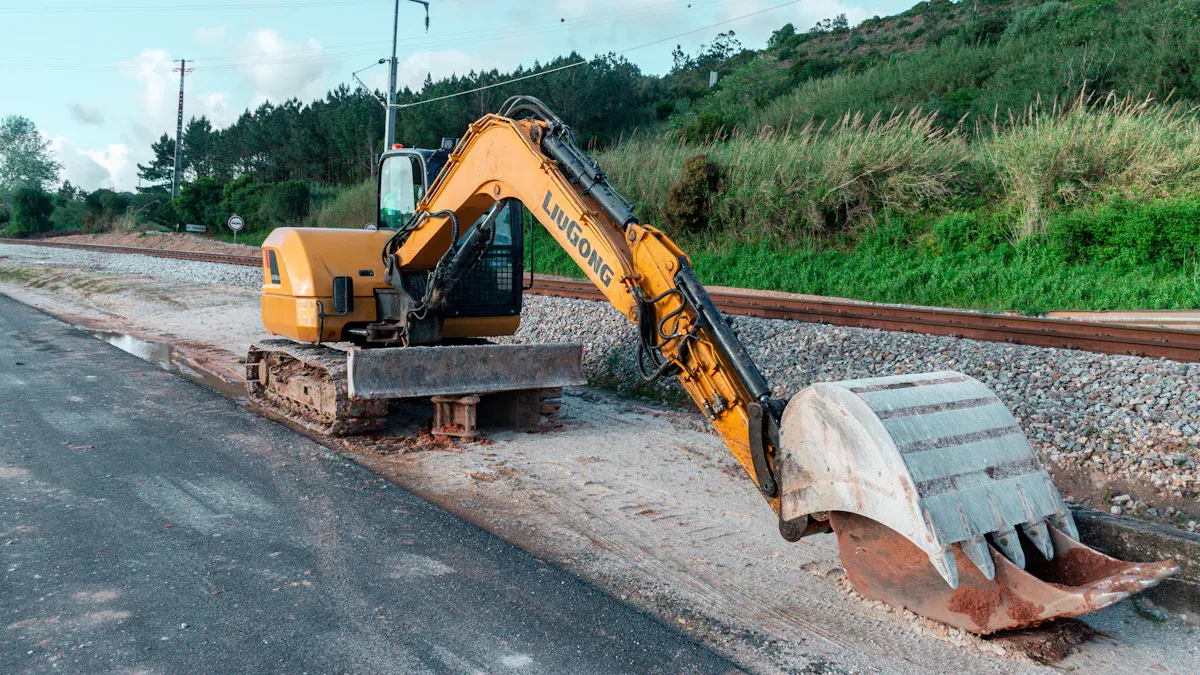
Knowing the excavator undercarriage parts name and the job of each part helps you a lot. When you understand these excavator undercarriage parts name, you can take better care of your excavator. This helps your machine last longer. Experts say you should match the right track style to your ground. You should also keep the tracks straight. This stops expensive damage. If you clean and check your excavator every day, you can find problems early. This helps you avoid big breakdowns. Studies show that how long the undercarriage lasts depends on your work site and how well you care for the parts. When you learn about each excavator undercarriage parts name, you can make better choices. This means less downtime and better excavator work.
Key Takeaways
Knowing each excavator undercarriage part and what it does helps you find problems early. This keeps your machine working well.
Checking and cleaning your machine often stops expensive repairs. It can also make your undercarriage parts last up to 30% longer.
Keeping the tracks tight and using the right track shoes makes the machine more stable. It also stops damage from happening.
Greasing moving parts every day lowers friction and wear. This helps your excavator last longer and work better.
Changing old parts like sprockets, rollers, and idlers on time stops bigger problems. It also keeps your excavator safe.
Undercarriage Overview
What Is an Undercarriage
You can think of the undercarriage as the foundation of your excavator. This part sits at the bottom of the machine and supports all the weight. The undercarriage connects the upper structure to the ground. It lets your excavator move, turn, and stay stable on different surfaces. Leading manufacturers list several main structural components in the undercarriage:
Tracks: These give your excavator mobility. You will find steel or rubber tracks, depending on the job.
Rollers: Top (carrier) and bottom (track) rollers guide and support the tracks.
