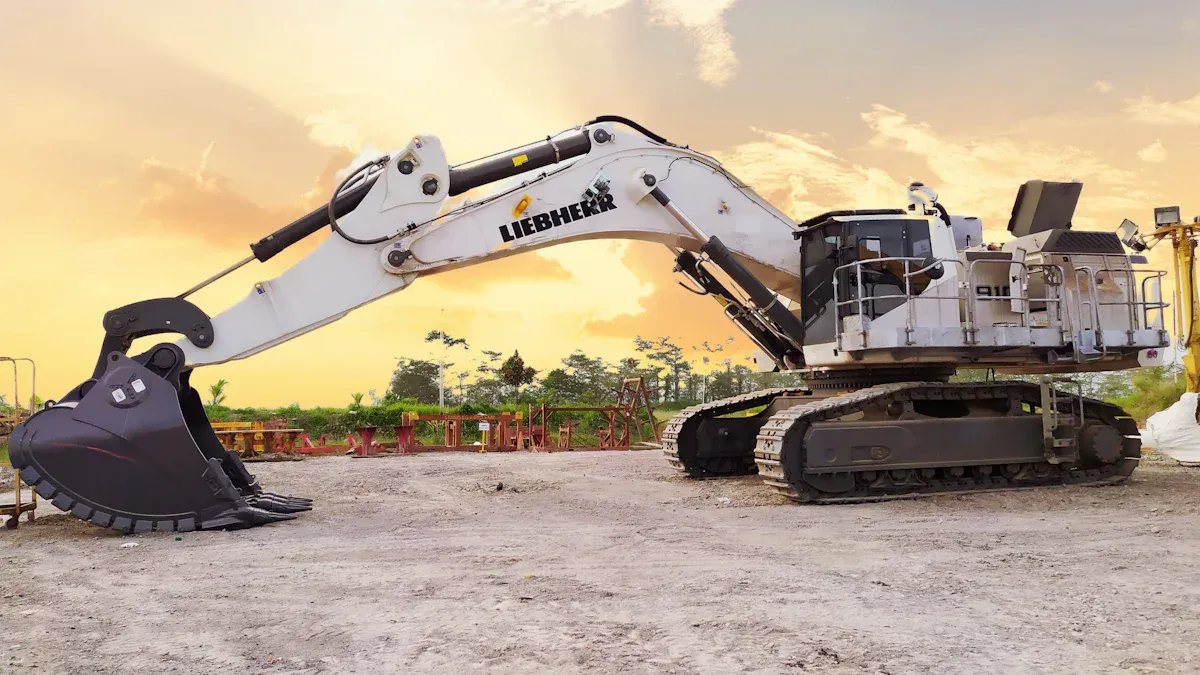
Excavator undercarriage systems consist of many main components that work together to support and move the machine efficiently. These key parts include the track chain, track rollers, carrier rollers, idlers, drive sprockets, track tensioner, pins and bushings, and guiding guards. Each component plays a vital role in keeping the excavator stable and mobile on rough terrain. An excavator undercarriage parts diagram is especially helpful for visualizing how these parts fit and function together. The table below outlines each part and its function:
Undercarriage Part | Description / Function |
---|---|
Track chain | Connects both sides; supports the machine’s weight |
Carrier roller | Supports the body; guides the track chain |
Guide wheel (Idler) | Maintains track chain tension; directs its movement |
Drive sprocket | Propels the machine by turning the track chain |
Track tensioner | Adjusts tightness to prevent the track from slipping off |
Load-bearing rollers | Support weight and facilitate track chain movement |
Understanding the excavator undercarriage parts through a detailed diagram helps operators and maintenance workers identify issues early. Components like bushings tend to wear out first, so regular inspections are crucial. Since undercarriage repairs can be costly, using an excavator undercarriage parts diagram is an effective way to locate and maintain these essential parts.
