
The excavator undercarriage is the base of every excavator. It connects the top part to the ground. This system has tracks, rollers, and other parts. These parts help support, steady, and move heavy machines on rough ground. Operators who know about the undercarriage can save money on repairs. They can also make the machine last longer. The table below shows how taking care of undercarriage parts, like track rollers and drive sprockets, affects cost and how long they last:
Aspect | Evidence Summary |
---|---|
Cost Impact | Poor maintenance increases repair costs by 200-300%. |
Lifespan | Well-maintained undercarriages last up to 6,000 hours, while poor care halves this. |
Key Takeaways
The excavator undercarriage holds up the machine’s weight. It helps the machine move safely on rough ground.
Important parts like tracks, rollers, sprockets, and the final drive work together. They keep the excavator steady and able to move.
Checking and cleaning the undercarriage often stops damage and expensive fixes. This helps the machine last longer and work better.
Taking care of the undercarriage, like checking track tension every day and greasing parts, saves money. It also helps stop breakdowns.
Operators who know about the undercarriage and take care of it make the job safer. They also help save fuel and do better work.
Excavator Undercarriage Overview
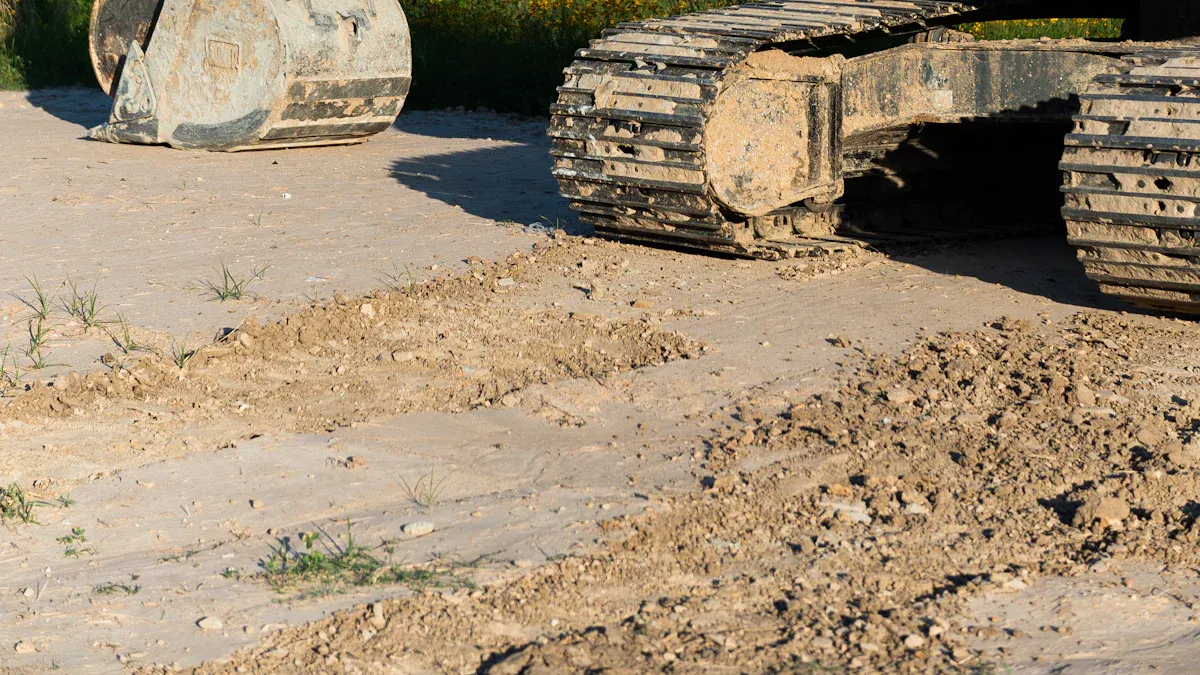
Purpose and Function
The excavator undercarriage is the bottom part of the machine. It links the top part to the ground. It holds up all the weight of the excavator. The undercarriage uses tracks and other important parts. These help the machine move and stay steady. The tracks let the excavator go over bumpy or muddy ground. The undercarriage has parts like track shoes, track chains, rollers, idlers, sprockets, and the final drive. All these parts work together to keep the machine balanced and moving.
The undercarriage holds up the excavator’s weight.
It keeps the machine steady when digging or lifting.
