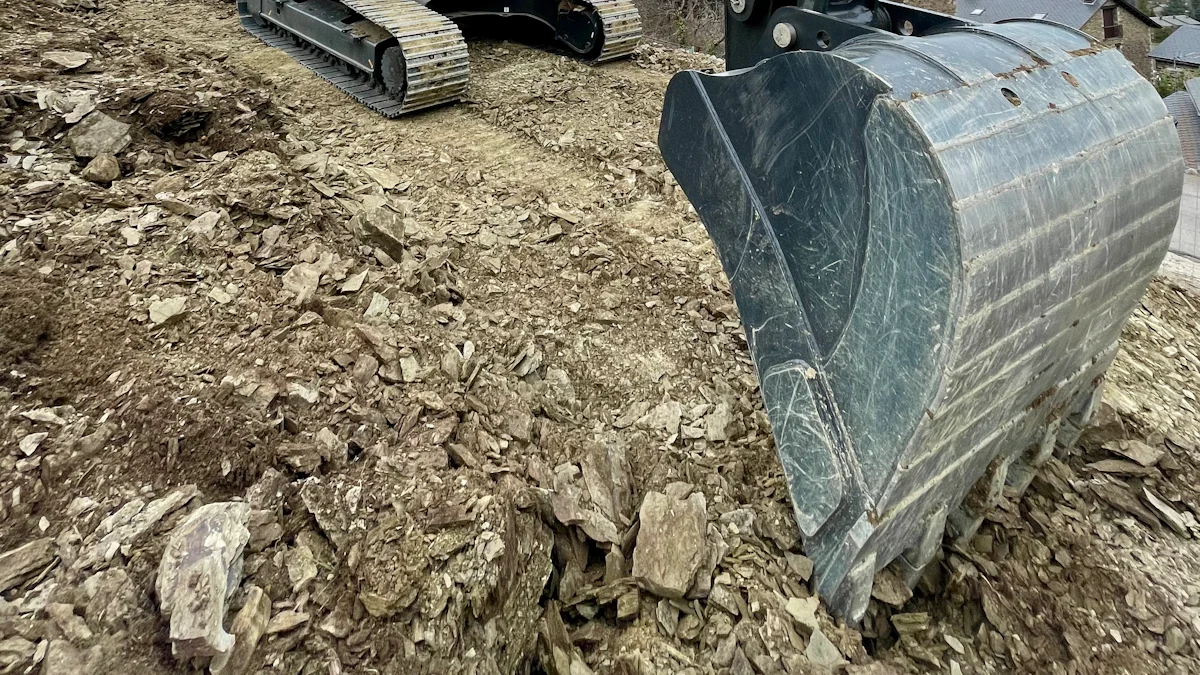
Excavator drills are specialized attachments designed to transform excavators into powerful drilling machines. These tools play a vital role in industries like construction and mining, where precision and efficiency are essential. By attaching an excavator drill, you can tackle tasks such as rock drilling, soil excavation, and foundation preparation with ease. Their adaptability allows them to perform in challenging environments, making them indispensable for modern projects. Whether you’re working on a construction site or extracting minerals, these attachments enhance productivity and ensure accurate results.
Key Takeaways
Excavator drills transform standard excavators into powerful drilling machines, enhancing their capabilities for tasks like rock drilling and foundation preparation.
These drills are designed for precision and efficiency, making them essential for construction and mining projects that require accurate results.
Different types of excavator drills, such as hydraulic, auger, and rock drills, cater to various materials and project needs, ensuring versatility in application.
Using excavator drills significantly speeds up the drilling process, reducing labor costs and minimizing the risk of injuries associated with manual methods.
Regular maintenance is crucial for extending the lifespan of excavator drills, ensuring reliable performance and preventing costly repairs.
Excavator drills excel in diverse environments, making them suitable for both urban construction sites and remote mining locations.
Choosing the right excavator drill involves considering the type of project, material, and ensuring compatibility with your existing excavator equipment.
Understanding Excavator Drills
What Are Excavator Drills?
