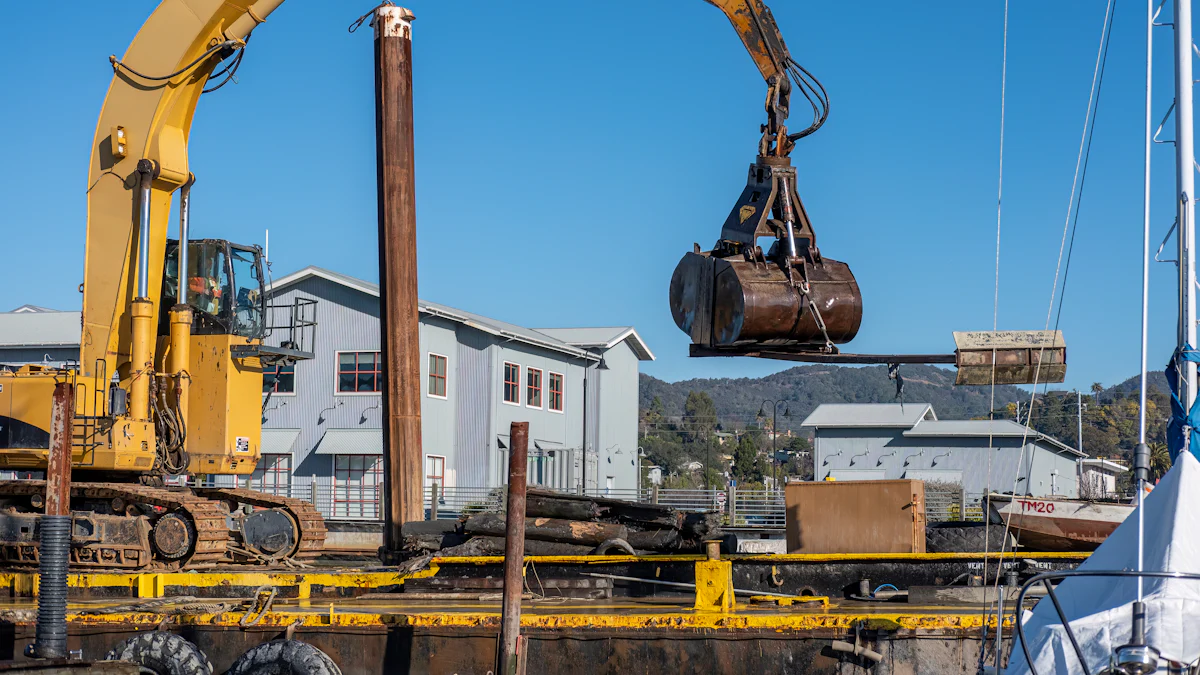
Choosing high-quality excavator parts is essential for ensuring your machine operates efficiently and safely. Reliable components reduce downtime, enhance performance, and save costs in the long run. Regular maintenance and timely replacement of worn parts prevent extensive damage to other components. For example, hydraulic systems rely heavily on durable parts to maintain optimal performance. YNF Machinery offers dependable excavator main parts designed to meet diverse needs. With over 35 years of expertise, YNF Machinery ensures you receive parts that deliver reliability and longevity, keeping your operations running smoothly.
Key Takeaways
Investing in high-quality excavator parts enhances performance and reduces downtime, ultimately saving costs in the long run.
Regular maintenance and timely replacement of components like filters and sprockets are crucial for preventing extensive damage and ensuring operational efficiency.
Understanding the specific roles of undercarriage components, such as tracks and rollers, helps in making informed purchasing decisions.
Prioritize the maintenance of hydraulic system parts, including pumps and cylinders, to ensure smooth operation and extend the lifespan of your excavator.
Utilizing maintenance kits simplifies upkeep by providing all necessary components for routine servicing, ensuring compatibility and saving time.
Safety features like backup cameras and warning alarms are essential for enhancing operator safety and preventing accidents during excavator operations.
Selecting the right attachments, such as buckets and grapples, maximizes your excavator’s versatility and productivity across various tasks.