Idlers: These sit at the front and rear of the track frame. They keep the track tight and help it move smoothly.
Sprockets: These toothed wheels drive the tracks and send power from the engine.
Track Chains and Links: These connect the track pads and form the backbone of the tracks.
Track Shoes or Pads: These come in different widths and types. They help your excavator grip the ground and protect the tracks.
The undercarriage holds all these components together. Each one plays a role in how your excavator moves and works.
Why It Matters
The undercarriage does more than just hold up your excavator. It affects how well your machine works and how long it lasts. If you keep the undercarriage in good shape, you get better performance and save money on repairs. Here is a table showing how each component helps with stability and movement:
Component | Function in Stability and Movement |
---|---|
Track Chains | Link and move the tracks, letting your excavator travel. |
Track Shoes | Spread out the weight and give traction, especially on rough ground. |
Sprockets | Drive the tracks forward or backward. |
Rollers | Support the weight and keep the tracks lined up. |
Idlers | Keep the track tight and in place. |
Idler Spring | Absorbs shocks and keeps the ride smooth. |
Track Adjuster | Keeps the track at the right tension for best performance. |
You need to check your undercarriage often. Regular inspections can help your excavator last longer. Studies show that if you inspect your undercarriage every 2,000 hours, you can extend the life of the components from about 50-65% to almost 95%. This saves you a lot of money over time. Good maintenance also helps you avoid breakdowns and keeps your excavator working when you need it most.
Excavator Undercarriage Parts Name
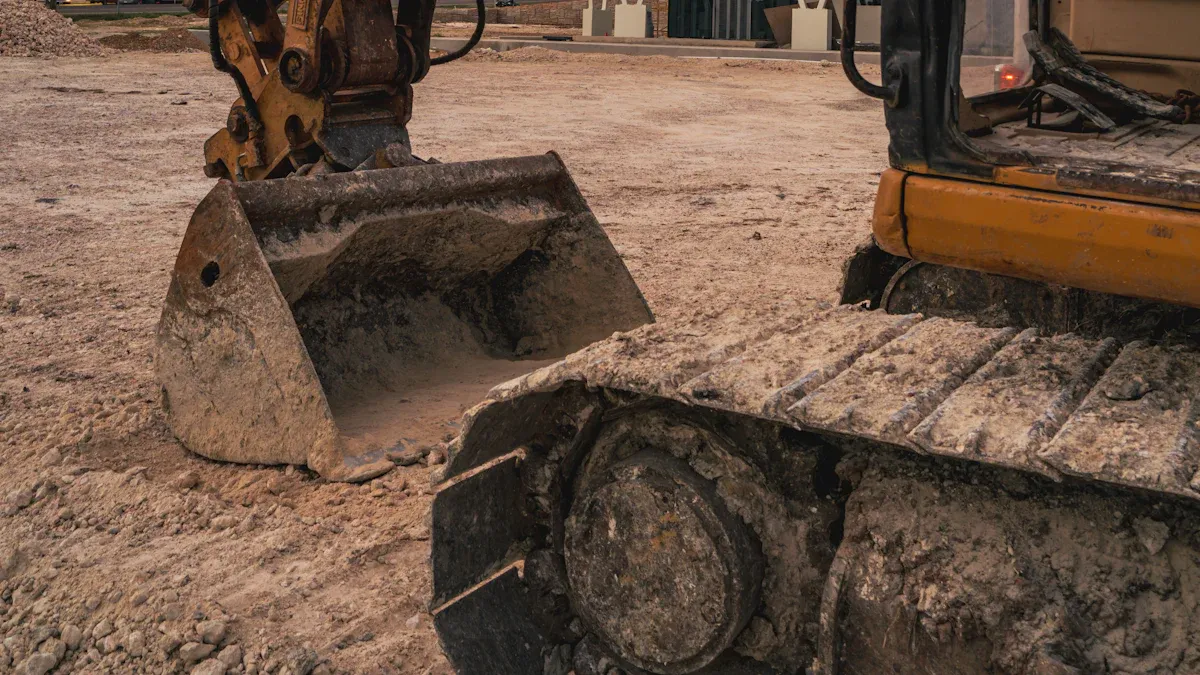
When you look at the essential parts of an excavator, the undercarriage stands out as the foundation. Each component has a unique job that helps your excavator move, dig, and stay stable. Here, you will learn the excavator undercarriage parts name and what each one does.