Definition and basic functionality
An excavator drill is a specialized attachment that transforms your excavator into a powerful drilling machine. These attachments are designed to handle a variety of tasks, including rock drilling, soil excavation, and foundation preparation. By replacing the standard bucket with a drill attachment, you can expand the capabilities of your excavator to meet the demands of construction and mining projects.
The primary function of an excavator drill is to create precise holes in tough materials like rock, concrete, or soil. This precision makes it an essential tool for projects requiring accuracy, such as installing utility lines or preparing blast holes in mining operations. With its robust design, an excavator drill can operate efficiently in challenging environments, ensuring reliable performance even in extreme conditions.
How they integrate with excavators
Excavator drills integrate seamlessly with excavators through a straightforward attachment process. Most models are designed to be interchangeable with the excavator’s bucket, allowing you to switch between digging and drilling tasks quickly. This adaptability ensures that you can maximize the use of your equipment without needing additional machinery.
Modern excavator drills often use hydraulic systems to power their drilling mechanisms. These systems connect directly to the excavator’s hydraulic lines, providing the necessary force to penetrate hard surfaces. The boom of the excavator enhances the drill’s reach, enabling you to access difficult-to-reach areas, such as steep slopes or confined spaces. This combination of flexibility and power makes excavator drills a versatile solution for various construction and mining applications.
Key Features of Excavator Drills
Design and build quality
The design and build quality of an excavator drill play a crucial role in its performance. High-quality drills are constructed with durable materials that can withstand the wear and tear of demanding tasks. For example, many models feature reinforced steel components to ensure longevity and reliability. A well-designed drill also incorporates advanced engineering to optimize efficiency and reduce operational downtime.
Some excavator drills, like the HY-W series, are specifically engineered to handle tough conditions. These models are ideal for projects such as road construction, slope stabilization, and quarrying. Their robust construction ensures consistent performance, even in environments where traditional drilling rigs might fail.
Compatibility with different excavator models
Excavator drills are designed to be compatible with a wide range of excavator models. This compatibility allows you to choose a drill that matches the specifications of your existing equipment. Many manufacturers offer versatile attachments that can be modified to fit different excavator sizes and brands. This flexibility ensures that you can find a drill suitable for your specific needs without investing in new machinery.
For instance, some excavator-mounted rock drills, like those from Pro Drill, excel in both construction and mining applications. These attachments not only fit various excavators but also provide exceptional performance in challenging conditions. Their ability to adapt to different job sites makes them a valuable addition to any project requiring drilling capabilities.
Types of Excavator Drills
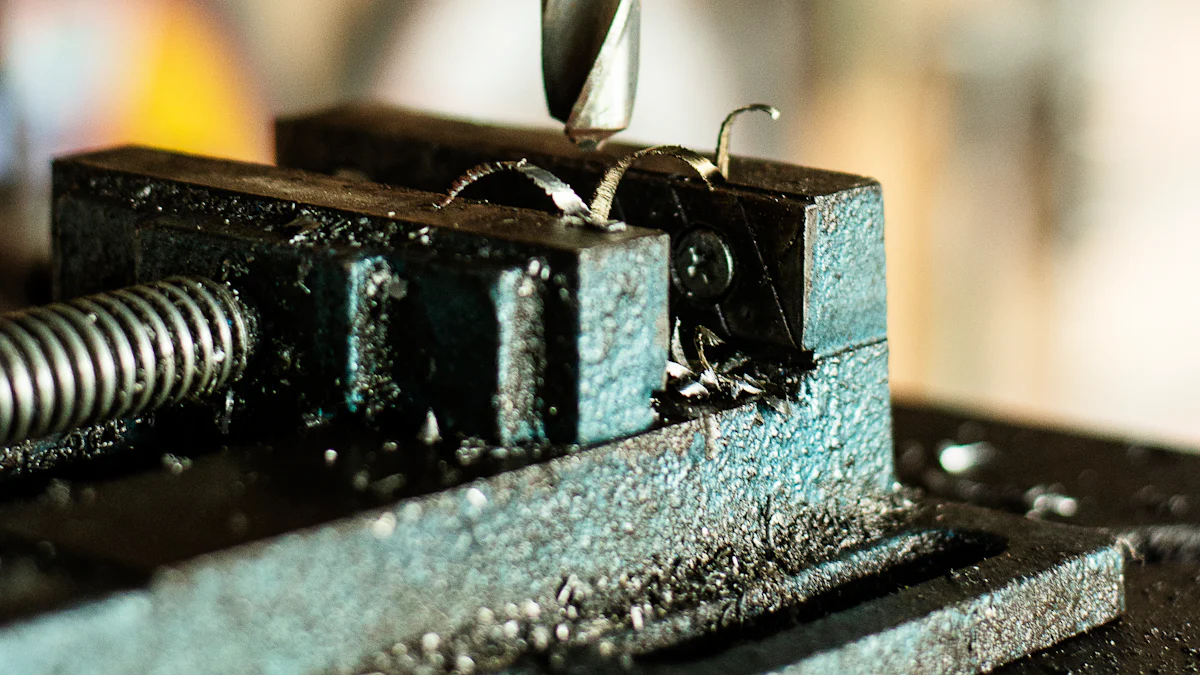
Hydraulic Drills
Features and advantages
Hydraulic drills rely on the power of hydraulic systems to deliver exceptional drilling performance. These drills use the excavator’s hydraulic lines to generate the force needed to penetrate tough materials like rock, concrete, and compacted soil. Their design ensures consistent power output, making them ideal for demanding tasks.
