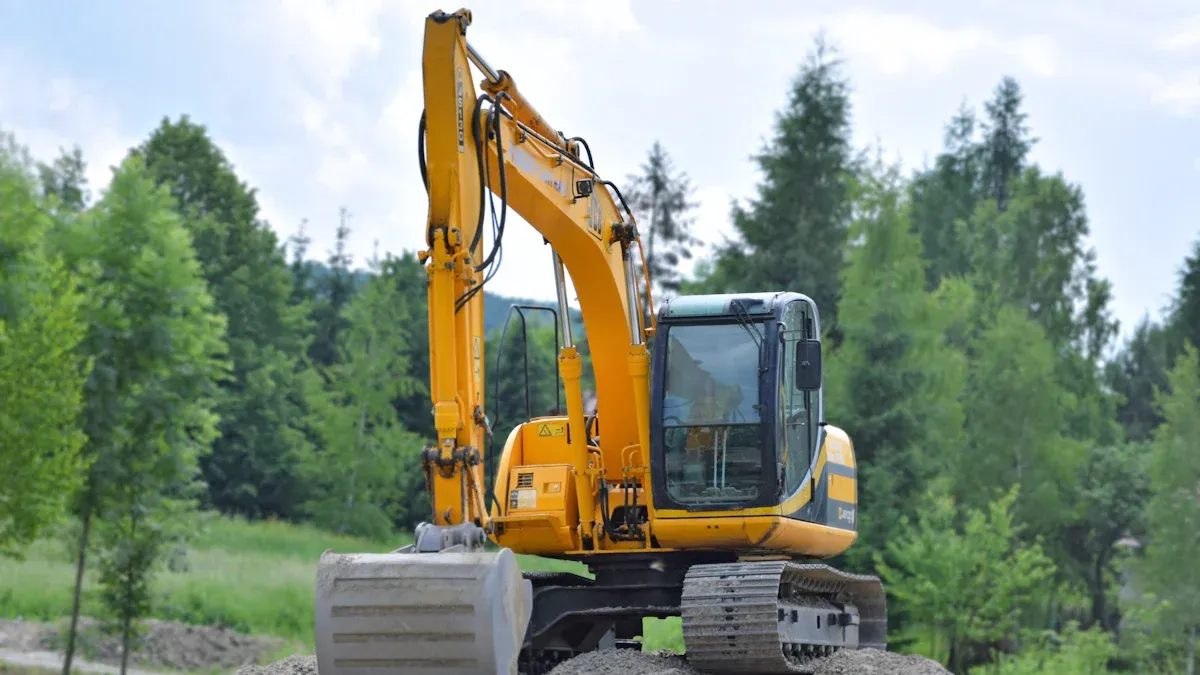
Choosing the right excavator tracks starts with knowing your machine. You need to measure your current tracks and match them to your work needs. The right excavator tracks help your machine perform better and keep you safe. Good choices also save money over time. > Tip: Careful selection prevents expensive mistakes and keeps your projects on track.
Key Takeaways
Measure your excavator track width, pitch, and number of links. This helps you get the right fit and avoid mistakes that cost money.
Pick tracks that match your machine’s make and model. Also, think about the ground where you work. This helps your machine work better and keeps you safe.
Choose the right tread pattern for your main terrain. This gives you better grip and stability. It also helps lower vibration.
Use rubber tracks on soft or paved ground. This makes less noise and protects the ground. Use heavy duty steel tracks on rough, rocky ground. This makes your tracks last longer.
Buy tracks from trusted sellers and check the warranties. Follow the right steps to install and take care of your tracks. This keeps your excavator working well and saves you money.
Excavator Tracks: Why the Right Choice Matters
Performance and Safety
Choosing the right excavator tracks makes a big difference in how your machine works each day. When you use tracks that fit your machine and match your job site, you get better track performance and safer operation. If you pick the wrong tracks, you may notice problems right away.
Your machine might move unevenly or lose traction.
Tracks that are too tight can strain parts like idlers and rollers.