Undercarriage Components: Essential Excavator Components for Stability
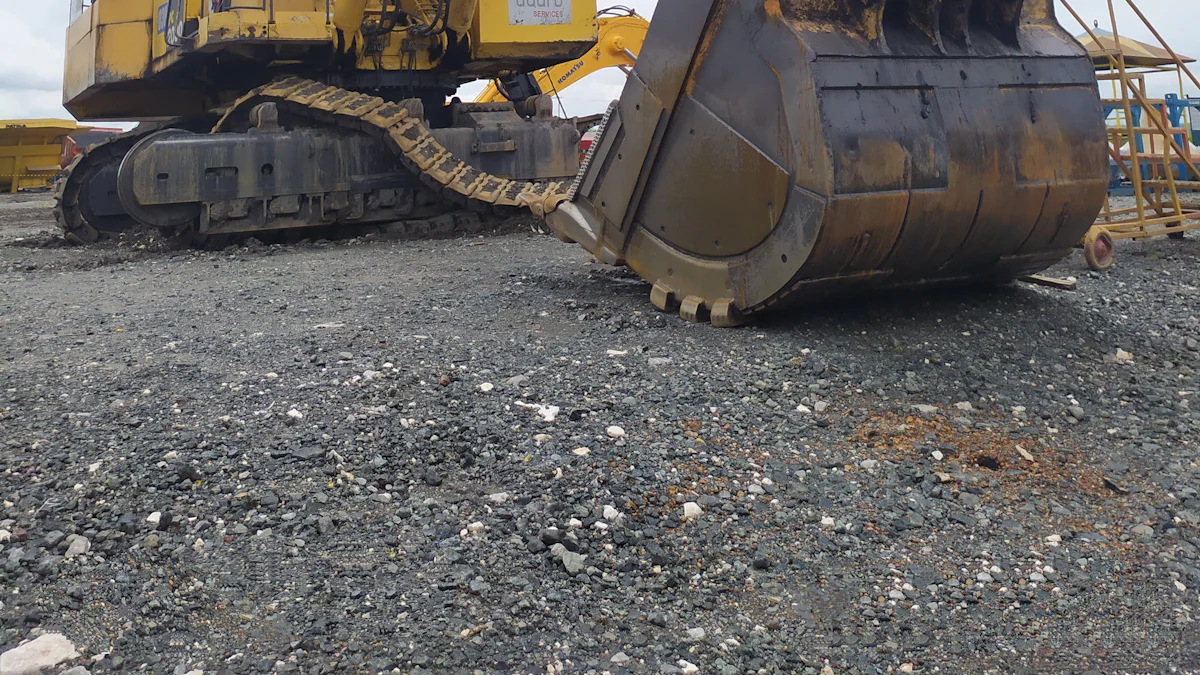
The undercarriage serves as the foundation of your excavator, ensuring proper support and movement across various terrains. It plays a critical role in maintaining the machine’s stability, especially during heavy-duty operations. Understanding the key parts of the undercarriage helps you make informed decisions when purchasing or replacing components.
Tracks
Tracks are vital for providing traction and mobility. They allow your excavator to navigate challenging surfaces like mud, gravel, or uneven ground. Choosing the right type of tracks ensures optimal performance and durability.
Rubber Tracks
Rubber tracks are ideal for projects requiring minimal ground disturbance. They offer excellent grip on soft surfaces like grass or dirt, making them suitable for landscaping or urban construction. Their lightweight design reduces wear on the undercarriage and enhances fuel efficiency. Regular inspections help you identify signs of wear, such as cracks or tears, ensuring timely replacements.
Steel Tracks
Steel tracks are designed for heavy-duty applications. They excel in rugged environments like mining or demolition sites, where durability is paramount. These tracks provide superior strength and resistance to sharp objects, ensuring long-lasting performance. Proper maintenance, including cleaning and lubrication, extends their lifespan and prevents premature damage.
Rollers and Idlers
Rollers and idlers support the tracks and distribute the machine’s weight evenly. They reduce friction and ensure smooth movement, which is essential for maintaining the undercarriage and traction.
Bottom Rollers
Bottom rollers bear the brunt of the excavator’s weight. They keep the tracks aligned and prevent derailment during operation. High-quality rollers crafted from durable steel alloys withstand heavy loads and harsh conditions. Regular cleaning and lubrication prevent debris buildup and extend their operational life.
Top Rollers
Top rollers, also known as carrier rollers, guide the tracks and maintain proper tension. They play a crucial role in reducing wear on the tracks and other undercarriage components. Precision-engineered rollers with advanced seals offer enhanced reliability and longevity. Inspecting these rollers periodically ensures consistent performance.
Sprockets: Commonly Replaced Excavator Parts
Sprockets engage with the tracks to convert engine power into movement. They are among the most frequently replaced parts due to constant contact with the tracks. Worn sprockets can lead to uneven track wear and reduced efficiency. Investing in high-quality sprockets ensures smooth operation and minimizes downtime. Regular inspections and timely replacements prevent costly repairs and maintain the excavator’s performance.
“Periodic maintenance, repairs, and adjustments, including inspections, are imperative to avoid wear and enhance the operational life of the working parts.”