Track Chains
Track chains connect the track shoes and form the backbone of the tracks. You will find these chains made from high-strength alloy steel. This material goes through special heat treatment to boost wear resistance and fatigue strength. The chain plates carry the main load, while the connecting pins act like rivets. These pins need to resist heavy wear and impact to keep the chain flexible and prevent breakage. The choice of material affects how long the chains last. Steel chains work well for heavy loads and tough conditions, but they are heavy and less flexible. Rubber chains absorb shocks and reduce vibration, but they wear out faster in harsh environments. Most excavator track chains last between 3,000 and 5,000 hours if you maintain them well. You should inspect for wear, keep the tension right, and clean debris to extend their life.
Tip: If you work in rocky or abrasive areas, you may need wear-resistant chains. These last longer but cost more and need extra care.
Track Shoes
Track shoes attach to the track chains and help your excavator grip the ground. The design of the shoes affects traction and ground pressure. Wider shoes and higher grousers (the raised ridges) give better traction, especially on sand or soft soil. Each extra shoe can boost traction by about 30%. Some shoes use special shapes, like those inspired by ostrich feet, to improve grip by over 40%. You can choose single, double, or triple ridge shoes. Single ridge shoes work best on hard ground. Double ridge shoes help on mixed terrain. Triple ridge shoes balance traction and smooth movement on soft or medium-hard ground. Steel shoes last longer and give strong grip on rough terrain, but they can damage paved surfaces. Rubber pads protect pavement and lower ground pressure but do not grip as well on rough ground.
Track shoes spread the excavator’s weight, stopping it from sinking on soft ground.
The right shoe design keeps your machine stable and safe.
Track Rollers
Track rollers sit under the track frame and support the weight of your excavator. These rollers guide the tracks and keep them lined up as you move. They also help the tracks roll smoothly over the ground. Tough jobs, rocky ground, and poor driving habits can wear out rollers quickly. You can slow down wear by keeping the rollers clean, using the right track tension, and training operators to avoid sharp turns or high speeds. If you see uneven wear or hear grinding noises, check the rollers right away. Replacing worn rollers keeps your tracks running straight and protects other components.
Carrier Rollers
Carrier rollers sit above the track frame. They support the top part of the tracks and help spread the excavator’s weight. By guiding the track chain, carrier rollers stop the tracks from slipping or coming off. They also keep the load balanced and reduce stress on other parts. Good carrier rollers make your excavator run smoother and last longer. If you notice the tracks sagging or hear odd noises, check the carrier rollers for wear.
Carrier rollers help distribute weight and keep the tracks aligned.
They reduce pressure on single parts and prevent uneven wear.
Idlers
Idlers guide the track chain and keep it tight. You will find idlers at the front or rear of the undercarriage. They do not carry the excavator’s weight but make sure the track stays in line and does not derail. Idlers also absorb shocks and vibrations as you move over rough ground. If the idler fails, the track can slacken, drift, or even come off. Well-maintained idlers spread out stress, protect other components, and help your undercarriage last longer. You should check idlers for cracks, misalignment, or signs of wear.
Sprockets
Sprockets are toothed wheels that drive the tracks. They transfer power from the engine to the track chains, making your excavator move forward or backward. Worn sprocket teeth cannot grip the chains well, causing power loss and jerky movement. Signs of sprocket trouble include smaller teeth, cracks, chipped teeth, or grinding noises. If you ignore these signs, you risk damaging the chains, bearings, and other components. You should inspect sprockets every 1,000 hours and replace them if you see shark fin-shaped teeth or other damage. Keeping sprockets in good shape ensures smooth movement and saves you from costly repairs.
Recoil Springs
Recoil springs act as shock absorbers in the undercarriage. They protect the track and idler system from impacts and heavy loads. These springs keep the track tension right by compressing when the idler moves back over rough terrain. This automatic tension adjustment helps your excavator perform well and extends the life of the undercarriage. If the recoil spring fails, you may see loose tracks or uneven movement. Regular checks for leaks, damage, or weak tension help keep the springs working.