Loose tracks may sag or slip, causing more wear on pins and bushings.
Misaligned tracks can vibrate and wear out faster.
Debris stuck in the tracks can slow you down or even stop your machine.
Tip: Always check your track tension and clear out any debris. This helps prevent track failures and keeps your excavator running smoothly.
Matching your tracks to the ground conditions and how often you use your machine also matters. Mud, rocks, and uneven surfaces all need different tread patterns. If you work on rough ground every day, you need tracks built for that environment. This choice keeps you safe and helps your machine perform at its best.
Cost and Longevity
The right excavator tracks do more than improve performance. They also save you money over time. Properly selected and well-maintained tracks can last up to 2,000 hours or more. Poorly matched tracks may only last 800 to 1,000 hours. That means you could double your track lifespan just by making the right choice.
Longer-lasting tracks mean fewer replacements and less downtime. You spend less on repairs and avoid unexpected costs from track failures. Good track selection boosts durability and keeps your projects on schedule.
Track Sizing and Measurement
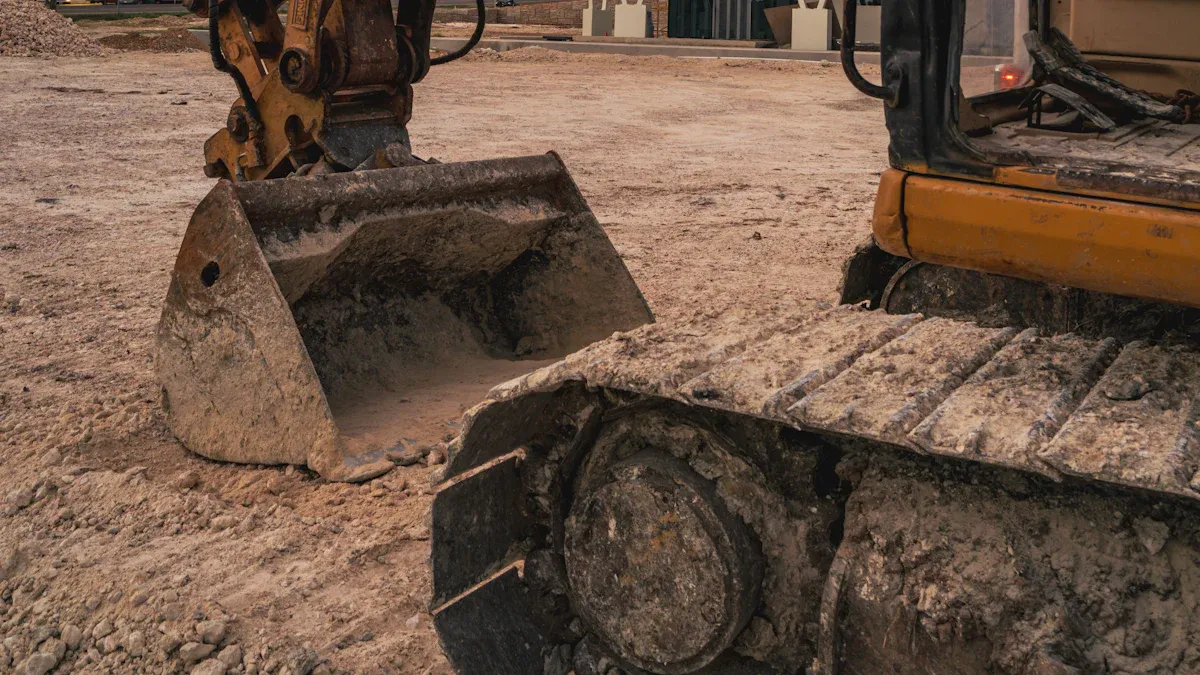
Choosing the right excavator track starts with getting the size right. You need to measure the width, pitch, and number of links to make sure you have the correct fitment for your machine. Using the wrong size can cause problems with performance and safety. Accurate measurements help you avoid costly mistakes and keep your excavator running smoothly.
