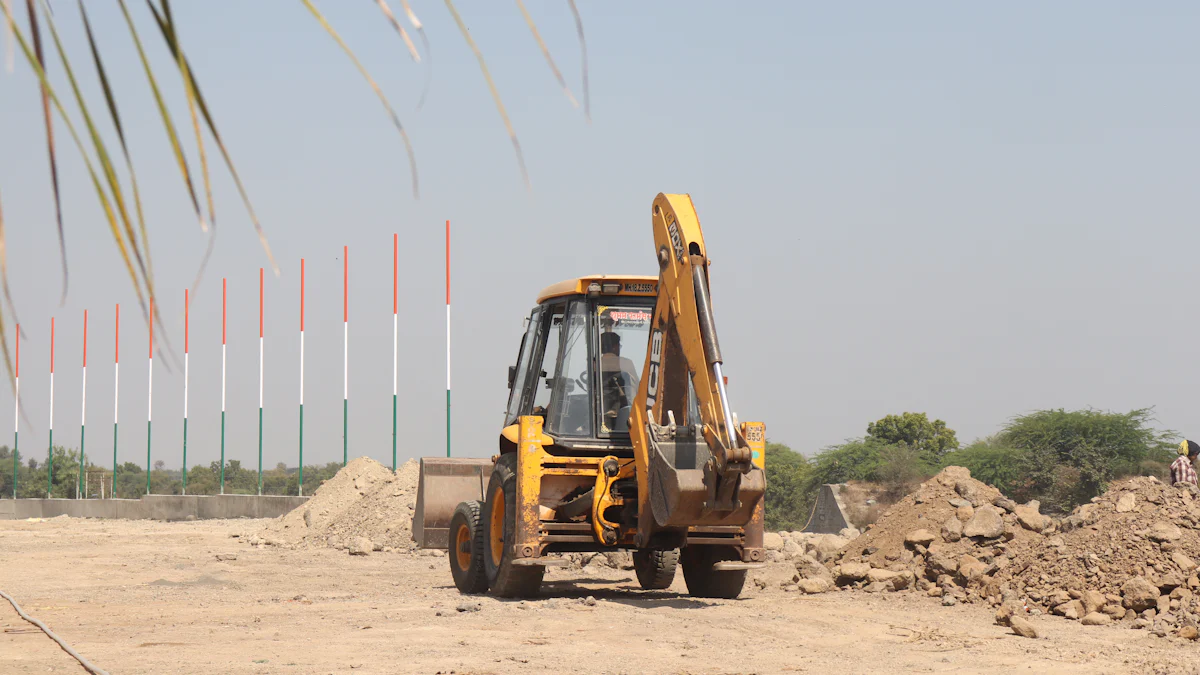
Selecting the right hydraulic rock drill for mini excavator ensures efficient and reliable performance. These tools are essential for tasks like drilling through tough rock and concrete, where precision and power matter most. Models such as the PD-90, Sandvik HF820T, and Furukawa hydraulic breaker stand out for their exceptional compatibility and durability. Their advanced designs deliver high impact energy while maintaining efficiency. You should also consider factors like hydraulic flow requirements and build quality to maximize productivity and minimize downtime during operations.
Key Takeaways
Choose a hydraulic rock drill that matches your project’s specific needs, considering factors like impact energy and drilling speed for optimal performance.
Ensure compatibility with your mini excavator by checking hydraulic flow and pressure requirements to avoid inefficiencies or equipment damage.
Prioritize durability by selecting drills made from high-quality materials that can withstand heavy-duty use, reducing the need for frequent repairs.
Look for user-friendly features such as quick-connect systems and clear labeling to simplify operation and maintenance, enhancing overall efficiency.
Evaluate the long-term value of a drill by considering maintenance costs and the availability of replacement parts to minimize downtime.
Assess the weight and size of the drill to ensure it complements your mini excavator’s capacity, maintaining balance and stability during operation.
Research brand reputation and customer support options, as a strong warranty and accessible service can protect your investment and ensure reliable performance.
