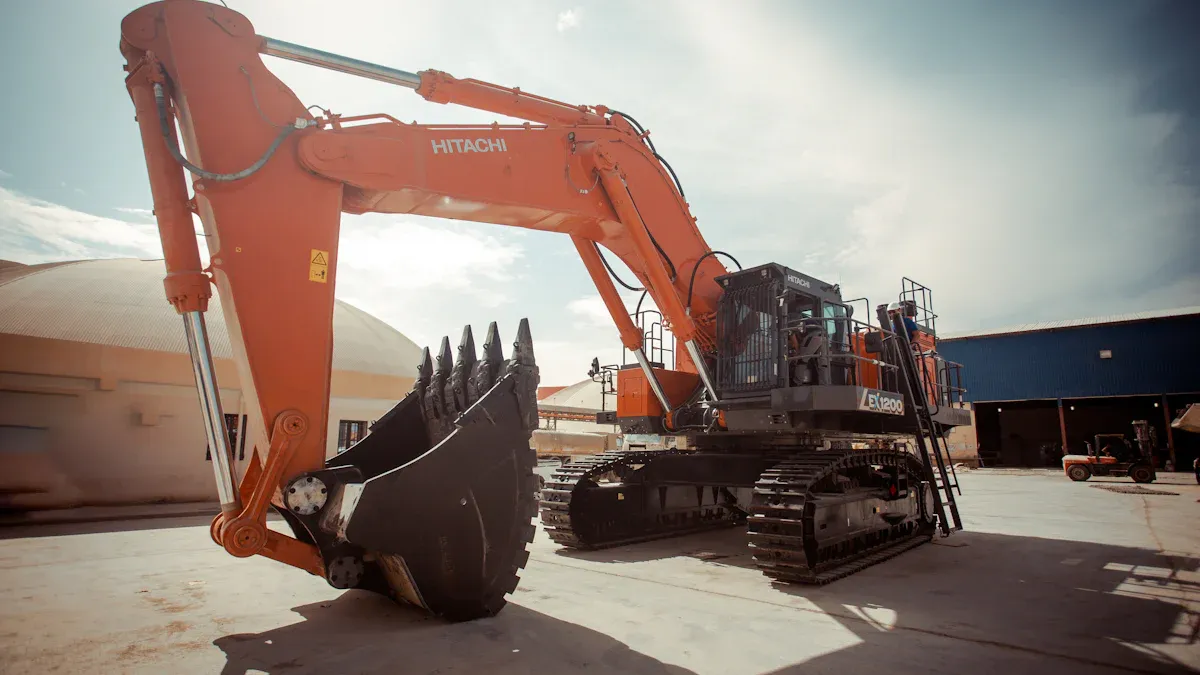
Engine System
Unusual Noises or Excessive Smoke
Your excavator’s engine often signals problems through unusual noises or excessive smoke. Listen for knocking or rattling sounds, which may indicate worn pistons or crankshafts. Excessive smoke from the exhaust, whether black, blue, or white, suggests issues like incomplete combustion, oil leaks, or coolant entering the combustion chamber. These signs require immediate attention to prevent further damage. Regular identification of these symptoms helps you avoid costly excavator repairs and downtime.
Other warning signs include overheating, fluid leaks, or engine stalling. Addressing these issues promptly ensures your excavator continues to perform efficiently.
Difficulty Starting or Reduced Power
Engines that struggle to start or exhibit reduced power often have underlying issues. Faulty injectors, clogged fuel filters, or worn-out bearings can disrupt the engine’s performance. If your excavator loses power during operation, inspect the engine assembly for damage. Early identification of these problems prevents complete engine failure.
Routine maintenance, such as replacing air filters and checking fuel systems, keeps the engine in optimal condition. These steps also reduce the likelihood of unexpected breakdowns.
Hydraulic System
Slow or Unresponsive Movements
Hydraulic systems power your excavator’s movements. When the system becomes slow or unresponsive, it may indicate low hydraulic fluid levels or damaged hoses. Reduced lifting power or unusual noises during operation also signal potential issues. Regularly inspect hydraulic components to ensure they function correctly.
To maintain efficiency, check fluid levels daily and replace hydraulic filters as needed. These simple steps prevent contamination and ensure smooth operation.