By focusing on these essential excavator components, you can ensure the longevity and efficiency of your machine’s undercarriage. Proper care and timely replacements keep your excavator stable and ready for any task.
Track Chains
Track chains play a crucial role in connecting the tracks to the undercarriage, ensuring smooth and efficient movement of your excavator. These components bear the machine’s weight and endure constant stress during operation. Selecting high-quality track chains enhances durability and reduces the risk of unexpected breakdowns.
Key Features of Track Chains:
Durability: Track chains are designed to withstand heavy loads and challenging terrains. High-quality chains crafted from robust materials, such as forged steel, ensure long-lasting performance.
Flexibility: Properly engineered track chains allow smooth articulation, enabling your excavator to navigate uneven surfaces with ease.
Compatibility: Ensure the track chains you choose are compatible with your excavator model to maintain optimal performance.
Maintenance Tips for Track Chains:
Regular Inspections: Examine the track chains for signs of wear, such as elongation or cracks. Early detection prevents further damage and costly repairs.
Proper Tensioning: Maintain the correct tension to avoid excessive strain on the chains and other undercarriage components. Over-tightened chains can lead to premature wear, while loose chains may derail during operation.
Lubrication: Apply appropriate lubrication to reduce friction and minimize wear. This practice also helps in preventing rust and corrosion.
Cleaning: Remove debris, mud, and dirt from the chains after each use. Accumulated debris can accelerate wear and compromise the chain’s performance.
“Periodic maintenance, repairs, and adjustments, including inspections, are imperative to avoid wear and enhance the operational life of the working parts.”
Investing in high-quality track chains and adhering to a consistent maintenance routine ensures your excavator remains reliable and efficient. By prioritizing these essential components, you can extend the lifespan of your machine and optimize its performance across various terrains.
Hydraulic System Parts: Key Excavator Main Parts for Performance
The hydraulic system powers your excavator’s movements and ensures smooth operation.
Hydraulic Pumps
The hydraulic pump serves as the heart of the hydraulic system.
To keep the pump in optimal condition:
Monitor for unusual noises or vibrations, which may indicate wear.
Check for leaks around the pump housing.
Replace worn seals promptly to prevent fluid loss.
Regular inspections and timely replacements ensure the pump operates efficiently, minimizing downtime.
Hydraulic Cylinders
Hydraulic cylinders convert the energy from pressurized fluid into linear motion. They play a vital role in controlling the excavator’s boom, arm, and bucket. Each cylinder has a specific function, making it essential to understand their roles.
Boom Cylinder
The boom cylinder raises and lowers the excavator’s boom. It provides the power needed to lift heavy loads and reach high areas. A well-maintained boom cylinder ensures smooth and precise movements, enhancing productivity.
Arm Cylinder
The arm cylinder controls the movement of the excavator’s arm. It enables the machine to extend or retract the arm, allowing for accurate positioning during operations. Regular maintenance prevents leaks and ensures consistent performance.
Bucket Cylinder
The bucket cylinder operates the excavator’s bucket. It provides the force required to dig, scoop, or dump materials. Inspecting the bucket cylinder for signs of wear, such as scratches or dents, helps maintain its efficiency.
Hydraulic Hoses and Fittings
Hydraulic hoses and fittings connect the various components of the hydraulic system, allowing fluid to flow seamlessly. These parts endure high pressure and constant movement, making them prone to wear. High-quality hoses and fittings reduce the risk of leaks and ensure reliable performance.
To maintain these components:
Inspect hoses for cracks, bulges, or abrasions.
Check fittings for signs of corrosion or looseness.
Replace damaged hoses and fittings immediately to prevent system failure.
Proper care of hoses and fittings supports the overall efficiency of the hydraulic system and fluid maintenance.
“Investing in durable hydraulic components and seals ensures the longevity of your excavator’s hydraulic system.”
By prioritizing the maintenance of these hydraulic components, you can enhance your excavator’s performance and extend its lifespan. Regular inspections and timely replacements keep your machine running smoothly, reducing costly repairs and downtime.
Engine Components: Vital Excavator Parts for Longevity
The engine and power systems of your excavator are the backbone of its performance. Maintaining these vital engine components ensures your machine operates efficiently and lasts longer.
Filters
Filters play a crucial role in protecting your excavator’s engine by keeping contaminants out. Regularly replacing filters ensures clean airflow, oil, and fuel, which are essential for optimal engine performance.
Air Filters
Air filters prevent dust, dirt, and debris from entering the engine. A clogged air filter can reduce engine efficiency and increase fuel consumption. Inspect your air filter frequently, especially in dusty environments. Replace it when you notice reduced airflow or visible dirt buildup. High-quality air filters improve engine longevity and maintain consistent performance.