Key Features to Look for in a Hydraulic Rock Drill for Mini Excavator
When selecting a hydraulic rock drill for mini excavator, understanding the essential features ensures you make an informed decision. These features directly impact performance, compatibility, and longevity.
Power and Performance
Impact energy and drilling speed
The power of a hydraulic rock drill determines its ability to penetrate tough materials like rock and concrete. High impact energy translates to faster and more efficient drilling. For instance, models like the HYG550 outperform others by delivering 13.5% higher energy efficiency. This improvement enhances drilling speed and reduces operational time. A powerful drill ensures consistent performance, even in demanding conditions.
Suitability for different rock types and applications
Not all rock drills perform equally across various applications. Some excel in breaking hard rock, while others are better suited for softer materials. You should evaluate the type of projects you handle most frequently. For example, if you work on grouting or anchor bolt holes, a versatile drill with adjustable settings will serve you better. Matching the drill’s capabilities to your specific needs ensures optimal results.
Compatibility with Mini Excavators
Hydraulic flow and pressure requirements
Hydraulic rock drills rely on the excavator’s hydraulic system for power. Ensuring compatibility with your mini excavator’s hydraulic flow and pressure is critical. A mismatch can lead to inefficiency or even damage to the equipment. Always check the manufacturer’s specifications to confirm the drill aligns with your excavator’s hydraulic output.
Weight and size considerations
The weight and size of the drill must complement your mini excavator’s capacity. An oversized attachment can strain the machine, reducing its lifespan. Lightweight models, like the Sandvik HF820T, offer excellent performance without compromising the excavator’s balance. Proper sizing ensures smooth operation and minimizes wear on your equipment.
Durability and Build Quality
Materials used in construction
The materials used in a hydraulic rock drill significantly affect its durability. High-quality steel and reinforced components withstand the rigors of heavy-duty drilling. Investing in a drill with robust construction reduces the risk of frequent repairs and replacements.
Resistance to wear and tear
Frequent use exposes hydraulic rock drills to wear and tear. Models like the HYG550 are designed to extend the service life of drill pipes, making them a cost-effective choice. Look for features like wear-resistant coatings or replaceable parts to ensure long-term reliability.
Maintenance and Ease of Use
Service intervals and part availability
Regular maintenance keeps your hydraulic rock drill for mini excavator running efficiently. You should always follow the recommended service intervals provided by the manufacturer. These intervals ensure that critical components, such as seals and hydraulic lines, remain in optimal condition. Neglecting maintenance can lead to reduced performance or costly repairs.
When choosing a drill, consider the availability of replacement parts. Models like the HYG550 stand out because they offer extended service life for components like drill pipes. This reduces the frequency of part replacements, saving you time and money. Manufacturers with a strong distribution network make it easier to source parts quickly, minimizing downtime during operations.
User-friendly design features
A user-friendly design simplifies operation and maintenance. Look for features like quick-connect systems, which make attaching and detaching the drill hassle-free. Lightweight models, such as the Sandvik HF820T, are easier to handle and reduce strain on your mini excavator. These designs improve efficiency and reduce operator fatigue.
Clear labeling and accessible maintenance points also enhance usability. For instance, some drills include visual indicators for hydraulic pressure, helping you monitor performance in real time. Tools with intuitive controls allow operators to adjust settings quickly, ensuring precision and adaptability across different tasks. Prioritizing ease of use ensures smoother operations and better results.