Visible Leaks in Hydraulic Cylinder Seal Kits
Oil leaks in hydraulic cylinder seal kits compromise the system’s performance. Look for visible leaks around the cylinders or connections. Damaged seals, worn hoses, or loose fittings often cause these leaks. Replacing faulty seals promptly prevents further damage and ensures your excavator operates efficiently.
Using high-quality seal kits during repairs minimizes the risk of recurring leaks. Regular inspections help you identify and address these issues early.
Undercarriage
Uneven Wear on Tracks
Uneven wear on tracks reduces traction and stability, affecting your excavator’s mobility. Thinning, cracks, or loss of traction on track shoes are common signs of wear. Misaligned tracks or damaged idlers can also cause uneven wear. Regular cleaning and inspection of the undercarriage prevent these problems.
Maintaining proper track tension and replacing worn components ensures smooth operation. These practices extend the lifespan of your excavator’s undercarriage.
Loose or Damaged Rollers
Rollers support the track chains and distribute the excavator’s weight. Excessive noise, vibration, or oil leaks from rollers indicate damage. Loose rollers can lead to misaligned tracks, reducing efficiency. Inspect rollers regularly and replace them when necessary.
Accurate identification of worn rollers prevents further damage to the undercarriage. Using durable replacement parts ensures long-lasting performance.
Attachments
Reduced Efficiency in Digging or Lifting
When your excavator struggles with digging or lifting, it signals potential issues with its attachments. Worn-out bucket teeth or cutting edges often reduce efficiency. Overloading attachments beyond their capacity can also cause stress and damage. Regular inspections help you identify these problems early. Neglecting lubrication leads to excessive friction, accelerating wear. Inexperienced operators applying unnecessary force may further strain attachments. Using high-quality attachments and maintaining them properly ensures optimal performance.
To maintain efficiency, follow these tips:
Inspect attachments daily for wear or damage.
Lubricate pivot points regularly to reduce friction.
Avoid overloading attachments to prevent stress on components.
Visible Cracks or Deformation
Cracks or deformation in attachments compromise safety and functionality. These issues often result from prolonged use or operating in harsh conditions. Minor cracks can escalate into major failures if left unchecked. Regularly inspect attachments for visible damage, especially in high-stress areas like bucket edges or quick couplers. Replace damaged parts promptly to avoid accidents. High-quality excavator parts ensure durability and reliability during repairs.
Tip: Use a flashlight to inspect hard-to-see areas for cracks or deformation. Early identification prevents costly excavator repair needs.
Electrical System
Flickering Lights or Faulty Sensors
Flickering lights or malfunctioning sensors indicate electrical system issues. Faulty connections, battery failure, or blown fuses often cause these problems. Sensors play a critical role in monitoring your excavator’s performance. When they fail, inaccurate readings can compromise safety. Regularly inspect wiring for damage and ensure connections are secure. Replace faulty sensors promptly to maintain operational efficiency.
Error Codes on the Control Panel
Error codes on the control panel provide valuable clues about electrical faults. These codes often point to issues like low battery voltage or sensor malfunctions. Diagnosing these problems involves checking battery terminals for corrosion, inspecting wiring, and replacing blown fuses. Addressing these issues early prevents further complications.
Common Electrical Problems and Diagnosis Steps:
Check battery terminals for corrosion and ensure tight connections.
Inspect wiring for visible damage.
Replace blown fuses to restore functionality.
Operator’s Cabin
Malfunctioning Controls
Malfunctioning controls reduce precision and increase the risk of accidents. Dust and debris often cause joysticks or control panels to stick. Regular cleaning and inspection keep these components in good condition. If controls feel unresponsive, check for loose connections or worn-out parts. Replacing damaged controls ensures smooth operation and enhances safety.
Worn-Out Seats or Joysticks
Worn-out seats or joysticks affect operator comfort and productivity. Torn seat covers or broken joysticks make long hours of operation challenging. Inspect these components regularly and replace them when necessary. Investing in ergonomic seating and high-quality joysticks improves operator efficiency.
Note: Comfortable operators are more productive. Prioritize cabin maintenance to enhance safety and reduce fatigue.