Recoil springs prevent damage to sensitive parts and reduce wear.
They are key to smooth operation and long undercarriage life.
Track Frame
The track frame holds all the undercarriage components together. It attaches the undercarriage to the main body of the excavator. Made from high-strength steel, the frame uses ribs and special designs to handle heavy loads and absorb shocks. The frame spreads the excavator’s weight and keeps the machine stable, even on uneven ground. Good track frames use strong bolts and have features to stop the tracks from derailing. You should keep the frame clean, check for cracks, and make sure all bolts are tight.
Aspect | Description |
---|---|
Material | High-strength steel with wear resistance |
Features | Ribs for strength, roller paths for weight spread, anti-derailment guides |
Fastening | High-grade bolts with precise torque |
Design | Reduces ground pressure, absorbs shocks, improves contact area |
Impact Resistance | Built to handle rough work and absorb impacts |
Rock Guards
Rock guards protect the undercarriage from rocks, sand, and debris. They form a barrier that deflects or absorbs impacts, keeping critical parts like sprockets, rollers, and track chains safe. Rock guards reduce friction and stop debris from jamming moving parts. Made from tough steel alloys, they cover the undercarriage fully and fit precisely. This protection lowers maintenance costs and keeps your excavator running longer, even in harsh conditions.
Note: Rock guards also help keep the undercarriage clean, which makes daily checks and repairs easier.
Pins and Bushings
Pins and bushings connect the links in the track chains. They let the chains bend and move smoothly around the sprockets and idlers. These components face heavy wear, especially in tough soil or rocky ground. Pins and bushings usually last between 2,000 and 7,000 hours, depending on the terrain and how well you maintain them. If you see loose links or hear clanking noises, check the pins and bushings for wear. Replacing them on time prevents bigger problems with the chains and tracks.
Bolts and Nuts
Bolts and nuts hold the undercarriage components together. They secure the track shoes, rollers, sprockets, and other parts to the frame. High-grade bolts resist loosening from vibration and heavy use. If bolts or nuts come loose, you risk losing parts or damaging the undercarriage. You should check all bolts and nuts during regular maintenance. Tighten or replace any that show signs of wear or damage.
Reminder: Using the right torque when tightening bolts and nuts keeps the undercarriage safe and stable.
When you know each excavator undercarriage parts name and its function, you can spot problems early and keep your machine running smoothly. These major parts of an excavator work together to support movement, stability, and long service life. Regular checks and good care of these components of the undercarriage will help you get the most from your excavator.
Additional Excavator Machine Parts Name
When you look at the excavator machine parts name list, you find several important components beyond the basic undercarriage. These extra parts help your excavator work better and last longer. Let’s look at three major parts of an excavator that play a big role in how your machine moves and stays stable.
Track Adjuster
The track adjuster helps you set and keep the right tension on your tracks. This part uses a cylinder to move the idler wheel forward or backward. You usually adjust it when the excavator is parked. Keeping the correct track tension is important because loose tracks can slip off, while tight tracks can wear out fast. The track adjuster works with the recoil spring to protect other components from damage.
Track adjusters set the initial tension by moving the idler wheel.
Recoil springs absorb shocks and keep the tension steady during work.
The track spring assembly protects the undercarriage and other components from impacts.
Tip: Check your track adjuster often. If you see slack or hear noise from the tracks, you may need to adjust the tension.
Yoke
The yoke connects the idler wheel to the frame and keeps your tracks lined up. This part helps your excavator stay stable on rough ground. When the yoke holds the idler in the right spot, your tracks grip better and wear evenly. If the yoke gets bent or loose, you might see uneven wear or even track derailment. The yoke supports the weight of the excavator and spreads it across the tracks, which helps all components last longer.
Proper alignment of the yoke means your excavator moves smoothly and stays balanced. You should check the yoke for cracks or misalignment during regular maintenance.
Final Drive
The final drive is one of the most important excavator machine parts name you will find. This component sends power from the engine to the tracks. It changes hydraulic energy into mechanical force, so your excavator can move and turn on different surfaces. The final drive uses a gearbox to slow down the engine’s speed and increase torque. This gives your excavator the strength to dig, lift, and travel over tough ground.