Detailed Reviews of the Top Hydraulic Rock Drills for Mini Excavators
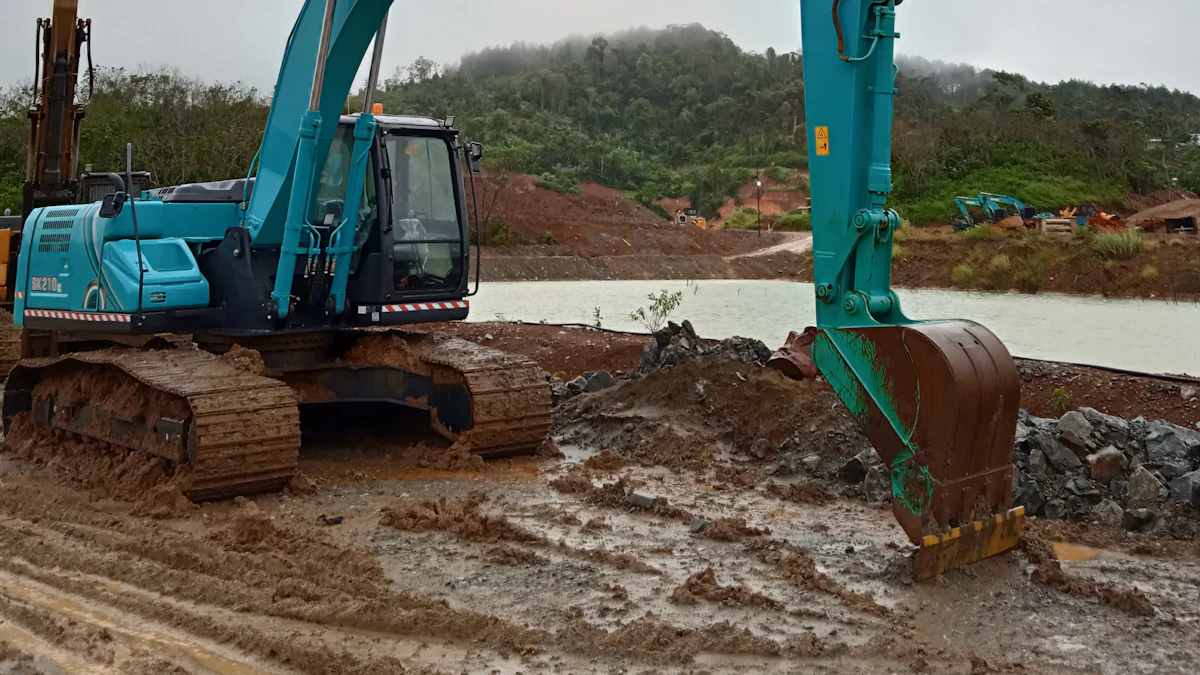
PD-90 Excavator Mounted Rock Drill
Key specifications
The PD-90 Excavator Mounted Rock Drill is a high-performance tool designed for demanding drilling tasks. It delivers an impressive percussion hour-to-engine hour ratio of 60%, ensuring efficient energy use. This model supports a wide range of drilling diameters, making it versatile for various applications. Its compact design allows seamless integration with mini excavators, enhancing operational flexibility.
Pros and cons
Pros:
High energy efficiency reduces fuel consumption.
Compact size ensures compatibility with most mini excavators.
Durable construction minimizes wear and tear during heavy-duty use.
Cons:
Limited availability of replacement parts in some regions.
Requires precise hydraulic flow calibration for optimal performance.
Ideal use cases
The PD-90 excels in tasks like drilling blast holes, anchor bolt holes, and grouting holes. Its efficiency makes it ideal for projects requiring consistent performance over extended periods. If you frequently work on hard rock or concrete, this model offers reliable results.
Sandvik HF820T Hydraulic Rock Drill
Key specifications
The Sandvik HF820T Hydraulic Rock Drill stands out for its precision and adaptability. It supports drilling diameters ranging from 64 to 127 mm, making it suitable for diverse applications. Its lightweight design ensures compatibility with mini excavators without compromising balance. Advanced hydraulic systems enhance its performance, delivering consistent impact energy.
Pros and cons
Pros:
Wide drilling diameter range increases versatility.
Lightweight design reduces strain on mini excavators.
Advanced hydraulic systems improve drilling precision.
Cons:
Higher initial cost compared to similar models.
Requires regular maintenance to sustain peak performance.
Ideal use cases
This model is perfect for projects demanding precision, such as creating anchor bolt holes or drilling in confined spaces. Its lightweight design makes it a great choice for operators prioritizing ease of use and equipment longevity.
Furukawa Hydraulic Breaker
Key specifications
The Furukawa Hydraulic Breaker is renowned for its robust performance and user-friendly features. It integrates advanced systems that simplify maintenance and enhance reliability. This breaker is specifically designed for mini excavators, ensuring seamless compatibility. Its durable build withstands the rigors of breaking hard rock and concrete.