One key advantage of hydraulic drills is their efficiency. They operate with minimal energy loss, allowing you to complete projects faster. Their robust construction ensures durability, even in harsh environments. Additionally, hydraulic drills offer precise control, enabling you to achieve accurate results in tasks such as foundation drilling or utility installation.
Common use cases
Hydraulic drills excel in applications that require strength and precision. You can use them for creating blast holes in mining operations or drilling into hard rock for construction projects. They are also effective in road construction, where they help establish stable foundations. Their versatility makes them a popular choice for projects involving dense or challenging materials.
Auger Drills
Features and advantages
Auger drills are designed for tasks that involve drilling into softer materials like soil, clay, or sand. These drills feature a helical screw blade, or auger, which efficiently removes material as it drills. This design minimizes resistance and ensures smooth operation.
The primary advantage of auger drills lies in their simplicity and speed. They are lightweight and easy to attach to your excavator, making them a convenient option for quick jobs. Auger drills also produce clean, uniform holes, which is essential for tasks like planting trees or installing fence posts. Their ability to handle loose or soft materials makes them a valuable tool for landscaping and agricultural projects.
Common use cases
You can use auger drills for a variety of tasks, particularly in landscaping and soil-related projects. They are perfect for digging holes for tree planting, fence installation, or light foundation work. Auger drills are also commonly used in utility projects, such as installing poles or anchors in soft ground. Their efficiency and ease of use make them a go-to option for projects requiring shallow or medium-depth drilling.
Rock Drills
Features and advantages
Rock drills are engineered to tackle the toughest materials, including solid rock and concrete. These drills use high-impact mechanisms to break through hard surfaces, making them indispensable for heavy-duty applications. Their rugged design ensures they can withstand the extreme forces required for rock drilling.
The main advantage of rock drills is their ability to handle high-pressure tasks with precision. They are built to create clean, accurate holes, even in the hardest materials. Rock drills also offer excellent durability, ensuring reliable performance over time. Their specialized design makes them suitable for projects where other types of drills might struggle.
Common use cases
Rock drills are widely used in mining and quarrying operations. You can use them to create holes for explosives or extract stone and minerals. In construction, rock drills are essential for tasks like drilling into bedrock for structural support or creating openings in concrete structures. Their ability to handle extreme conditions makes them a critical tool for challenging projects.
Excavator-Mounted Core Drills
Features and advantages
Excavator-mounted core drills are specialized attachments designed to extract cylindrical samples, or cores, from materials like rock, concrete, and soil. These tools provide unmatched precision, making them essential for projects that require detailed material analysis or structural assessments. By attaching a core drill to your excavator, you can transform it into a powerful machine capable of handling demanding drilling tasks.