Measuring Track Width and Pitch
You can measure the width of your excavator track using a tape measure. Place the tape across the top of the track from one side to the other. Always record this width in millimeters. This number tells you how wide the track is and helps you find a replacement that fits your machine.
To measure the pitch, look at the inside of the track. Place your tape measure at the center of one drive lug and measure the pitch by finding the distance to the center of the next drive lug. This distance, also in millimeters, shows how far apart the lugs are. Both width and pitch are important for making sure your new track will fit and work well.
Note: The industry standard for track size uses the formula Width x Pitch x Number of Links, all in millimeters. For example, a track marked 450x86x55 means 450mm width, 86mm pitch, and 55 links.
Counting Track Links
After you measure the width and pitch, you need to count the total number of links around the track. Each link is a drive lug that helps move the track along the undercarriage. You can count these by marking your starting point and counting each lug until you return to the start.
The number of links is just as important as the other measurements. If you use the wrong number, the track may not fit your machine. Too many links make the track loose and cause it to sag. Too few links make the track too tight, which puts extra pressure on parts like idlers and rollers. Both problems can lead to faster wear, poor performance, and even safety risks.
Tip: Always double-check your measurements before ordering new tracks. Accurate sizing helps you avoid installation issues and keeps your excavator safe and reliable.
Choosing Excavator Tracks for Your Application
Machine Make and Model
Start by checking your machine’s make and model. Every excavator needs tracks that fit its size and shape. Tracks must match the width, length, and tread pattern your machine uses. Using the wrong track can hurt the undercarriage and make your machine work worse. Some brands, like Camso, Bridgestone, and McLaren, make tracks for certain machines and jobs. Camso has tracks for tough jobs. Bridgestone makes tracks that last a long time and work well. McLaren offers tracks with different tread patterns for many types of ground. You can use guides to pick tracks that fit your machine’s make and model. Always look at your excavator’s manual or ask a trusted supplier before buying. This helps you avoid mistakes and keeps your machine working well.
Tip: Do not guess your track size. Use your manual or a supplier’s tool to check the right fit.
Ground Conditions and Terrain
Think about the ground where you will use your excavator. Different ground needs different tracks. Some places are soft and wet, while others are rocky or hard. If you work in mud, swamp, or after rain, you need tracks that grip slippery ground. Sandy or clay soil that gets slick when wet also needs special tracks. In these places, general duty tracks with wide surfaces help your machine stay on top and not sink. For rocky or rough ground, heavy-duty or strong tracks protect your undercarriage. Swamp tracks have sealed chains and longer frames to keep out water and dirt. Always pick tracks that match the ground to get the best safety and performance.
Common tough ground conditions:
Wet and marshy places
Loose or filled soil
Clay or sandy ground
Frozen or melting surfaces
Note: The right tracks for your ground help stop breakdowns and make your undercarriage last longer.
Tread Patterns
Tread patterns are important for how your excavator moves on different ground. The right pattern gives better grip and keeps your machine steady. For mud, straight bar treads give the most grip. On paved roads or finished ground, multi-bar treads lower shaking and protect the surface. Block treads are good for gravel or hard-packed soil and give more stability. C-pattern treads are good for many jobs and lower shaking. Some steel tracks have grouser bars for extra grip on rocks. Narrow tracks help you move in small spaces. Wide tracks give more stability on soft ground but can make turning harder.
Tread Pattern | Best Terrain | Benefit |
---|---|---|
Straight Bar | Mud, wet ground | Maximum traction |
C-pattern | General use | Balanced grip, less vibration |
Multi-bar | Paved surfaces | Less ground damage, smooth ride |
Block Tread | Gravel, hard-packed soil | Extra stability |
Tip: Pick your tread pattern based on the main ground you work on. This helps your machine stay safe and work well.
When you follow these steps, your excavator will fit the job. You also protect your machine and get the best results from your work.