The track frame spreads out the weight.
Tracks and sprockets help the machine move.
Track shoes help the machine grip the ground.
Rollers and idlers guide and hold up the tracks.
Sprockets help move the excavator by turning the tracks.
These jobs make the undercarriage very important for heavy equipment. Without these parts, the excavator could not move or work safely.
Importance for Excavator Performance
The undercarriage is a big part of how well an excavator works. If the undercarriage is in good shape, the machine is more stable and lasts longer. Tracks help the excavator move on many types of ground. Rollers and idlers keep the tracks in place and stop them from slipping. Sprockets and the final drive send power from the engine to the tracks so the machine can move.
Note: Taking care of undercarriage parts stops breakdowns and helps the excavator work well. Finding worn track shoes, chains, rollers, or sprockets early can save money and time.
When the undercarriage is well cared for, the excavator works faster and better. Broken or worn parts can slow down work and cost more to fix. Operators who know about the undercarriage and take care of it can help the machine last longer and work better.
Undercarriage Components
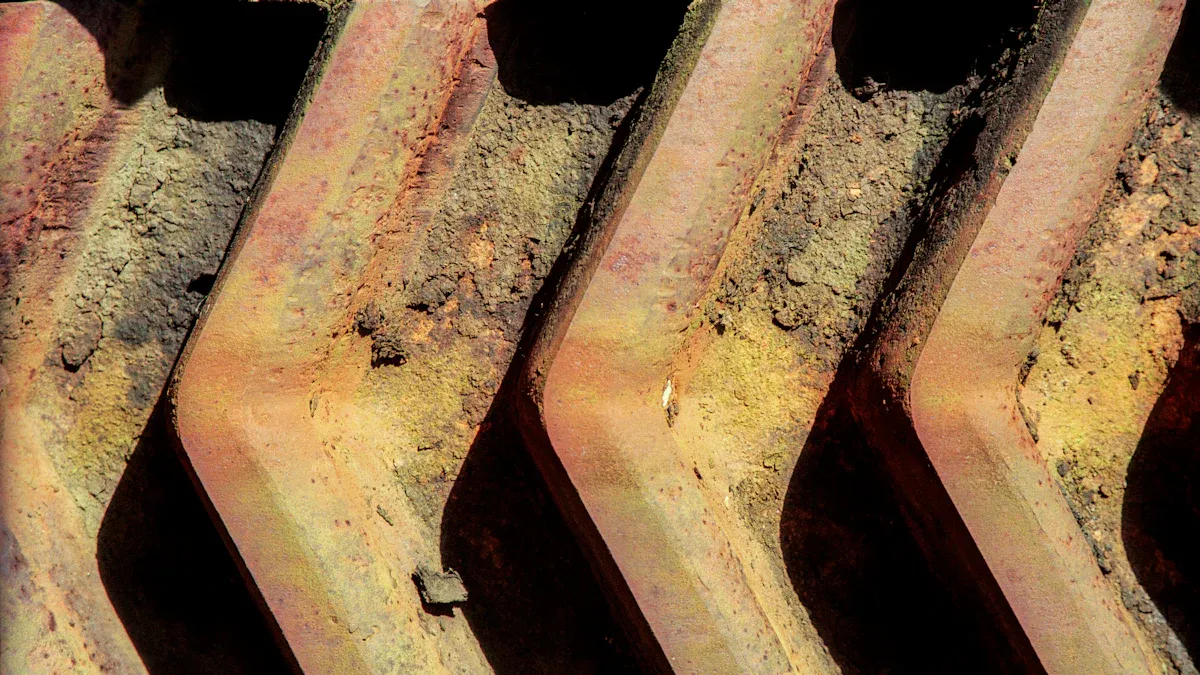
The excavator undercarriage has many parts that work together. These parts help the machine move, stay steady, and hold its weight. Each part has a special job. All of them help the excavator last longer and work better. If operators know about these parts, they can keep their machines working and avoid big repair bills.
Track Frame
The track frame is like the skeleton of the undercarriage. It holds all the track parts in place. It also connects them to the main body of the excavator. Track frames are made from different materials. Each material changes how strong and tough the frame is:
Steel: This is strong and bends without breaking. It is cheap and works well for most excavators.
Aluminum: This is light and stiff. But it is not as tough and can wear out faster.