One of the standout features of core drills is their ability to create clean, uniform holes. This precision ensures minimal disruption to surrounding materials, which is crucial for tasks like geological sampling or structural testing. Core drills also excel in durability. Their robust construction allows them to withstand the intense pressure and friction generated during drilling. Many models incorporate advanced cooling systems to prevent overheating, ensuring consistent performance over extended periods.
Another advantage lies in their adaptability. Core drills can integrate seamlessly with various excavator models, allowing you to use your existing equipment efficiently. Hydraulic-powered core drills, in particular, deliver exceptional force and control, enabling you to tackle tough materials with ease. This combination of precision, durability, and adaptability makes excavator-mounted core drills an invaluable tool for specialized drilling applications.
Common use cases
You can use excavator-mounted core drills in a wide range of industries and applications. In construction, they are ideal for extracting core samples to assess the strength and composition of materials before building begins. This ensures that foundations and structures are built on reliable ground. Core drills also play a vital role in mining, where they help identify mineral deposits by extracting samples from deep within the earth.
In addition to construction and mining, these drills are frequently used in environmental studies. For example, you can use them to collect soil samples for contamination analysis or geological research. Their ability to create precise, clean cores makes them indispensable for projects requiring detailed material evaluation.
Core drills are also valuable in infrastructure maintenance. You can use them to inspect the integrity of existing structures, such as bridges or tunnels, by extracting samples for laboratory testing. This helps identify potential weaknesses and ensures long-term safety. Whether you are working on a new project or maintaining an existing one, excavator-mounted core drills provide the accuracy and reliability needed for critical tasks.
Applications of Excavator Drills in Construction
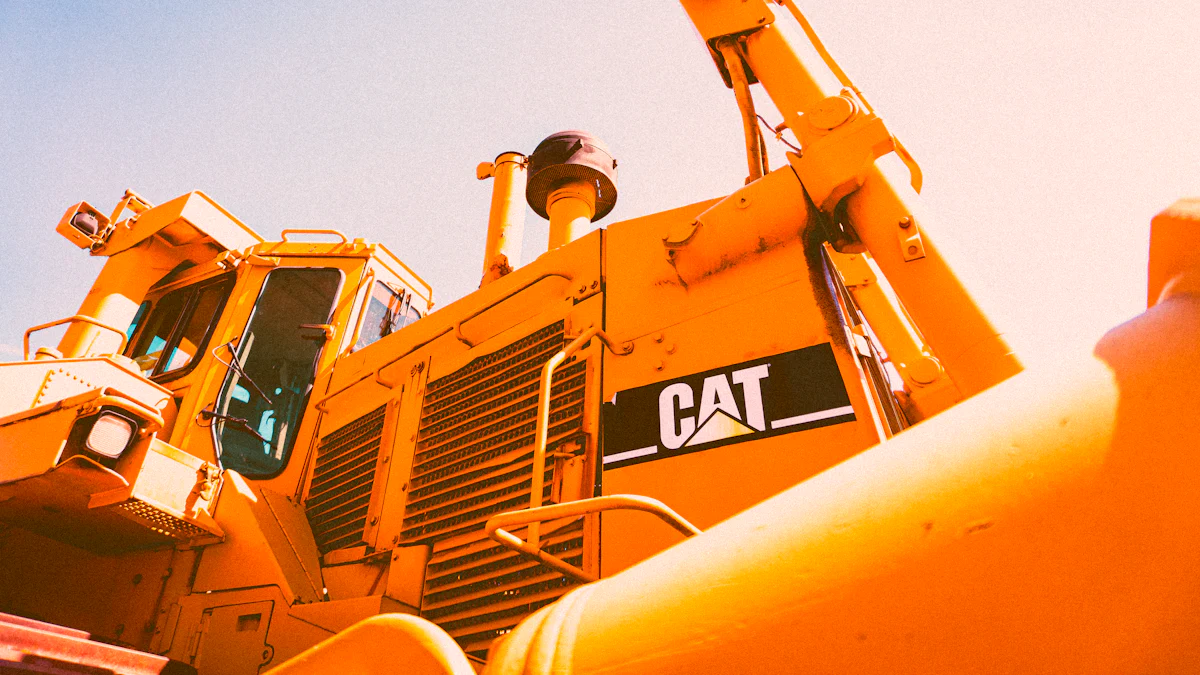
Foundation Drilling
Creating stable foundations for buildings
Creating a stable foundation is critical for any construction project. Excavator drills play a key role in this process by delivering precision and efficiency. When you use an excavator drill, you can create deep, uniform holes that provide the necessary support for building foundations. These drills excel in handling tough materials like rock and compacted soil, ensuring the stability of the structure above.