Oil Filters
Oil filters remove impurities from the engine oil, ensuring smooth lubrication of moving parts. Dirty or clogged oil filters can lead to increased friction and wear. Replace oil filters during every oil change to maintain engine health. Using reliable oil filters minimizes the risk of engine damage and extends the life of your excavator.
Fuel Filters
Fuel filters block contaminants from reaching the engine through the fuel system. Clean fuel filters ensure efficient combustion and prevent engine misfires. Replace fuel filters regularly to avoid clogs that can disrupt fuel flow. High-quality fuel filters enhance engine reliability and reduce maintenance costs.
Turbochargers
Turbochargers boost engine power by forcing more air into the combustion chamber. This process improves fuel efficiency and increases the machine’s overall performance. Over time, turbochargers may wear out due to high temperatures and pressure. Inspect them for signs of damage, such as unusual noises or reduced power output. Replacing worn turbochargers ensures your excavator maintains its productivity and efficiency.
Cooling Systems
Cooling systems regulate engine temperature, preventing overheating during operation. Proper maintenance of these components is essential for avoiding engine damage and ensuring smooth performance.
Radiators
Radiators dissipate heat from the engine coolant, keeping the engine at an optimal temperature. Dirt and debris can clog radiators, reducing their efficiency. Clean the radiator fins regularly and check for leaks. Replace damaged radiators promptly to maintain effective cooling.
Cooling Fans
Cooling fans enhance airflow through the radiator, improving heat dissipation. Worn or damaged fans can lead to inadequate cooling and engine overheating. Inspect the fan blades for cracks or wear and ensure they rotate smoothly. Replacing faulty cooling fans helps maintain a stable engine temperature and prevents costly repairs.
“Regular maintenance of crucial engine parts, including filters, turbochargers, and cooling systems, ensures your excavator operates at peak efficiency.”
By prioritizing the care of these vital engine parts, you can extend the lifespan of your excavator and optimize its performance. High-quality components and consistent maintenance keep your machine reliable and ready for demanding tasks.
Attachments and Work Tools: Enhancing Excavator Versatility
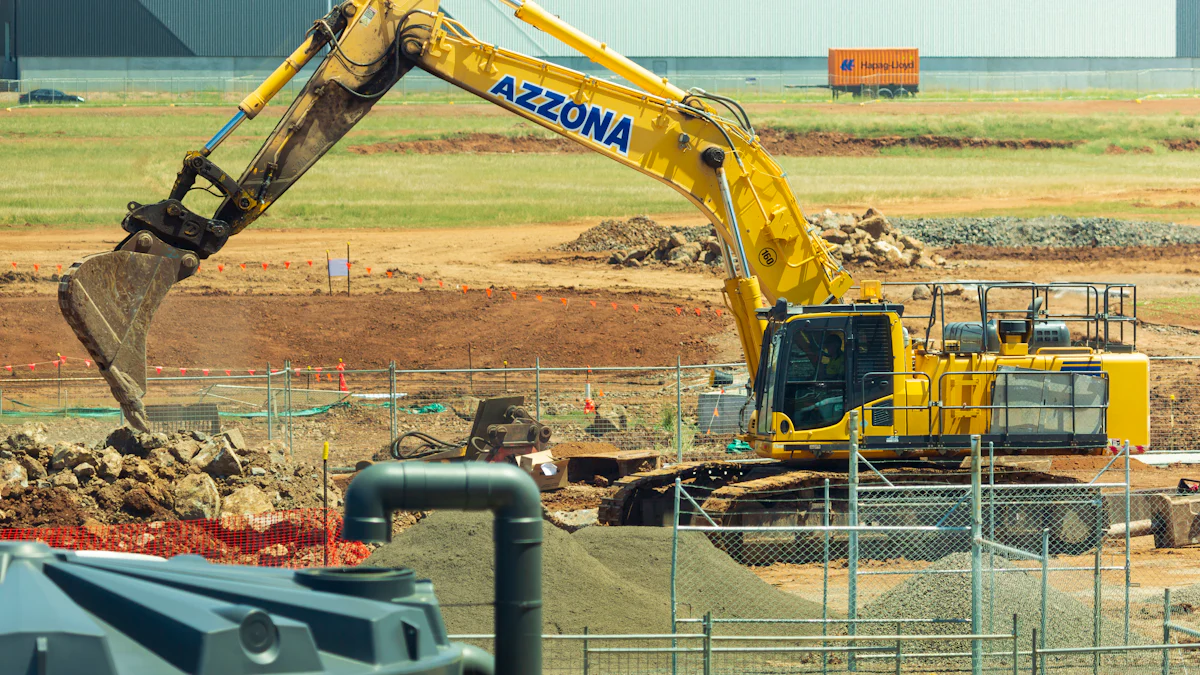
Attachments and work tools significantly enhance the versatility of your excavator attachments. They allow you to adapt your machine to various tasks, improving efficiency and productivity.