Function | Description |
---|---|
Power Transmission | Sends power from the engine and hydraulic system to the tracks, so your excavator can move. |
Speed Reduction | Slows down the motor speed for better control and more power. |
Torque Multiplication | Increases force for digging and lifting heavy loads. |
You should keep the final drive clean and check for leaks or strange noises. Good care of this component helps your excavator run smoothly and keeps all undercarriage components working well.
Undercarriage Maintenance
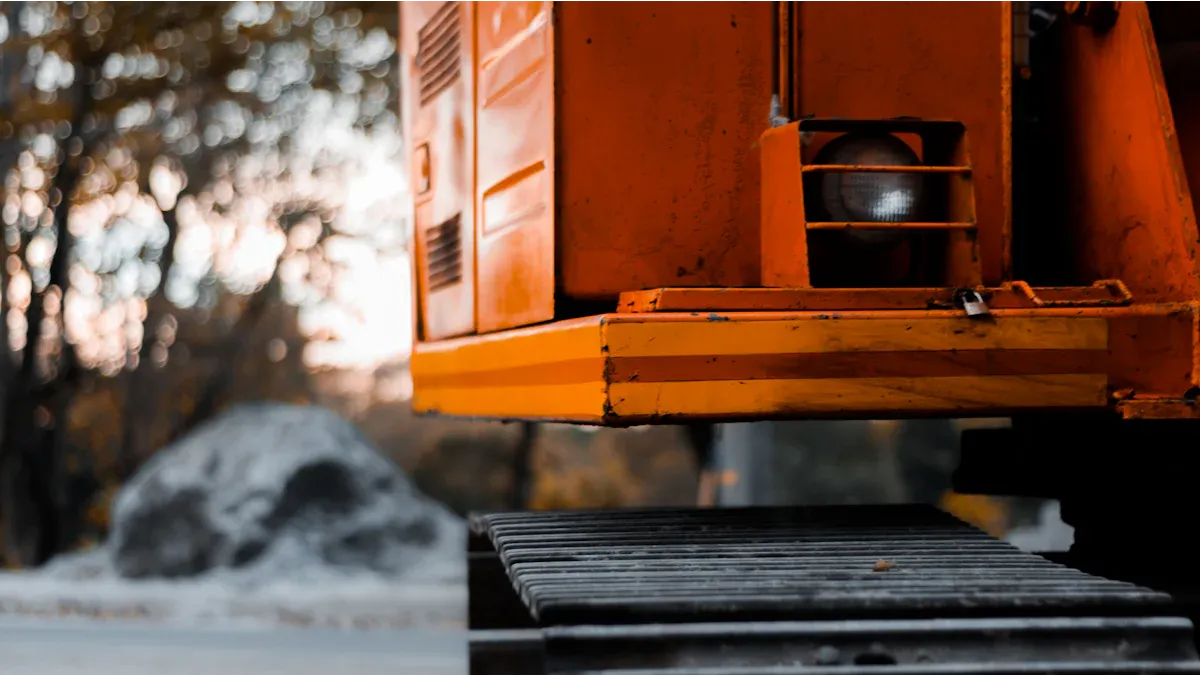
Taking care of your excavator’s undercarriage parts saves money. It also helps you avoid machine downtime. Good maintenance makes your machine last longer and work better. You can follow these tips to keep your excavator in great shape.
Inspection Tips
Check your excavator every day. Look for loose bolts and worn tracks. Check for damaged rollers too. Watch for leaks near the idlers and sprockets. Use this easy inspection schedule to help you remember:
Every day, look for wear, debris, and loose parts on tracks, rollers, idlers, and sprockets.
Each week, check tracks and undercarriage parts closely. Measure tread wear and replace worn parts.
Once a month, adjust track tension and clean the undercarriage. Use a pressure washer for best cleaning.
Every 50-100 hours, grease pivot points and change hydraulic drive motor oil.
Every 500 hours, replace case drain filters and check rollers, idlers, and sprockets.