Pros and cons
Pros:
High reliability ensures consistent performance.
User-friendly features simplify operation and maintenance.
Durable construction extends service life.
Cons:
Limited drilling diameter range compared to other models.
Slightly heavier than some competing options.
Ideal use cases
The Furukawa Hydraulic Breaker is ideal for breaking concrete and hard rock in construction or demolition projects. Its reliability and ease of use make it a preferred choice for operators seeking minimal downtime and straightforward maintenance.
Kymron Excavator Hydraulic Drill Attachment
Key specifications
The Kymron Excavator Hydraulic Drill Attachment is a versatile tool designed to enhance the functionality of mini excavators. It features a robust hydraulic system that ensures consistent performance across various drilling applications. This attachment supports a range of drilling diameters, making it suitable for tasks like anchor bolt installation, grouting, and rock breaking. Its compact design allows seamless integration with mini excavators, ensuring smooth operation without compromising balance or stability.
Key highlights include:
Hydraulic compatibility: Designed to match the hydraulic flow and pressure requirements of most mini excavators.
Durable construction: Built with high-grade steel to withstand wear and tear during heavy-duty operations.
Lightweight design: Reduces strain on the excavator while maintaining excellent drilling efficiency.
Maintenance-friendly features: Equipped with easily accessible components for quick servicing and part replacement.
Pros and cons
Pros:
Exceptional versatility for a wide range of drilling tasks.
Lightweight design minimizes stress on your mini excavator.
Durable materials ensure long-term reliability and reduced maintenance costs.
User-friendly features simplify operation and maintenance.
Cons:
Limited availability in certain regions may delay procurement.
Requires precise hydraulic calibration for optimal performance.
Ideal use cases
The Kymron Excavator Hydraulic Drill Attachment excels in projects requiring precision and adaptability. It is ideal for creating anchor bolt holes, drilling in confined spaces, and breaking softer rock formations. Its lightweight design makes it a preferred choice for operators who prioritize ease of use and equipment longevity. If you frequently handle diverse drilling tasks, this attachment offers the flexibility and reliability you need to maximize productivity.
Comparison Table of the Top Hydraulic Rock Drills for Mini Excavators
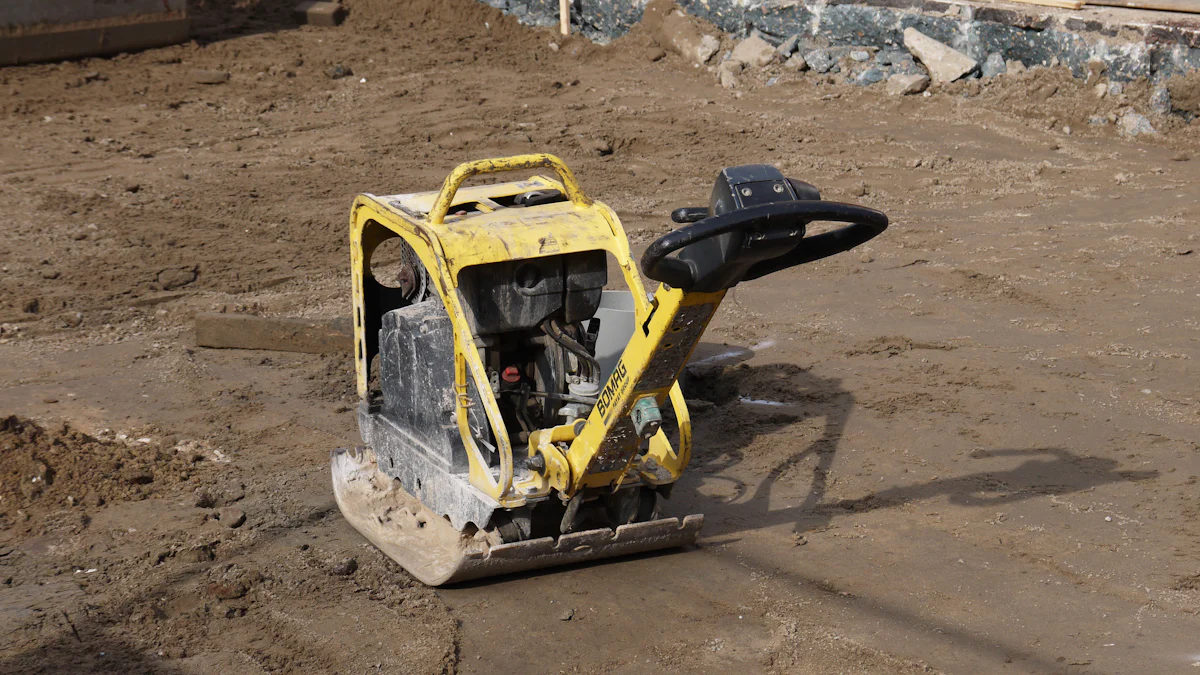
When comparing hydraulic rock drills, understanding their specifications and value helps you make an informed decision. Below is a detailed breakdown of the key features and pricing considerations for the top models.