Track Types: Rubber Track vs. Heavy Duty Tracks
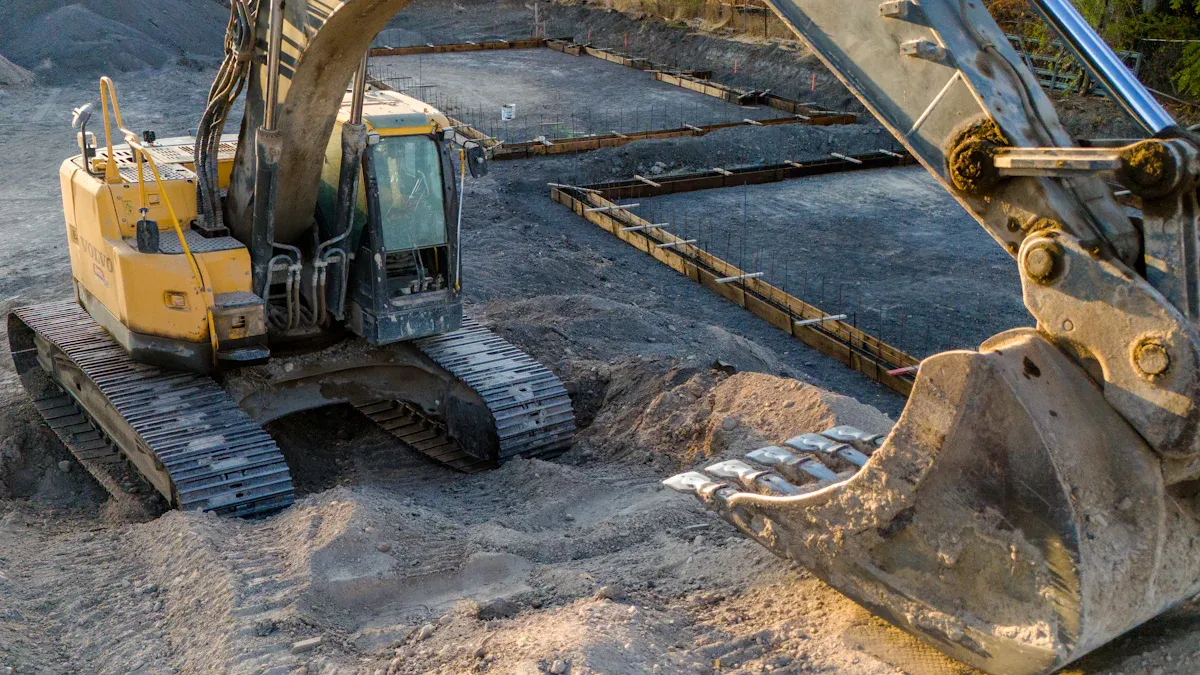
Rubber Track Benefits
You will notice many benefits when you choose a rubber track for your excavator. Rubber tracks make less noise and reduce vibration. This means you get a smoother and quieter ride. You can work in neighborhoods or near schools without disturbing people. Rubber also protects paved surfaces. It does not tear up roads or sidewalks like steel tracks can. You will find rubber tracks easy to maintain. They need less care than steel tracks. You can replace them quickly when needed. Many rubber tracks use an advanced rubber compound. This material gives extra strength and helps the track last longer on soft or finished ground.
Tip: Rubber tracks work best on grass, dirt, and paved surfaces where you want less noise and less ground damage.
Steel and Heavy Duty Tracks
Heavy duty tracks give you more strength and durability. You should use these tracks when you work on rocky, rough, or harsh ground. Steel tracks last longer than rubber tracks. They can handle sharp rocks and heavy loads without wearing out fast. If a steel track link breaks, you can replace just that link. This saves you money over time. Heavy duty tracks need regular care to prevent rust, but they stay strong in extreme heat or cold. You will see better stability and balance with steel tracks, especially on slopes or uneven ground.
Aspect | Steel Tracks (Heavy Duty) | Rubber Tracks |
---|---|---|
Durability | Lasts longer, best for harsh terrain | Wears faster, best for soft ground |
Maintenance | Needs regular care | Needs less care |
Repairability | Replace single links | Replace whole track if damaged |
Noise/Vibration | Louder, more vibration | Quieter, less vibration |
Surface Impact | Can damage pavement | Protects pavement |
Note: Heavy duty tracks cost more at first, but you replace them less often. This saves money in the long run.