Titanium: This is very strong and bends well. But it costs a lot and is hard to make.
Carbon Fiber Composites: This is strong and light. But it needs careful building to last a long time.
The track frame spreads the excavator’s weight over the tracks. This helps the machine stay balanced on rough ground. The material and quality of the frame decide how long it will last.
Excavator Tracks and Track Chains
Excavator tracks and track chains help the machine move on many surfaces. There are two main types of tracks: steel and rubber. The table below shows how they are different:
Feature | Steel Tracks | Rubber Tracks |
---|---|---|
Wear Resistance | Lasts longer and handles heat and debris | Not as tough and can be cut by sharp things |
Application Suitability | Good for rough or heavy work | Best for grass, dirt, or city areas |
Noise and Vibration | Makes more noise and shakes more | Quieter and smoother |
Surface Impact | Can hurt soft ground | Protects soft ground |
Maintenance | Needs cleaning and checks often | Easier and cheaper to change |
Hybrid Option | Can add rubber pads for protection | N/A |
Track chains link the track shoes and help the tracks move smoothly. They are made from strong steel and special pins. Good seals keep oil in and dirt out. This helps the parts last longer. Some chains have buffers to soak up shocks and protect other parts. Picking the right chain and taking care of it helps the undercarriage last longer and need fewer fixes.
Track Shoes
Track shoes are the parts that touch the ground. They help the excavator grip mud, rocks, or gravel. The size and shape of the grooves in the shoes matter. Bigger and deeper grooves help water drain and stop slipping. The way the grooves are set also helps the machine grip better.
Worn track shoes make the machine slip and lose balance. Taller grousers grip better but can hurt the ground and wear out faster. When track shoes wear down, the excavator is less stable, especially on soft ground. Checking and changing worn shoes keeps the machine safe.
Rollers (Bottom and Carrier)
Rollers hold up the excavator and guide the tracks. There are two kinds: bottom rollers hold the machine’s weight, and carrier rollers hold the top of the tracks. If rollers break, the weight is not spread right. This can hurt other parts like the track chain. Broken rollers can make the track sag or fall off. This is dangerous and can stop work. Checking and changing rollers on time keeps the undercarriage safe and working.
Idlers and Recoil Springs
Idlers are big wheels at the front that guide the tracks. Recoil springs connect to the idlers and act like shock absorbers. When the track hits something hard, the idler moves back and the spring squishes. This soaks up the shock and keeps the frame safe. This system keeps the track tight, even if mud builds up. Recoil springs also stop the tracks from getting too tight, which can break parts.
Tip: Operators should look at idlers and recoil springs every day for leaks or damage. Checking often helps find problems early and saves money.
Sprockets
Sprockets are toothed wheels at the back that move the tracks. They send power from the final drive to the tracks. Sprockets wear out when the chain stretches, the parts are not lined up, or the metal is weak. Too much weight, not enough oil, and rough work can also wear them out faster.
To stop sprocket wear:
Keep the sprocket and chain lined up.
Oil them often.
Clean off dirt and mud.
Use strong parts and put them in right.
Teach operators not to stop fast or overload.
The way sprockets are made changes how well power moves to the tracks. Strong metal and good tooth shapes help them last longer and save fuel.
Final Drive
The final drive is a main part that powers the tracks. It has three main pieces:
Hydraulic motor: Changes hydraulic power into turning power.
Reduction gear system: Slows the motor and makes it stronger.
Sprocket: Connects to the tracks and moves the machine.
These parts work together to send power from the hydraulic system to the tracks. This lets the excavator move and turn. Keeping the final drive clean and oiled stops it from getting too hot or wearing out. The track must not be too loose or too tight, or the final drive can break early. Checking oil and filters often keeps the final drive and undercarriage working well.
The excavator undercarriage needs all these parts to work right. Each part helps the others. Together, they help the machine move, stay steady, and last longer. Operators who know about these parts can keep their excavators working and avoid big repair costs.
How Undercarriage Parts Work Together
Movement and Power
The undercarriage has many parts that help the excavator move. Each part does something important for travel on rough ground. Tracks go around the track frame and connect to sprockets. The final drive gives power from the engine to the sprockets. Sprockets spin the tracks to move the excavator forward or backward. Rollers and idlers guide the tracks and keep them tight. Track chains hold the track shoes and help the tracks move smoothly.