Buckets
Buckets are among the most commonly used excavator attachments. They handle tasks like digging, scooping, and material handling. Choosing the appropriate bucket type for your project ensures better results and minimizes operational strain.
General-Purpose Buckets
General-purpose buckets are versatile and suitable for a wide range of applications. They excel in tasks like digging, loading, and moving materials such as soil, sand, or gravel. These buckets feature a balanced design that provides durability and efficiency. Regular cleaning and inspection of the bucket edges prevent wear and maintain their effectiveness.
Heavy-Duty Buckets
Heavy-duty buckets are designed for demanding tasks in tough environments. They handle materials like rocks, clay, and demolition debris with ease. Reinforced edges and robust construction make them resistant to wear and impact. Inspecting the bucket teeth and adapters regularly ensures consistent performance and reduces downtime.
Quick Couplers
Quick couplers simplify the process of switching between attachments. They save time and increase productivity by allowing you to change tools without manual intervention. High-quality quick couplers ensure secure attachment and prevent accidental detachment during operation. Regular maintenance, including lubrication and inspection of locking mechanisms, keeps them functioning reliably.
Hydraulic Hammers
Hydraulic hammers are essential for breaking through tough materials like concrete, asphalt, or rock. They deliver powerful blows, making them ideal for demolition and excavation projects. Properly maintaining hydraulic hammers ensures consistent performance and extends their lifespan. Key maintenance practices include checking for leaks, inspecting seals, and replacing worn-out parts promptly.
“Attachments like buckets, quick couplers, and hydraulic hammers transform your excavator into a multi-functional machine, enabling you to tackle diverse tasks efficiently.”
Investing in high-quality attachments and maintaining them regularly ensures your excavator remains versatile and reliable. By selecting the right tools for your projects, you can maximize productivity and reduce wear on your machine.
Grapples
Grapples are indispensable attachments for excavators, designed to handle materials with precision and efficiency. They excel in tasks such as sorting, loading, and moving bulky or irregularly shaped objects. Whether you work in construction, forestry, or waste management, grapples enhance your excavator’s versatility and productivity.
Key Features of Grapples:
Versatility: Grapples can handle a wide range of materials, including logs, scrap metal, rocks, and debris.
Durability: High-quality grapples are built from robust materials to withstand heavy loads and harsh conditions.
Precision: Their design allows for accurate gripping and placement, reducing material damage and improving operational efficiency.
Types of Grapples:
Sorting Grapples: Ideal for separating and organizing materials. These grapples are commonly used in recycling and demolition projects.
Log Grapples: Specifically designed for forestry applications, they provide a secure grip on logs for easy transport and stacking.
Demolition Grapples: Built for heavy-duty tasks, these grapples handle large debris and demolition waste effectively.
Maintenance Tips for Grapples:
Regular Cleaning: Remove dirt, mud, and debris after each use to prevent wear and maintain functionality.
Lubrication: Apply grease to pivot points and moving parts to reduce friction and extend the grapple’s lifespan.
Inspection: Check for cracks, loose bolts, or hydraulic leaks. Addressing these issues promptly ensures reliable performance.
Hydraulic System Care: Keep the hydraulic hoses and fittings in good condition to avoid fluid contamination, which can lead to system failures.
“Strengthening regular maintenance ensures that grapples remain in optimal working condition, reducing downtime and operating costs.”
Investing in high-quality grapples tailored to your specific needs boosts your excavator’s efficiency. By maintaining these attachments properly, you can maximize their lifespan and ensure consistent performance across various applications.
Electrical Components: Ensuring Reliable Excavator Operation
Electrical components play a vital role in maintaining the smooth operation of your excavator.
Batteries
Batteries provide the initial power needed to start your excavator and support its electrical systems. A reliable battery ensures consistent performance, especially in demanding environments. Over time, batteries can lose their charge capacity due to wear or exposure to extreme temperatures.
Key Tips for Battery Maintenance:
Inspect Regularly: Check for corrosion on terminals and clean them to maintain a strong connection.
Test Voltage: Use a multimeter to measure the battery’s voltage. Replace it if the charge drops below the recommended level.
Secure Placement: Ensure the battery is firmly secured to prevent vibrations that may damage internal components.