How to Source and Replace Excavator Parts
Sourcing Parts
Choosing Between OEM and Aftermarket Parts
When sourcing excavator parts, you must decide between OEM (Original Equipment Manufacturer) and aftermarket options. Each choice has unique advantages:
OEM Parts: These parts meet strict quality standards and fit perfectly with your excavator. They often come with warranties, ensuring reliability and peace of mind.
Aftermarket Parts: These parts are more affordable and widely available, especially for older equipment. They also offer customization options for specific needs.
However, aftermarket parts can vary in quality. To avoid performance issues, source them from reputable suppliers. Accurate identification of your needs ensures you choose the right option for your excavator repair or maintenance.
Why YNF Machinery is a Trusted Supplier
YNF Machinery simplifies the process of sourcing high-quality replacement parts. With over 35 years of experience, YNF provides reliable excavator parts for various brands. Their products undergo rigorous quality checks, ensuring durability and performance. YNF offers both OEM and aftermarket options, catering to different budgets and requirements. Their user-friendly platform and expert support make identifying specific parts and ordering seamless.
Replacing Parts
Tools Required for Replacement
Replacing excavator parts requires the right tools for efficiency and safety. Common tools include:
Wrenches and screwdrivers for loosening and tightening bolts.
A hydraulic jack for lifting heavy components.
A multimeter for testing electrical parts.
Having these tools ready ensures smooth repairs and minimizes downtime.
Step-by-Step Guide for Common Replacements
Follow this step-by-step guide for replacing worn parts:
Use excavator parts diagrams to locate the faulty component.
Disconnect power sources to ensure safety.
Remove the damaged part using appropriate tools.
Install the new part, ensuring proper alignment.
Test the excavator to confirm functionality.
This process ensures accurate identification and proper installation, reducing the risk of future issues.
Ensuring Compatibility
Correct Identification of Part Numbers
Correct identification of part numbers is crucial for sourcing compatible parts. Check the excavator manual or the part itself for these numbers. Using excavator parts diagrams can also help you verify compatibility. Keeping a record of part numbers simplifies future replacements.
Consulting the Excavator Manual
The excavator manual is an essential resource for identifying specific parts. It provides detailed diagrams and specifications, ensuring you select the right replacement parts. Always consult the manual before ordering to avoid compatibility issues.
Troubleshooting Common Issues with Excavator Parts
Hydraulic System Issues
Diagnosing and Fixing Leaks
Hydraulic leaks are among the most common issues you may encounter. These leaks often result from worn hoses, damaged seals, or loose connections. To address this, inspect the hydraulic hoses and connections regularly. Look for visible signs of wear, such as cracks or oil seepage. Tighten any loose fittings and replace damaged seals promptly. Maintaining proper hydraulic fluid levels is equally important. Contaminated or low fluid can exacerbate leaks and reduce system efficiency. Flushing the hydraulic system periodically removes sludge and particulates, ensuring smooth operation. Regular maintenance and early identification of leaks prevent costly repairs and downtime.
Resolving Slow Movement Problems
Slow or unresponsive movements in your excavator often indicate hydraulic system issues. Low fluid levels, clogged filters, or damaged pumps can restrict fluid flow. Start by checking the hydraulic fluid levels and topping them up if necessary. Inspect the filters for blockages and replace them if needed. Damaged pumps or control valves may require professional repair or replacement. Regular servicing of the hydraulic system ensures optimal performance and prevents recurring problems.
Electrical System Issues
Fixing Wiring Problems
Electrical wiring problems can disrupt your excavator’s functionality. Loose connections, corroded terminals, or damaged wires are common culprits. Begin by inspecting the battery terminals. Clean them using a wire brush and a mixture of baking soda and water. Ensure all connections are tight and secure. Examine the wiring for visible damage, such as frays or breaks, and replace faulty wires immediately. Regular checks and proper maintenance of the electrical system minimize the risk of wiring issues.
Replacing Faulty Sensors
Faulty sensors can lead to inaccurate readings, affecting your excavator’s performance. To resolve this, identify the malfunctioning sensor using the control panel’s error codes. Replace the faulty sensor with a compatible one, ensuring proper alignment during installation. Testing the new sensor after replacement confirms its functionality. Regular sensor inspections and timely replacements keep your excavator operating efficiently.