Key Takeaways
Excavator undercarriage parts include track chains, rollers, idlers, and sprockets. These parts work together to hold up the machine. They help the excavator move and stay steady on rough ground.
Cleaning and checking undercarriage parts often helps find damage early. This stops big repairs and keeps the excavator working well.
The track must be tight enough to work right. If it is too loose, it can slip or wear out fast. Operators should check and fix the track tension often.
Changing old parts like track shoes, rollers, and sprockets on time helps the machine last longer. It also keeps the excavator safe to use.
Using the correct parts and taking care of them the right way helps the machine work better. It also keeps the undercarriage safe, based on where you use the excavator.
Excavator Undercarriage Parts Diagram
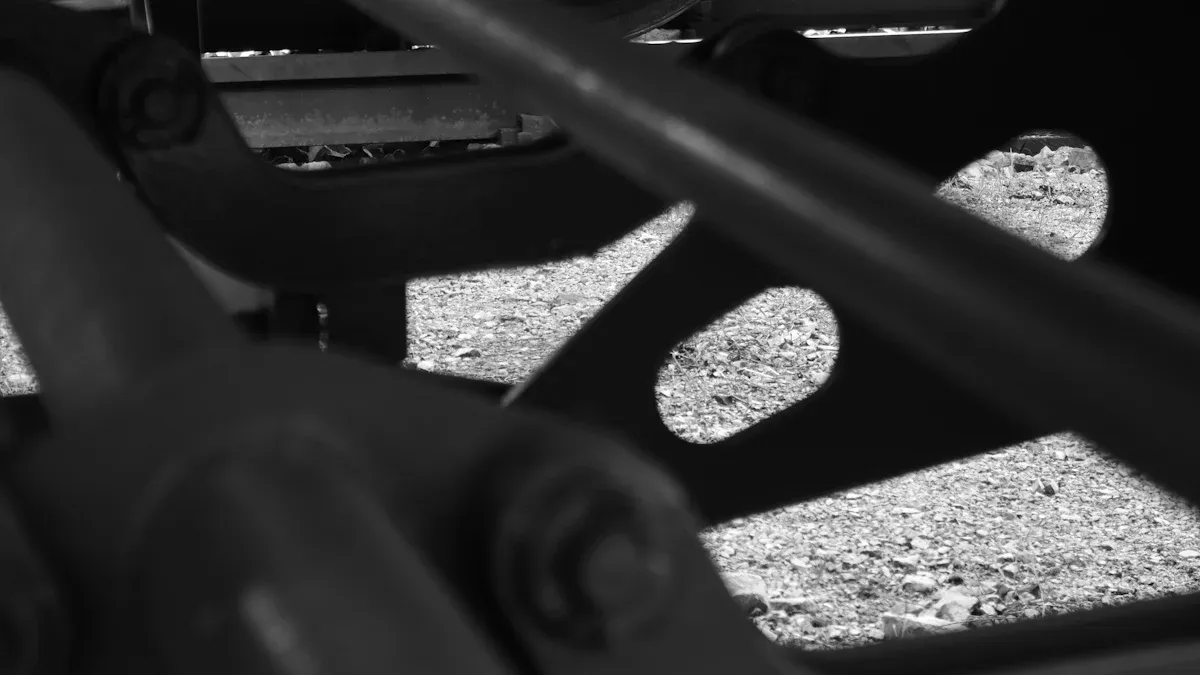
A detailed diagram of excavator undercarriage parts helps people see each part’s job. Each part is explained below to make it easier to understand.
Track Shoes
Track shoes, also called track pads, are attached to the track chains. They touch the ground and help the excavator move. These parts give the machine grip on different surfaces. Steel track shoes last a long time and work well on rough ground. Rubber pads are quieter and protect soft surfaces like asphalt. The choice between steel and rubber depends on where the excavator works.