For example, hydraulic drills are particularly effective in foundation drilling. They utilize the excavator’s hydraulic system to generate the power needed to penetrate hard surfaces. Their robust design ensures consistent performance, even in challenging conditions. By using these tools, you can achieve accurate results while reducing the time and labor required for manual drilling.
Examples of projects
Excavator drills are commonly used in projects such as high-rise buildings, bridges, and industrial facilities. For instance, when constructing skyscrapers, you need to drill deep into the ground to create a solid base that can support the immense weight of the structure. Similarly, in bridge construction, these drills help establish stable piers that anchor the bridge securely.
In residential construction, auger drills are often employed to create shallow foundations for homes or small commercial buildings. Their ability to handle softer materials like soil and clay makes them ideal for these tasks. Whether you’re working on a large-scale infrastructure project or a smaller residential build, excavator drills provide the reliability and precision needed for foundation work.
Utility Installation
Drilling for pipelines and cables
Utility installation requires precise drilling to lay pipelines and cables underground. Excavator drills simplify this process by creating clean, accurate holes that minimize disruption to the surrounding area. Whether you’re installing water lines, electrical cables, or gas pipelines, these tools ensure efficient and reliable results.
Auger drills are particularly well-suited for utility installation. Their helical blade design efficiently removes soil, allowing you to drill quickly and effectively. This makes them an excellent choice for projects involving soft or loose materials. By using an auger drill, you can complete utility installations with minimal effort and maximum accuracy.
Examples of tasks
Excavator drills are widely used in tasks such as laying fiber optic cables, installing sewer lines, and setting up underground power grids. For example, when installing a water pipeline, you need to drill precise holes to ensure proper alignment and avoid damage to existing infrastructure. Similarly, in telecommunications projects, these drills help create pathways for cables without disrupting the surrounding environment.
In rural areas, excavator-mounted core drills are often used to extract soil samples before utility installation begins. This helps assess the ground conditions and ensures the project proceeds smoothly. By incorporating these tools into your utility installation projects, you can achieve efficient and accurate results.
Road and Bridge Construction
Drilling for structural support
Road and bridge construction often involves drilling to create structural supports. Excavator drills are essential for this task, as they provide the power and precision needed to penetrate tough materials like rock and concrete. By using these tools, you can ensure the stability and durability of the structures you build.
Rock drills are particularly effective in road and bridge construction. Their high-impact mechanisms allow them to break through hard surfaces with ease, making them ideal for creating support columns or anchoring bridge piers. These drills also offer excellent durability, ensuring reliable performance throughout the project.
Examples of use cases
In road construction, excavator drills are used to create holes for guardrail posts, signposts, and lighting fixtures. For example, when building a highway, you need to drill into the ground to install barriers that enhance safety. Similarly, in bridge construction, these drills help establish deep foundations that anchor the structure securely.
Quarrying operations often support road and bridge projects by providing the necessary materials. Excavator-mounted rock drills are frequently used in these operations to extract stone and aggregate. By integrating these tools into your construction projects, you can achieve precise and efficient results, ensuring the long-term success of your work.
Applications of Excavator Drills in Mining
Mineral Extraction
Drilling for ore and minerals
Excavator drills play a crucial role in extracting valuable minerals from the earth. By attaching a drill to your excavator, you can efficiently penetrate underground layers to access ore deposits. These drills are designed to handle tough materials, making them ideal for mining operations that require precision and durability. Hydraulic-powered drills, in particular, deliver the force needed to break through dense rock formations, ensuring effective mineral extraction.
Using an excavator drill allows you to streamline the mining process. The hydraulic system of the excavator powers the drill, enabling it to operate with consistent performance. This setup reduces the time and effort required to reach mineral-rich zones. Whether you’re working on a large-scale mining project or a smaller operation, these tools enhance productivity and ensure accurate results.