Charge Properly: Avoid overcharging or deep discharging, as these can shorten the battery’s lifespan.
Investing in high-quality batteries designed for heavy-duty machinery ensures reliable operation and consistent power delivery.
Alternators
Alternators generate electricity to recharge the battery and power the excavator’s electrical systems during operation. A malfunctioning alternator can lead to insufficient power supply, causing system failures or battery drain.
Signs of a Faulty Alternator:
Dim or flickering lights
Slow or weak engine starts
Warning indicators on the control panel
Maintenance Tips for Alternators:
Inspect Belts: Check the drive belt for cracks or wear. Replace it if necessary to maintain proper tension and performance.
Clean Connections: Ensure all electrical connections are clean and secure to avoid power loss.
Monitor Output: Test the alternator’s output voltage regularly to ensure it meets the manufacturer’s specifications.
Replacing worn or damaged alternators promptly prevents disruptions and ensures your excavator operates efficiently. High-quality alternators designed for heavy machinery provide durability and reliable performance.
Wiring Harnesses
Wiring harnesses connect the various electrical components of your excavator, enabling seamless communication and power distribution. Damaged or faulty wiring can disrupt operations and pose safety risks.
Common Issues with Wiring Harnesses:
Frayed or exposed wires
Loose or corroded connectors
Electrical shorts or intermittent faults
Steps to Maintain Wiring Harnesses:
Inspect Routinely: Look for signs of wear, such as cracks, cuts, or exposed wires. Address issues immediately to prevent further damage.
Secure Properly: Ensure the harness is securely fastened to avoid rubbing against sharp edges or moving parts.
Protect from Moisture: Use protective sleeves or coatings to shield the wiring from water, dirt, and debris.
Check Connectors: Tighten loose connectors and replace corroded ones to maintain a stable electrical connection.
High-quality wiring harnesses designed for excavators withstand harsh conditions and provide reliable performance. Regular inspections and timely repairs ensure uninterrupted operation and enhance the longevity of your machine.
“Maintaining your excavator’s electrical components ensures reliable performance and reduces the risk of unexpected failures.”
By prioritizing the care of batteries, alternators, and wiring harnesses, you can keep your excavator’s electrical systems in top condition. Investing in durable components and following a consistent maintenance routine enhances efficiency and minimizes downtime, ensuring your machine is always ready for the job.
Safety and Operator Comfort Features: Prioritizing Safety and Efficiency
Safety and comfort are essential for ensuring efficient excavator operations. A well-designed cabin not only enhances operator safety but also improves productivity by reducing fatigue. Modern excavators incorporate advanced safety features of the cabin to provide maximum visibility and protection, ensuring operator safety and excavator stability during demanding tasks.
Cab Components
Operator Seats
The operator seat is a critical component of the cabin design and safety features. A high-quality seat provides ergonomic support, reducing strain during long hours of operation. Adjustable seats allow you to customize the position for optimal comfort and control. Look for seats with shock-absorbing mechanisms to minimize vibrations, which can improve stability and prevent tipping during heavy-duty tasks. Regularly inspect the seat for wear and tear to maintain its functionality and ensure operator safety.
Control Panels
Control panels serve as the command center of the excavator. A well-organized panel enhances efficiency by allowing you to access controls quickly and intuitively. Modern control panels often include digital displays that provide real-time data on machine performance, stability, and counterweights. These features help you make informed decisions during operations. Ensure the control panel is clean and free from obstructions to maintain smooth functionality. Familiarizing yourself with the layout and functions of the panel can further enhance safety and efficiency.
Safety Systems
Backup Cameras
Backup cameras are essential for improving visibility and preventing accidents. They provide a clear view of the area behind the excavator, reducing blind spots and enhancing operator awareness. This feature is particularly useful in crowded or confined workspaces. High-resolution cameras with wide-angle lenses offer maximum visibility and protection. Regularly check the camera system for any malfunctions or dirt buildup on the lens to ensure consistent performance.
Warning Alarms
Warning alarms play a vital role in alerting you to potential hazards. These alarms notify you of issues such as low stability, improper counterweights, or mechanical failures. Loud and distinct alarms ensure you can respond promptly to avoid accidents. Test the alarm system periodically to confirm it is functioning correctly. Reliable warning systems contribute significantly to operator safety and excavator stability, especially in high-risk environments.
“Investing in advanced safety systems and ergonomic cabin designs ensures a safer and more efficient working environment.”
By prioritizing safety features and maintaining cab components, you can enhance both operator comfort and machine performance. Regular inspections and timely upgrades keep your excavator ready for any challenge while ensuring the safety of the operator and the equipment.