Feature | Steel Track Shoes | Rubber Track Pads |
---|---|---|
Durability | Great for rough ground | Wear out faster on tough ground |
Noise | Loud | Quieter, less vibration |
Surface Impact | Can hurt pavement | Protects soft surfaces |
Track Chains
Track chains make a loop on both sides of the undercarriage. They connect the track shoes and let the excavator move forward and backward. Track chains are made from strong steel and are heat-treated to last longer. This makes them tough enough for heavy work. Keeping them oiled and checking them often stops them from stretching or breaking early.
Track Rollers
Track rollers, or bottom rollers, are at the bottom of the undercarriage. They hold up the excavator’s weight and guide the track. These rollers help the machine move smoothly, even on bumpy ground. Track rollers can last from 2,000 to 7,000 hours. Cleaning them and keeping the track tight helps them last longer.
Carrier Rollers
Carrier rollers, or top rollers, sit above the track chains. They hold up the top part of the track and spread the weight. These rollers keep the track straight and tight. They also help the excavator run smoothly and take in shocks and bumps. This protects the undercarriage and helps it last longer.
Sprockets
Sprockets are wheels with teeth that sit outside the wheelbase. They connect to the final drive and move the track chains. Sprockets turn engine power into movement. They also help keep the track tight and straight. If sprocket teeth wear down, the track can slip or come off. Checking and changing sprockets when needed keeps the excavator working well.
Idlers
Idlers are at the front or back of the undercarriage. They guide the track and help keep it tight. The idler wheel takes in shocks and keeps the track in place. If idlers or track adjusters break, the track can get loose or fall off. This causes more wear and expensive repairs. Checking idlers often helps them work right.
Track Frame
The track frame is the main support for all undercarriage parts. It holds the rollers, idlers, sprockets, and track chains together. The size and shape of the track frame affect how steady the excavator is. A strong track frame spreads out the weight and helps the machine work better.
Pins and Bushings
Pins and bushings link the pieces of the track chain. They let the track bend and fit the ground. These parts act like hinges and take in shocks and bumps. If they wear out, the track can stretch, sag, or make strange noises. Oiling them and changing them when needed stops big repairs and helps the track last longer.
Guiding Guards
Guiding guards, also called chain guards or rock guards, are put along the tracks. They keep the track chain in place and stop it from coming off. If these guards get worn or broken, the track can move out of place. Taking care of guiding guards keeps the excavator safe and working well.
Recoil Springs
Recoil springs are part of the track adjuster. They take in shocks and protect the track and idler from hard hits. When the excavator hits something, the recoil spring squeezes and keeps the track tight. This stops damage to the undercarriage. Checking recoil springs often helps them keep working.
Rubber Pads
Rubber pads can be put on steel track shoes to make less noise and protect roads. They are flexible and take in bumps, which is good for city work. But rubber pads wear out faster than steel on rough ground. Picking the right pad depends on where the excavator will work.
A clear diagram of excavator undercarriage parts helps workers find each part fast. It also helps them know what each part does and how to take care of it. When people know how these parts work together, the excavator stays strong and works well.