Operating Hour Interval | Recommended Inspection and Maintenance Tasks |
---|---|
As Required | Look over, clean, adjust track tension, check or replace sprockets and tracks, tighten bolts and nuts |
8-10 Hours | Check fluid levels, inspect battery, grease pivot points |
50 Hours | Change fuel filter, adjust fan belt, change final drive oil |
100 Hours | Change hydraulic drive motor oil, check track tension |
250 Hours | Check and replace sprockets and tracks, check bolts and nuts |
500 Hours | Replace case drain filters, check rollers, idlers, and sprockets |
1,000 Hours | Major service, oil changes, check components |
2,000 Hours | Overhaul or replace big parts |
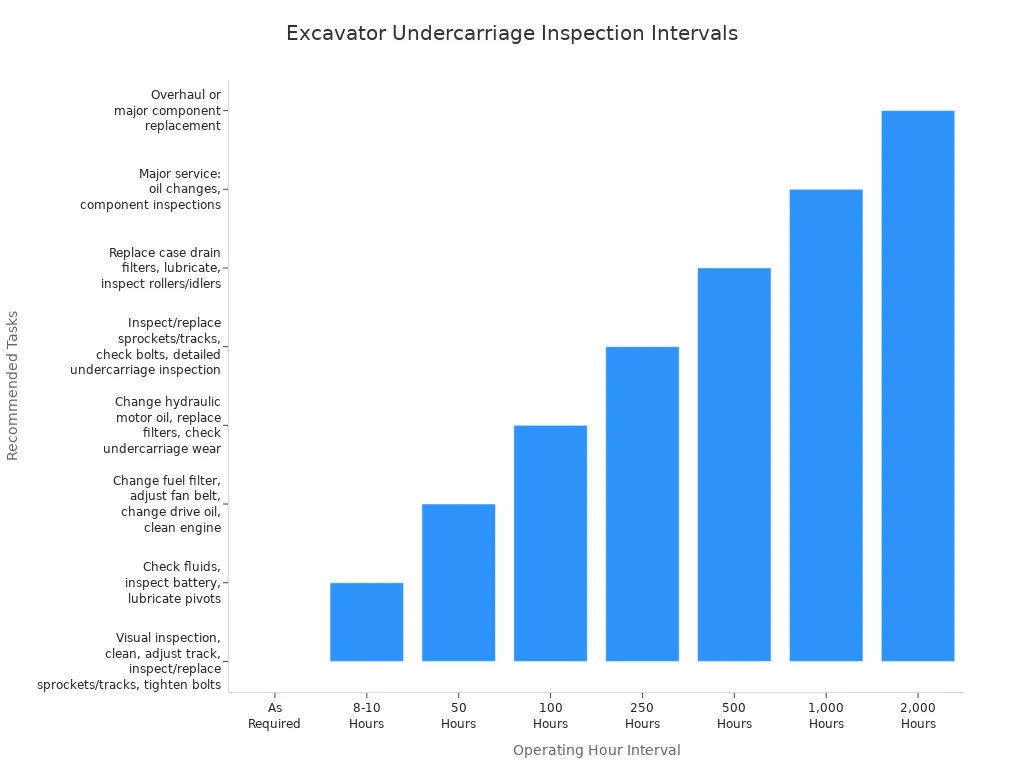
Tip: Regular checks can make your excavator last up to 30% longer and save you money.
Cleaning & Lubrication
Clean your excavator’s undercarriage after each use. Use hand tools to get rid of big mud chunks. Spray the undercarriage with a pressure washer to remove dirt from rollers, idlers, and tracks. Do not use harsh chemicals that can hurt rubber parts. After cleaning, dry the undercarriage with air or clean rags to stop rust.
Put grease on all moving parts, especially rollers, idlers, and track links. Grease bushings every day when the machine is warm. Only use lubricants the manufacturer recommends. Check for leaks around rollers and idlers. Greasing lowers friction, stops rust, and helps your excavator last longer.
Note: Cleaning and greasing often can make tracks last up to 25% longer and cut emergency repairs by 40%.