Undercarriage Issues
Addressing Track Misalignment
Track misalignment reduces your excavator’s stability and mobility. Misaligned tracks often result from loose bolts, worn rollers, or damaged idlers. Inspect the track chains for loose or missing bolts. Tighten or replace them as needed. Check the rollers and idlers for cracks or oil leaks, and address any damage promptly. Proper alignment ensures smooth operation and extends the lifespan of your undercarriage components.
Replacing Worn Sprockets
Worn sprockets compromise the efficiency of your excavator’s undercarriage. Look for signs of wear, such as rounded teeth or misalignment. Replace worn sprockets immediately to prevent further damage to the track chains. Regular inspections and timely replacements ensure your excavator remains in top condition. Using high-quality replacement parts enhances durability and reduces the need for frequent repairs.
Tip: Regular cleaning of the undercarriage after use removes debris that can accelerate wear and tear. This simple step improves the longevity of your excavator parts.
Engine Issues
Resolving Overheating
Overheating is one of the most frequent problems in excavators. It often results from coolant leaks, clogged radiators, or faulty thermostats. You can prevent this issue by regularly checking coolant levels and inspecting the radiator for blockages. A clean radiator ensures proper airflow, which helps regulate engine temperature. Faulty thermostats can also disrupt the cooling system. Replacing them promptly restores the system’s efficiency.
To identify overheating early, monitor the temperature gauge on your excavator. If the needle moves into the red zone, stop the machine immediately. Allow the engine to cool before inspecting it. Look for visible signs like steam or fluid leaks around the radiator. Regular maintenance, such as flushing the cooling system and replacing old coolant, minimizes the risk of overheating.
Tip: Always use the coolant recommended by the manufacturer. Mixing incompatible coolants can reduce efficiency and damage the engine.
Addressing Fuel System Problems
Fuel system problems can disrupt your excavator’s performance. Common issues include fuel contamination, clogged filters, or faulty injectors. Contaminated fuel often leads to engine stalling or power loss. To prevent this, use clean fuel and store it in sealed containers. Regularly inspect and replace fuel filters to maintain smooth fuel flow.
Faulty fuel injectors can cause uneven combustion, reducing engine power. You can identify this issue by observing symptoms like rough idling or excessive smoke. Replacing damaged injectors ensures efficient fuel delivery. Additionally, inspect the fuel pump for blockages or wear. A well-maintained fuel system improves engine performance and reduces the need for frequent repairs.
Note: Perform daily checks for leaks in the fuel lines. Early identification of leaks prevents further damage and ensures safety during operation.
Understanding the excavator parts list and performing regular excavator maintenance are essential for keeping your machine in peak condition. Routine inspections, such as checking hydraulic fluid levels and examining tracks for wear, help identify issues early. Proactive maintenance improves performance, reduces fuel consumption, and extends the lifespan of your excavator. YNF Machinery simplifies part identification and provides high-quality excavator parts to ensure reliable operation. By addressing minor problems promptly and keeping spare parts on hand, you can avoid costly downtime and maximize productivity.
Tip: Prioritize preventive maintenance to enhance safety and efficiency while reducing long-term costs.
FAQ
What is the most important part of an excavator to maintain regularly?
The hydraulic system requires regular maintenance. Check fluid levels daily and inspect for leaks or worn seals. This ensures smooth operation and prevents costly repairs. Neglecting this system can lead to reduced performance and downtime.
How often should you replace an excavator’s air filter?
Replace the air filter every 250 to 500 operating hours. This keeps debris out of the engine and ensures efficient combustion. Regular checks help you identify when the filter becomes clogged or damaged.
Can you use aftermarket parts for excavator repairs?
Yes, aftermarket parts offer a cost-effective alternative to OEM parts. Ensure they meet quality standards and fit your machine. Reputable suppliers like YNF Machinery provide reliable aftermarket options for various excavator models.
How do you identify the correct replacement part for your excavator?
Refer to the excavator manual for part numbers and specifications. Use diagrams to locate the faulty component. Contact a trusted supplier like YNF Machinery for assistance in finding compatible parts.
What tools are essential for replacing excavator parts?
You’ll need wrenches, screwdrivers, a hydraulic jack, and a multimeter. These tools help you safely and efficiently replace components. Having the right tools minimizes downtime and ensures proper installation.