Key Parts of the Undercarriage
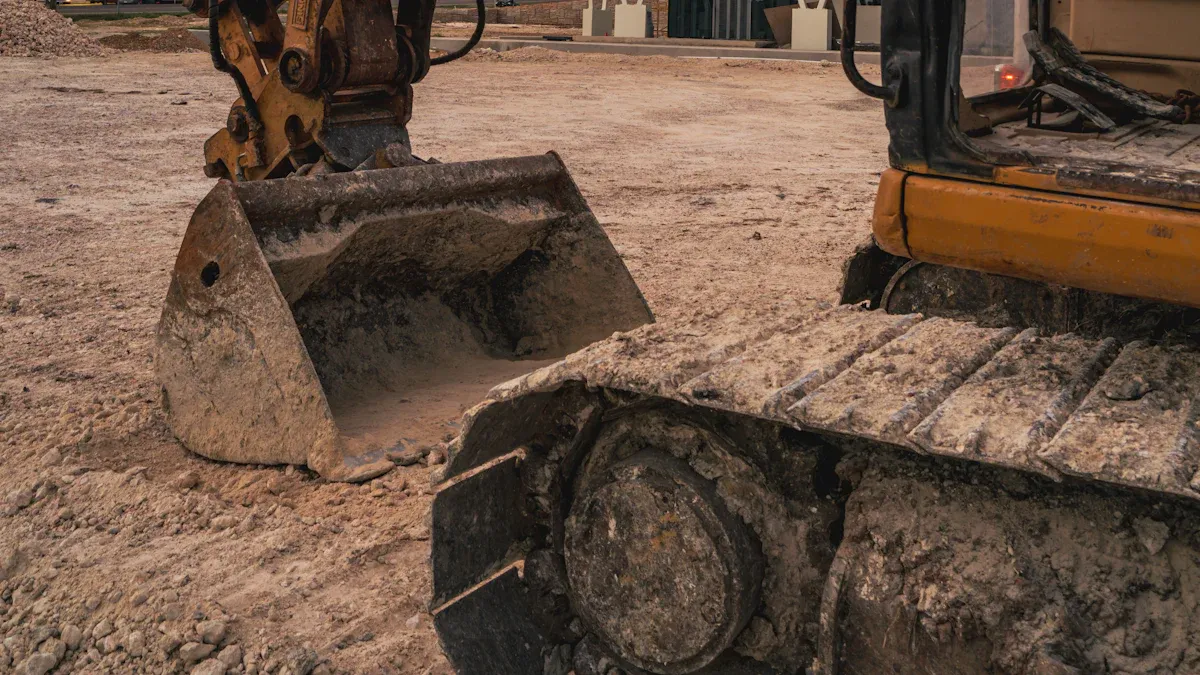
Support and Stability
The key parts of the undercarriage work together to keep the excavator steady and safe. The track rollers carry the weight of the machine and help spread it out over the ground. Carrier rollers keep the tracks in the right position, which helps with alignment and prevents the machine from tipping. Idlers, with their tension springs, absorb shocks from rough ground and keep the track tight. The drive sprocket moves the track and helps keep everything in place. Track shoes support the excavator and spread its weight, which is important for stability on soft or uneven ground. Chain links connect the track and make sure it stays tight. Regular maintenance of these parts helps prevent damage and keeps the undercarriage of heavy equipment stable during tough jobs.
Tip: Clean and check the undercarriage often. This reduces friction and wear, which helps the machine stay stable and safe during heavy lifting.
Mobility and Traction
The undercarriage gives the excavator the ability to move and grip the ground. Track pads touch the ground and provide traction. Wide tracks help the machine stay on top of soft soil, while narrow tracks give better grip on rocky ground. Track chains and shoes link the pads and allow smooth movement. Sprockets engage with the track links to move the excavator forward or backward. Rollers guide the tracks and keep them moving straight. Idlers control the tension, which helps with alignment and smooth movement. Rock guards protect the undercarriage from rocks and debris. The track frame spreads the weight and helps the excavator move safely on uneven ground. Good maintenance of these parts keeps mobility and traction strong, even on rough terrain.
Wide tracks lower ground pressure and improve stability.
Narrow tracks increase traction on hard surfaces.
Supporting parts like rollers, idlers, and rock guards keep the tracks aligned and protected.
Energy Transfer
The undercarriage transfers energy from the engine to the tracks. The engine creates power and sends it to the hydraulic pump. The pump turns this power into hydraulic energy. The travel motor receives the hydraulic energy and changes it back into mechanical energy. The final drive gearbox increases torque and lowers speed. This energy goes to the sprocket, which pulls the track and moves the excavator. Rollers, idlers, and springs guide the track and keep it tight during movement. Each part must work together for smooth and efficient energy transfer.
The engine makes mechanical energy.
The hydraulic pump turns it into hydraulic energy.
The travel motor and final drive send power to the sprocket.