Key Specifications
Power and performance metrics
The power and performance of a hydraulic rock drill determine its efficiency in handling tough materials. For instance, the PD-90 Excavator Mounted Rock Drill offers a percussion hour-to-engine hour ratio of 60%, ensuring high energy efficiency. Similarly, the Sandvik HF820T Hydraulic Rock Drill delivers consistent impact energy, making it ideal for precision tasks. Models like the Furukawa HD Series Rock Drills incorporate advanced piston designs to maximize energy transmission, ensuring effective drilling across various rock types. These metrics highlight the importance of selecting a drill that matches your project’s demands.
Compatibility details
Compatibility ensures seamless integration with your mini excavator. The Kymron Excavator Hydraulic Drill Attachment stands out for its lightweight design, reducing strain on your equipment while maintaining balance. The Furukawa Hydraulic Breaker is specifically designed for mini excavators, ensuring proper hydraulic flow and pressure alignment. Additionally, models like the Doofor DF560L-BLTG-2M are crafted for diverse tasks, offering flexibility in construction projects. Always verify the hydraulic flow and pressure requirements to avoid inefficiencies or equipment damage.
Durability and maintenance factors
Durability plays a crucial role in minimizing downtime and repair costs. The Furukawa FRD Rock Drills feature robust construction with wear-resistant materials, ensuring long-term reliability. Similarly, the HYG550 extends the service life of drill pipes, reducing the frequency of replacements. Maintenance-friendly designs, such as those found in the Doofor DF538L-BLTG, simplify servicing and part replacement. Prioritizing durability and ease of maintenance ensures your drill remains operational under demanding conditions.
Pricing and Value
Cost comparison
Pricing varies significantly among hydraulic rock drills, reflecting differences in features and performance. The Sandvik HF820T Hydraulic Rock Drill commands a higher initial cost due to its advanced hydraulic systems and precision capabilities. In contrast, the Furukawa Hydraulic Breaker offers a more budget-friendly option without compromising reliability. The Kymron Excavator Hydraulic Drill Attachment provides excellent value with its versatile design and durable construction. Comparing costs alongside features helps you identify the best option within your budget.
Features offered at different price points
Higher-priced models often include advanced features that enhance performance and usability. For example, the PD-90 Excavator Mounted Rock Drill combines high energy efficiency with a compact design, justifying its premium price. Mid-range options like the Furukawa HD Series Rock Drills balance affordability with innovative designs, such as noise and vibration reduction. Budget-friendly models, such as the Doofor DF560L-BLTG-2M, focus on essential features while maintaining reliability. Evaluating the features offered at various price points ensures you get the best value for your investment.
By comparing these specifications and pricing details, you can select the hydraulic rock drill for mini excavator that aligns with your operational needs and budget.
Buying Guide for Hydraulic Rock Drills for Mini Excavators
Assessing Your Needs
Type of projects and materials
Understanding the type of projects you handle helps you choose the right hydraulic rock drill for mini excavator. If your work involves breaking through hard rock or concrete, prioritize models with high impact energy and robust construction. For tasks like grouting or anchor bolt installation, select a drill with precision and adjustable settings. Matching the drill’s capabilities to the materials you work with ensures efficient performance and reduces wear on the equipment.