If any undercarriage part wears out, the excavator may not move well or could stop.
Loose tracks or stuck rollers make the machine use more fuel and slow it down.
Not doing maintenance makes repairs cost more and can delay work.
All undercarriage parts must work together for smooth movement and good productivity.
Operators should clean tracks and rollers often. Dirt and rocks can get stuck and make rollers freeze or bolts come loose. Checking parts often helps find problems before they get worse. Good care keeps the tracks moving and helps the excavator finish jobs faster.
Stability and Load Support
The undercarriage gives the excavator a strong base. Tracks spread the weight over a big area. This stops the machine from sinking into soft ground. The track frame, rollers, and sprockets help balance the excavator. Rollers and idlers share the weight and keep the tracks tight. Track shoes grip the ground and stop slipping.
The undercarriage holds up the whole machine and keeps it steady.
Tracks and rollers help the excavator stay balanced on hills or bumpy ground.
Track chains and sprockets work together to move the machine without slipping.
Good care stops problems and keeps the excavator safe.
The undercarriage design lets the excavator work on many types of soil. Tracks help the machine grip and climb over rocks or mud. When all parts work together, the excavator can carry heavy loads and stay steady, even on rough ground.
Excavator Undercarriage Maintenance
Inspection Tips
Good maintenance starts with careful checks. Operators should look at the undercarriage every day before work. They need to find loose bolts, broken parts, or things stuck in the tracks. Tools like vernier calipers help measure chain gaps and pin wear. Infrared thermal imagers can find hot spots in bearings. Hot spots may mean damage is starting. Turning rollers by hand helps find if they are stuck or rough.
The table below shows when to check and what to look for:
Interval | Inspection Tasks |
---|---|
Daily | Check track tension, remove debris, inspect chain links, sprockets, rollers, and tighten bolts. |
Weekly | Measure chain elongation, check drive gear clearance, inspect buffer spring length. |
Monthly | Flip track assembly, test for seal leaks, retighten bolts. |
250/500/1000h | Inspect and replace worn parts, lubricate, check alignment, and adjust tension. |
2000h/Annual | Disassemble, replace worn assemblies, check for frame deformation, upgrade lubrication system. |

Signs of Wear
Operators should look for signs of undercarriage problems. Too much shaking, odd sounds, or a bumpy ride can mean parts are worn or not lined up. Tracks that look uneven, loose chains, or cracks and dents are warning signs. Worn track shoes can make the machine slip and lose grip. Warm joints or oil leaks near rollers and idlers also show damage. If the excavator pulls to one side or slows down, the undercarriage might need fixing.
Finding these signs early stops bigger problems and keeps the machine safe.
Preventive Care
Taking care of the undercarriage helps it last longer. Operators should clean off dirt, rocks, and mud after each shift. Greasing parts every day lowers friction and pushes out dirt. Checking and setting track tension right stops parts from wearing out too soon. Changing worn track shoes and rollers before they break saves money. Operators should not make sharp turns or drive on rough ground to protect parts. Following the maker’s care plan helps all parts last longer.
Doing regular checks, cleaning, and greasing makes undercarriage parts last longer and keeps the machine working.
Knowing about undercarriage parts helps operators make excavators work better and cost less. These parts can be half of all the money spent to own and use an excavator. Checking and oiling the parts often helps them last longer and stops big repair bills.
Taking care of the undercarriage saves fuel and keeps the machine safe.
Looking at the parts every day and following a plan helps stop problems and keeps jobs going.
Operators who learn about undercarriage systems keep their machines in good shape and get more use from them.
FAQ
What is the most common cause of undercarriage wear?
Dirt, rocks, and mud often get stuck in the tracks. These things rub on metal parts and cause them to wear out. Cleaning the tracks often helps stop this problem.
How often should operators check track tension?
Operators need to check track tension every day before work. The right tension keeps the tracks safe and helps the excavator work well.
Can operators replace undercarriage parts themselves?
Trained operators can change some parts, like track shoes or rollers. But if the repair is hard, a professional technician should do it.
Why do excavators use tracks instead of wheels?
Tracks spread the machine’s weight over more ground. This helps the excavator move on soft or bumpy ground without sinking.
What happens if operators ignore undercarriage maintenance?
If operators skip maintenance, parts wear out faster and break more. Repairs cost more, and the excavator can become unsafe.