Mini Excavator Track Features
Mini excavators need special tracks for stability and safety. Many mini excavator tracks use a 3S iron core design. This design uses drop-forged steel inside the rubber. The iron core gives extra strength and keeps the track from slipping off, even on slopes or when turning. You get better control and less risk of de-tracking. The advanced rubber compound in these tracks also helps them last longer and stay flexible. You can trust your mini excavator to stay steady and safe on many types of ground.
Tip: Always check for an iron core in your mini excavator track. This feature gives you more stability and strength for tough jobs.
Buying and Replacing Excavator Tracks
Where to Buy Tracks
You should buy excavator tracks from sellers you trust. The best brands give you good help, strong parts, and solid warranties. These sellers have good reviews because they are reliable and helpful. Here are some of the most trusted sellers for 2025:
Supplier | Key Attributes | Customer Feedback Highlights |
---|---|---|
Caterpillar (Cat) | Tough parts for hard jobs; great warranty and support. | Very reliable, lasts long, great help. |
Komatsu | Real, high-quality parts that fit well; sold worldwide and checked for quality. | Strong performance, on-time delivery, good quality. |
John Deere | Top undercarriage parts; very good customer service. | Works well, lasts long, helpful service. |
Always check with your machine’s maker or a trusted seller before you buy. This helps you avoid fake or weak tracks. Trusted sellers also help you pick the right track for your machine and job.
Tip: Look at online reviews and ask about the warranty before you buy. This keeps your money safe and helps you feel sure about your choice.
Ordering and Installation Tips
When you order new tracks, follow these steps to get the right ones:
Measure your old track’s width, pitch, and number of links. Good measurements stop fit problems.
Pick a track pattern that matches your main job site. For example, use smooth tracks for grass or C-pattern for wet weather.
Make sure the new tracks fit your machine’s make and model. This keeps your excavator safe and working right.
Choose tracks with strong belts or cords inside. These parts help stop stretching and make the track last longer.
Ask about the rubber used in the track. Hard rubber outside lasts longer, soft rubber inside makes it bend better.
Before you put on the tracks, read your machine’s manual. Use the right tools and wear safety gear. Always put the track on the right way. Add grease to set the tension until you see the right gap between the chain and rollers. After you finish, check for loose parts and make sure the snap ring is in its place.
Note: Check your tracks often and keep them oiled. This helps your new tracks last longer and keeps your machine safe.
Picking the right excavator tracks means you need to measure carefully. You should:
Measure the track width, pitch, and number of links in millimeters.
Make sure the track is tight enough and lined up right to stop early damage.
Choose a track that fits your machine’s make, model, and where you will use it.
Look for any damage or uneven wear before you put on new tracks.
Ask an expert or trusted dealer if you have a special job.
Doing these things helps your machine work better, keeps you safer, and saves money on fixing problems. Always check your measurements twice and talk to a supplier if you are not sure. The right tracks help your excavator last longer and work better.
FAQ
How often should you check your excavator tracks?
You should check your tracks before each use. Look for wear, damage, or loose parts. Regular checks help you catch problems early and keep your machine safe.
Can you use rubber tracks on rocky ground?
Rubber tracks work best on soft or paved ground. Rocks can cut or tear rubber. If you work on rocky sites, choose steel tracks for better durability.
What happens if you install the wrong size track?
The wrong size track can slip, sag, or break parts. Your machine may not move right. Always measure carefully and match the track to your machine’s specs.
How do you know when to replace your tracks?
Look for cracks, missing lugs, or deep cuts. If your machine shakes or loses grip, your tracks may need replacing. You can also check the wear marks on the track.
Do all brands fit every excavator?
No, not all brands fit every machine. You must match the track to your excavator’s make and model. Check your manual or ask a supplier for help.