Wear Parts: Commonly Replaced Excavator Parts for Maintenance
Regular inspection and timely replacement of these parts ensure your excavator operates efficiently and avoids costly downtime.
Cutting Edges
Cutting edges play a vital role in excavation tasks. They attach to the bottom of buckets and help cut through soil, rocks, or other materials. Over time, these edges wear down due to friction and impact. Replacing worn cutting edges improves digging efficiency and reduces strain on the bucket.
Key Benefits of High-Quality Cutting Edges:
Enhanced durability for extended use.
Improved cutting precision for smoother operations.
Reduced stress on the bucket and other components.
To maintain cutting edges effectively:
Inspect them regularly for signs of wear, such as thinning or cracks.
Replace damaged edges promptly to avoid further wear on the bucket.
Choose cutting edges made from hardened steel for better longevity.
“Timely replacement of cutting edges ensures your excavator performs optimally and minimizes operational delays.”
Teeth and Adapters
Bucket teeth and adapters are essential for breaking through hard surfaces. These parts experience significant wear due to their direct contact with abrasive materials. Worn teeth reduce digging efficiency and increase fuel consumption. Replacing them at the right time ensures your excavator maintains its productivity.
Features of Reliable Bucket Teeth and Adapters:
High resistance to abrasion and impact.
Easy installation and secure fit.
Compatibility with various bucket types.
Maintenance Tips for Teeth and Adapters:
Inspect teeth for chipping, dullness, or uneven wear.
Check adapters for cracks or looseness.
Replace worn teeth and adapters immediately to prevent damage to the bucket.
Investing in high-quality teeth and adapters reduces the frequency of replacements and enhances your excavator’s performance.
Side Cutters
Side cutters protect the sides of the bucket and improve its penetration ability. They handle lateral forces during digging, making them prone to wear. Replacing worn side cutters prevents damage to the bucket and ensures efficient material handling.
Advantages of Using Durable Side Cutters:
Increased bucket lifespan by reducing side wear.
Enhanced digging performance in tough conditions.
Better material retention during scooping.
Steps to Maintain Side Cutters:
Inspect side cutters for wear or deformation after each use.
Replace damaged cutters to maintain bucket integrity.
Use side cutters made from high-strength materials for better durability.
“Regular replacement of failing components like side cutters ensures your excavator remains reliable and efficient.”
By focusing on these commonly replaced excavator parts, you can extend the lifespan of your machine and reduce operational costs. Prioritizing wear parts and undercarriage replacements keeps your excavator ready for demanding tasks while minimizing downtime.
Lubrication and Maintenance Parts: Essential Excavator Components for Upkeep
Proper lubrication and maintenance are critical for keeping your excavator in peak condition.
Grease Fittings
Grease fittings, also known as grease nipples, play a vital role in maintaining your excavator’s moving parts. They provide access points for applying grease to components like pins, bushings, and bearings. Regular lubrication through these fittings minimizes friction and prevents premature wear.
Benefits of Using High-Quality Grease Fittings:
Ensure smooth movement of mechanical parts.
Protect components from rust and corrosion.
Reduce the risk of equipment failure.
Tips for Maintaining Grease Fittings:
Clean Before Use: Wipe the fittings clean before applying grease to prevent contaminants from entering the system.
Inspect Regularly: Check for damage or blockages that may hinder grease flow.
Use Compatible Grease Guns: Ensure the grease gun fits securely to avoid leaks during application.
“Regular maintenance of grease fittings ensures your excavator’s components remain well-lubricated and functional.”
By prioritizing the care of grease fittings, you can enhance the efficiency and reliability of your excavator’s moving parts.
Oil and Lubricants
Oil and lubricants are the lifeblood of your excavator. They reduce friction, dissipate heat, and protect components from wear. Using the right type of oil and lubricants ensures optimal performance and prevents damage to critical systems.
Key Types of Lubricants for Excavators:
Engine Oil: Keeps the engine running smoothly by reducing friction and removing contaminants.
Hydraulic Oil: Powers the hydraulic system, enabling precise and efficient movements.
Gear Oil: Protects gears and transmissions from wear and overheating.
Best Practices for Managing Oil and Lubricants:
Perform Regular Inspections: Check oil levels and quality frequently to ensure they meet the manufacturer’s specifications.
Replace on Schedule: Follow the recommended intervals for oil changes to maintain system efficiency.
Store Properly: Keep lubricants in a clean, dry place to prevent contamination.
“Investing in high-quality oil and lubricants reduces wear and extends the lifespan of your excavator’s critical systems.”
By adhering to a consistent lubrication routine, you can keep your excavator operating at its best.