Examples of mining operations
Excavator drills are widely used in various mining scenarios. For instance, in open-pit mining, you can use these drills to create access points for extracting ore. In underground mining, they help establish tunnels and shafts by drilling through rock layers. Quarrying operations also rely on excavator drills to extract raw materials like limestone and granite. These examples highlight the versatility of excavator drills in the mining industry.
Blasting Preparation
Creating blast holes for explosives
Blasting preparation is a critical step in mining, and excavator drills make this process more efficient. You can use these drills to create precise blast holes, which are essential for placing explosives. The accuracy of the drilling ensures that the blast is controlled, minimizing waste and maximizing the yield of valuable materials. Rock drills, known for their high-impact mechanisms, are particularly effective for this task.
The ability to drill clean and uniform holes is vital for successful blasting. Excavator drills achieve this by delivering consistent power and precision. This capability allows you to optimize the placement of explosives, ensuring that the surrounding rock breaks apart as intended. By using an excavator drill, you can improve the safety and efficiency of blasting operations.
Examples of tasks
Excavator drills are commonly used in tasks such as preparing blast holes for quarrying and mining. For example, in a quarry, you might need to drill multiple holes to place explosives for breaking large rock formations. In mining, these drills help create blast patterns that facilitate the extraction of minerals. Their reliability and precision make them indispensable for projects involving blasting.
Quarrying
Drilling for stone and aggregate extraction
Quarrying operations depend heavily on excavator drills for extracting stone and aggregates. These materials are essential for construction projects, and the ability to drill efficiently ensures a steady supply. Excavator-mounted rock drills excel in this application, as they can penetrate hard surfaces like granite and basalt with ease. Their robust design ensures consistent performance, even in demanding environments.
By using an excavator drill, you can simplify the process of extracting stone and aggregates. The drill’s hydraulic system provides the power needed to break through tough materials, while its precision ensures minimal waste. This combination of efficiency and accuracy makes excavator drills a valuable tool for quarrying.
Examples of use cases
Excavator drills are used in various quarrying scenarios. For instance, you can use them to extract limestone for cement production or granite for building materials. They are also effective for producing aggregates used in road construction. These use cases demonstrate the importance of excavator drills in meeting the demands of the construction and mining industries.
Benefits of Using Excavator Drills
Efficiency and Productivity
Faster drilling compared to manual methods
Using an excavator drill significantly speeds up the drilling process compared to traditional manual methods. In earlier times, miners relied on manual drilling, which required immense physical effort and consumed a lot of time. Today, with advancements in technology, excavator drills deliver faster results by utilizing hydraulic systems and powerful mechanisms. These tools can penetrate tough materials like rock and compacted soil in a fraction of the time it would take manually. This efficiency allows you to complete projects on schedule, even when working in demanding environments.
Reduced labor costs
Excavator drills reduce the need for extensive manual labor. By attaching a drill to your excavator, you can perform tasks that would otherwise require a team of workers. This not only lowers labor costs but also minimizes the risk of injuries associated with manual drilling. For example, large excavators, often used in mining projects, can handle heavy-duty drilling tasks independently, eliminating the need for additional equipment or manpower. This cost-effectiveness makes excavator drills an essential investment for both small and large-scale operations.
Precision and Accuracy
Improved drilling accuracy for specific tasks
Excavator drills provide unmatched precision, ensuring that every hole is drilled exactly where it is needed. This accuracy is crucial for tasks like foundation preparation, utility installation, and blasting in mining operations. The hydraulic systems in these drills allow you to control the drilling process with precision, even in challenging conditions. Whether you are working on a construction site or extracting minerals, the ability to drill with pinpoint accuracy ensures the success of your project.
Reduced material waste
Accurate drilling reduces material waste, saving both time and resources. When you use an excavator drill, you can create clean, uniform holes without damaging the surrounding material. This is especially important in projects like quarrying, where preserving the integrity of extracted stone or aggregate is essential. By minimizing waste, you can maximize the efficiency of your operations and reduce overall project costs.