The sprocket pulls the track, moving the excavator tracks.
Rollers and idlers keep the track aligned and tight.
When all key parts of the undercarriage work together, the excavator can move, lift, and stay stable on any job site.
Excavator Undercarriage Maintenance
Common Wear Issues
Operators see undercarriage wear for many reasons. Sand and rocks rub against the track and other parts. This can make them wear out faster. Bumpy ground can cause cracks or leaks in the parts. Mud and dirt can pile up and hold water. This can cause rust or make seals break. Using the machine wrong, like turning too sharply or carrying too much, adds extra stress. Signs of wear are missing rubber, wires showing, cracks, or uneven spots. Leaks from idlers and rollers, weird-shaped sprocket teeth, and stuck debris also mean trouble. Checking the undercarriage every day helps find these problems early. This stops the damage from getting worse.
Maintenance Tips
Taking care of the undercarriage means cleaning off dirt and mud often. Operators should look at all parts, like bearings, bolts, chains, and rollers, for damage or if they are loose. Keeping the track tight helps the undercarriage stay steady and last longer. Oiling parts and changing them when needed makes them work better. Use the right products from the maker to lower friction and help parts last. Preventive care, like checking if things line up and watching for wear, helps spot trouble before it gets bad. Doing regular checks and service makes the excavator work better and saves money by stopping big repairs.
Tip: Clean the undercarriage after every use. This easy step stops dirt from building up and causing damage later.
When to Replace Parts
Knowing when to change undercarriage parts keeps the excavator safe and working well. The table below shows how long parts last and what to look for:
Component | Expected Lifespan (hours) | Signs of Wear | Maintenance Tips |
---|---|---|---|
Track Shoes | 2,000–3,000 | Getting thin, cracks, less grip | Check for wear, keep tight, clean often |
Rollers | 3,000–5,000 | Noises, shaking, oil leaks | Oil them, check for damage |
Idlers | 4,000–6,000 | Noises, not straight, surface marks | Check them, keep them lined up |
Sprockets | 3,000–4,000 | Worn teeth, chain slips | Watch teeth, keep track tight |
Track Chains | 3,000–5,000 | Stretching, sagging, pin wear | Clean, keep tight, oil them |
Changing parts on time stops more damage and keeps the machine working. Not taking care of the undercarriage costs more and can be unsafe. Taking care of the undercarriage is very important. Regular checks and fixing parts help the excavator last longer and run smoothly.
Knowing what each undercarriage part does helps people take better care of their machines. When operators check and fix parts often, they can stop big problems before they happen. This saves money and keeps the excavator working well.
Operators who learn to look at track chains, rollers, idlers, and sprockets can find issues early and help the machine last longer.
Good care means:
Clean and check parts every day.
Do what the manufacturer says.
Write down all the work you do.
This knowledge helps everyone stay safe, spend less, and use the excavator for more years.
FAQ
What causes the most wear on an excavator undercarriage?
Sand, rocks, and mud wear out parts the most. These things rub against metal and cause damage. Turning sharply and carrying heavy loads add more stress. Operators should clean the undercarriage often to stop damage.
How often should operators inspect the undercarriage?
Operators need to check the undercarriage every day. Quick checks help find loose bolts, leaks, or worn parts. Finding problems early stops bigger issues and keeps the machine safe.
Can operators replace undercarriage parts themselves?
Operators can change easy parts like rubber pads or track shoes. For harder repairs, like rollers or sprockets, a trained technician should do the work. Safety is always the most important thing.
Why does track tension matter?
Good track tension keeps the track in place. If the track is too loose, it can slip off. If it is too tight, it wears out faster. Operators should check and adjust the tension often.
What signs show it is time to replace a part?
Look for cracks, missing rubber, oil leaks, or worn sprocket teeth. Strange noises or shaking mean something is wrong. Operators should replace broken parts right away.
Tip: Check the undercarriage often and fix problems fast. This helps the excavator last longer and work better.