Maintenance Kits
Maintenance kits simplify the upkeep of your excavator by providing all the necessary tools and parts in one package. These kits often include filters, seals, gaskets, and other essential components for routine servicing. Using a maintenance kit ensures you have everything needed for efficient repairs and replacements.
Advantages of Maintenance Kits:
Save time by eliminating the need to source individual parts.
Ensure compatibility with your excavator model.
Provide cost-effective solutions for regular maintenance.
How to Use Maintenance Kits Effectively:
Follow the Manual: Refer to the manufacturer’s guidelines for proper installation and usage.
Keep a Spare Kit: Stock an extra kit to handle unexpected repairs promptly.
Inspect Components: Check the kit’s contents for quality and completeness before use.
“Maintenance kits streamline the process of regular maintenance, helping you keep your excavator in top condition.”
By incorporating maintenance kits into your routine, you can simplify servicing tasks and minimize downtime.
Investing in high-quality excavator main parts is essential for maintaining optimal performance, safety, and longevity. Reliable components reduce downtime and enhance operational efficiency. Regular maintenance and timely replacement of commonly worn parts, such as filters and sprockets, ensure your excavator remains in peak condition. YNF Machinery stands out as a trusted supplier, offering durable excavator main parts that meet rigorous quality standards. Consult with YNF Machinery for expert recommendations tailored to your needs. By prioritizing quality and consistent upkeep, you can maximize the lifespan and productivity of your equipment.
FAQ
What are the most commonly replaced excavator parts?
The most commonly replaced parts include filters, sprockets, bucket teeth, and cutting edges. These components experience significant wear due to their constant use in demanding environments. Regular inspections and timely replacements of these parts help maintain your excavator’s efficiency and prevent costly downtime.
How often should I replace filters on my excavator?
You should replace filters, such as air filters, oil filters, and fuel filters, based on the manufacturer’s recommended intervals or when signs of clogging appear. For example, replace air filters if you notice reduced airflow or visible dirt buildup. Regular filter changes ensure clean airflow, proper lubrication, and efficient fuel combustion, which protect your engine from damage.
Why is proper lubrication important for excavators?
Lubrication reduces friction, minimizes wear, and protects moving parts from rust and contamination. Components like grease fittings ensure smooth operation by allowing grease to reach critical areas such as pins and bushings. Using high-quality lubricants also dissipates heat and removes debris, extending the lifespan of your excavator’s systems.
“Proper lubrication is essential to keep your excavator running smoothly and to avoid premature wear and tear.”
What are maintenance kits, and why should I use them?
Maintenance kits include essential items like filters, seals, gaskets, and lubricants for routine servicing. They simplify maintenance by providing all necessary components in one package. Using a maintenance kit ensures compatibility with your excavator model, saves time, and reduces the risk of missing critical parts during repairs.
How can I extend the lifespan of my excavator’s hydraulic system?
To extend the lifespan of your hydraulic system, focus on regular maintenance. Inspect hydraulic hoses and fittings for cracks or leaks, replace worn seals promptly, and use high-quality hydraulic oil. Keeping the system clean and well-lubricated prevents contamination and ensures efficient performance.
What should I look for when inspecting undercarriage components?
When inspecting undercarriage components, check tracks, rollers, sprockets, and track chains for signs of wear or damage. Look for cracks, elongation, or misalignment. Proper tensioning of tracks and regular cleaning of debris help maintain stability and prevent premature wear.
How do I choose the right bucket for my excavator?
Select a bucket based on your project requirements. General-purpose buckets work well for tasks like digging and loading soil or sand, while heavy-duty buckets handle tougher materials like rocks and demolition debris. Inspect bucket teeth and edges regularly to ensure optimal performance.
What are the benefits of using quick couplers?
Quick couplers allow you to switch between attachments quickly and efficiently, saving time and increasing productivity. High-quality quick couplers ensure secure attachment and reduce the risk of accidental detachment. Regular maintenance, such as lubrication and inspection of locking mechanisms, keeps them functioning reliably.
How can I improve the safety of my excavator operations?
Enhance safety by maintaining cab components like operator seats and control panels. Use backup cameras to improve visibility and reduce blind spots. Ensure warning alarms function properly to alert you to potential hazards. Regularly inspect these features to create a safer working environment.
Why should I invest in high-quality excavator parts?
High-quality parts, such as those offered by YNF Machinery, ensure durability, reliability, and optimal performance. They reduce downtime, enhance efficiency, and minimize the risk of unexpected failures. Investing in premium components saves money in the long run by extending the lifespan of your excavator and reducing repair costs.