When to Replace
You need to know when to change undercarriage parts. Watch for these signs:
Loose tracks that sag or make noise
Sprockets with worn or broken teeth
Idlers that are not lined up, making tracks run crooked
Rollers that are worn out, vibrate, or make the ride rough
Undercarriage Part | Key Indicators for Replacement | Consequences if Ignored |
---|---|---|
Track Pads | Too much wear, damage | Less grip, poor work |
Track Chain | Broken or stretched | Machine stops, uneven wear |
Rollers | Damage, stuck | More friction, risk of derailment |
Sprockets | Worn teeth, slipping | Less grip, uneven wear |
Idlers | Not lined up, uneven wear | Tracks run crooked, more wear |
If you see these problems, change the parts right away. Waiting can cause bigger repairs and more downtime. Good care keeps your excavator safe and working well.
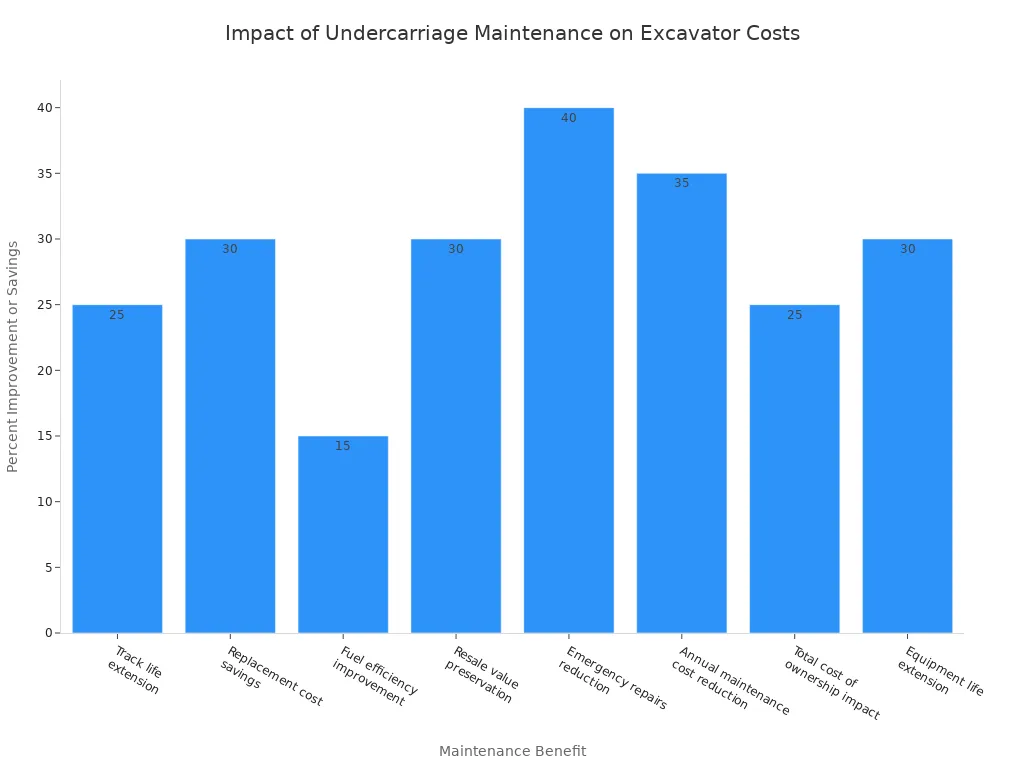
Knowing what each excavator undercarriage part does helps you a lot. If you understand how your excavator works, you can find problems early. This helps you save money and avoid big repairs. Checking and caring for your machine often is important.
Good undercarriage care helps your excavator stay strong and steady.
Cleaning and greasing every day or week makes your excavator last longer.
Fixing small problems early stops bigger issues and keeps your machine safe.
If you take care of your excavator, it will work well for a long time.
FAQ
What is the most important part of an excavator undercarriage?
You should pay close attention to the track chains. These parts support the weight and movement of your excavator. If you keep them in good shape, your machine will run smoothly and last longer.
How often should you inspect your excavator undercarriage?
You should check your excavator undercarriage every day. Look for loose bolts, worn tracks, and damaged rollers. Regular inspections help you find problems early and prevent bigger repairs.
Can you use an excavator on rocky ground?
Yes, you can use an excavator on rocky ground. You should choose wear-resistant track chains and rock guards. These parts protect your machine and help it work better in tough conditions.
What happens if you ignore undercarriage maintenance?
If you skip maintenance, your excavator may break down. Worn parts can cause the tracks to slip or come off. You might face expensive repairs and lose valuable work time.