Versatility and Adaptability
Ability to handle various drilling tasks
Excavator drills are versatile tools capable of handling a wide range of drilling tasks. From creating blast holes in mining to installing utility lines in construction, these attachments adapt to different requirements with ease. For instance, auger drills excel in soft materials like soil, while rock drills are designed for hard surfaces such as granite or concrete. This adaptability allows you to use a single excavator for multiple applications, enhancing the overall functionality of your equipment.
Compatibility with different environments
Excavator drills perform reliably in diverse environments, from urban construction sites to remote mining locations. Their robust design ensures consistent performance, even in extreme conditions. Surface excavators, often used in surface mining, demonstrate the importance of this adaptability. By equipping your excavator with the right drill attachment, you can tackle projects in any setting, whether it involves steep slopes, confined spaces, or rocky terrains.
Choosing the Right Excavator Drill
Factors to Consider
Type of project and material
Selecting the right excavator drill begins with understanding your project requirements. Different projects demand specific drilling capabilities, and the material you are working with plays a significant role in this decision. For instance, if your project involves drilling into soft soil, an auger drill with its helical blade design is ideal. It efficiently extracts soil through rotational force, ensuring clean and precise results. On the other hand, for hard surfaces like rock or concrete, a hydraulic or rock drill provides the power and durability needed to penetrate tough materials.
Matching the drill type to the material ensures optimal performance and reduces wear and tear on your equipment. For construction projects requiring foundation work or utility installations, choosing a drill designed for precision and efficiency will save time and resources. Always evaluate the material’s density and the depth of drilling required before making your selection.
Excavator compatibility
Compatibility between the excavator and the drill attachment is crucial for seamless operation. Not all drills fit every excavator model, so you must ensure that the attachment matches your equipment’s specifications. Many manufacturers design versatile drills that can adapt to various excavator sizes and brands, offering flexibility for different projects.
Hydraulic-powered drills, for example, connect directly to the excavator’s hydraulic system, enabling efficient power transfer. This integration enhances the drill’s performance and ensures consistent results. Additionally, the excavator’s boom provides extended reach, allowing you to access challenging areas. By choosing a compatible drill, you maximize the functionality of your excavator and avoid unnecessary downtime caused by mismatched equipment.
Maintenance and Longevity
Importance of regular maintenance
Regular maintenance is essential to keep your excavator drill in top condition. Drilling tasks often expose the equipment to harsh conditions, including high pressure, friction, and debris. Without proper care, these factors can lead to reduced performance and costly repairs. Routine inspections help identify potential issues early, preventing unexpected breakdowns during critical projects.
Cleaning the drill after each use removes dirt and debris that could damage its components. Lubricating moving parts ensures smooth operation and minimizes wear. Hydraulic systems, in particular, require regular checks to maintain optimal pressure levels. By prioritizing maintenance, you extend the lifespan of your drill and ensure reliable performance across multiple projects.
Tips for extending drill lifespan
To maximize the longevity of your excavator drill, follow these practical tips:
Inspect components regularly: Check for signs of wear, such as cracks or loose bolts, and address them promptly.
Use the right drill for the job: Avoid overloading the drill by using it on materials it is not designed to handle.
Store equipment properly: Keep the drill in a dry, secure location to protect it from environmental damage.
Follow manufacturer guidelines: Adhere to the recommended maintenance schedule and use approved replacement parts.
Monitor hydraulic systems: Ensure the hydraulic lines are free from leaks and maintain the correct pressure levels.
By implementing these practices, you not only extend the life of your excavator drill but also enhance its efficiency and reliability. Proper care ensures that your equipment remains a valuable asset for years to come.
Excavator drills have revolutionized construction and mining by offering unmatched efficiency, precision, and adaptability. You can choose from various types, such as hydraulic, auger, rock, or core drills, to meet specific project needs. These tools excel in tasks like foundation drilling, utility installation, and mineral extraction, ensuring reliable performance in demanding environments. By integrating an excavator drill, like the versatile HY-W series, into your equipment, you enhance productivity and reduce operational challenges. Consider these attachments as essential tools to elevate the success of your modern projects.