Frequency of use
The frequency of use plays a significant role in your decision. For daily operations, invest in a durable and high-performance model that can withstand continuous use. Occasional users may benefit from budget-friendly options with basic features. Consider the long-term demands of your projects to avoid overpaying for features you may not need or underinvesting in a tool that cannot handle your workload.
Budget Considerations
Balancing cost and performance
Balancing cost and performance ensures you get the best value for your investment. High-end models often come with advanced features like enhanced hydraulic systems or wear-resistant materials. While these may have a higher upfront cost, they deliver superior performance and reliability. On the other hand, mid-range options can offer a good balance of affordability and essential features. Evaluate your budget and prioritize features that directly impact your productivity.
Long-term value and maintenance costs
Long-term value goes beyond the initial purchase price. Consider the maintenance costs and availability of replacement parts. A model with a higher upfront cost but lower maintenance requirements may save you money over time. Look for drills with durable construction and extended service intervals. Reliable brands often provide better customer support and easier access to spare parts, reducing downtime and ensuring consistent performance.
Compatibility with Your Mini Excavator
Checking hydraulic system requirements
Before purchasing, verify the hydraulic system requirements of the drill. Ensure the hydraulic flow and pressure specifications align with your mini excavator’s capabilities. A mismatch can lead to inefficiency or damage to both the drill and the excavator. Refer to the manufacturer’s guidelines to confirm compatibility. Proper alignment guarantees optimal performance and prevents unnecessary wear on your equipment.
Ensuring proper fit and balance
The drill’s weight and size must match your mini excavator’s capacity. An oversized attachment can strain the machine, affecting its stability and lifespan. Lightweight models, designed specifically for mini excavators, maintain balance and ensure smooth operation. Always check the attachment points and dimensions to confirm a secure fit. A well-matched drill enhances safety and efficiency during use.
Evaluating Brand Reputation and Support
Warranty and Customer Service
When choosing a hydraulic rock drill for your mini excavator, the warranty and customer service offered by the manufacturer play a critical role. A strong warranty reflects the brand’s confidence in its product. It also provides you with peace of mind, knowing that potential defects or issues will be addressed without additional costs. Look for brands that offer comprehensive warranties covering key components like hydraulic systems and wear parts.
Customer service quality is equally important. Reliable brands provide responsive support to address your concerns quickly. You should prioritize manufacturers with dedicated customer service teams that can assist with troubleshooting, technical questions, or warranty claims. Brands with 24/7 support or online resources, such as manuals and video tutorials, enhance your experience and reduce downtime during operations.
“A dependable warranty and excellent customer service ensure that your investment remains protected and operational for years to come.”
Availability of Replacement Parts
The availability of replacement parts significantly impacts the long-term usability of your hydraulic rock drill. Frequent use leads to wear and tear, making it essential to replace components like seals, drill bits, and hydraulic lines. You should choose a brand with a well-established distribution network to ensure quick access to these parts. Delays in sourcing replacements can halt your projects and increase operational costs.
Some manufacturers maintain an inventory of parts that are readily available through authorized dealers or online platforms. This accessibility reduces downtime and keeps your equipment running efficiently. Additionally, consider brands that offer interchangeable parts across multiple models. This feature simplifies maintenance and lowers costs by reducing the need for unique components.
“Choosing a brand with readily available replacement parts ensures uninterrupted operations and minimizes costly delays.”
The PD-90, Sandvik HF820T, Furukawa hydraulic breaker, and Kymron attachment represent the top choices for a hydraulic rock drill for mini excavator. Each model excels in key areas like power, compatibility, and durability. For heavy-duty drilling, the PD-90 offers unmatched efficiency. The Sandvik HF820T stands out for precision and adaptability. If you need reliability for breaking hard materials, the Furukawa hydraulic breaker is ideal. For versatility and ease of use, the Kymron attachment delivers excellent value. Evaluate your project needs and ensure compatibility with your mini excavator to make the best investment.