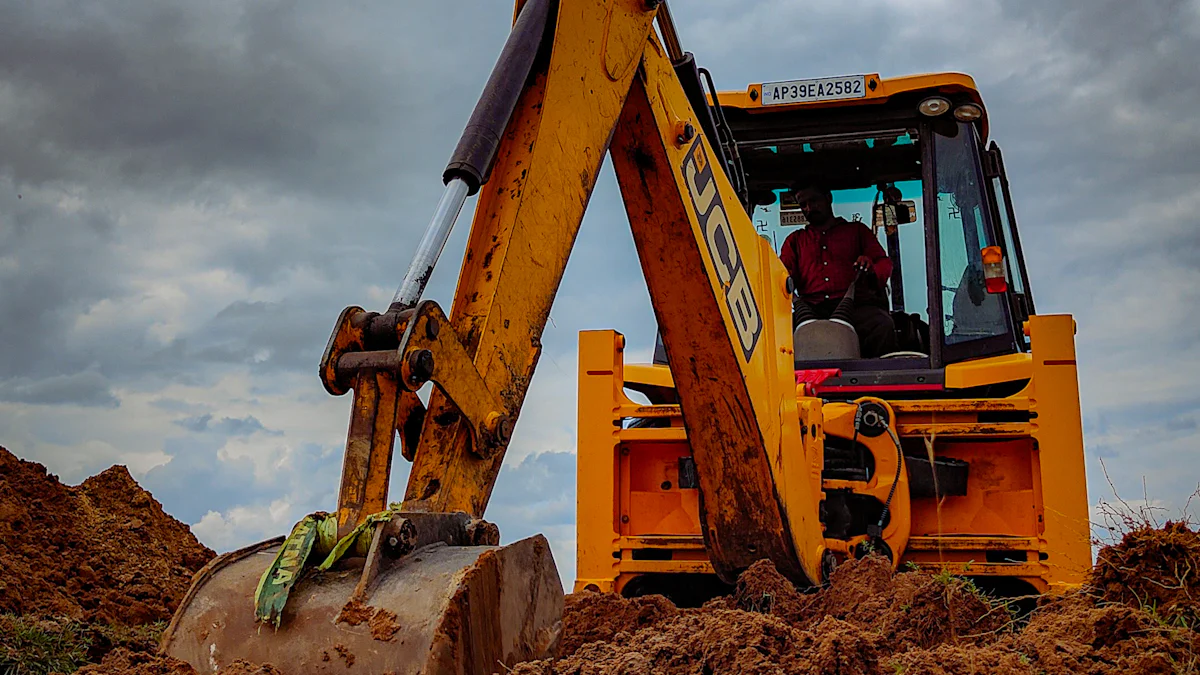
Excavator jaw crusher buckets revolutionize material processing by combining the functionality of a crusher with the versatility of an excavator. These innovative attachments enable on-site crushing of materials like concrete, rock, and debris, eliminating the need for additional machinery. By utilizing the excavator’s hydraulic power, they deliver efficient performance in demanding environments. Industries such as construction, demolition, and mining rely on these buckets to streamline operations, reduce waste, and enhance productivity. Their ability to recycle materials directly on-site makes them indispensable tools for modern projects focused on cost efficiency and sustainability.
Key Takeaways
Excavator jaw crusher buckets combine the power of a crusher with the versatility of an excavator, enabling efficient on-site material processing.
These buckets are built with durable materials like HARDOX steel, ensuring they withstand heavy-duty operations and reduce maintenance needs.
Adjustable jaw plates allow for customizable output sizes, making these buckets suitable for various applications, from recycling concrete to processing natural stone.
Using these buckets minimizes transportation and disposal costs by allowing contractors to crush materials directly on-site, enhancing project efficiency.
Excavator jaw crusher buckets are compatible with a wide range of excavator models, maximizing investment and simplifying setup.
Regular maintenance, including inspections and timely replacement of worn components, is crucial for maintaining the performance and longevity of these buckets.
Choosing a reliable manufacturer like YNF Machinery ensures access to high-quality products and comprehensive support, enhancing operational success.
Key Features of Excavator Jaw Crusher Buckets
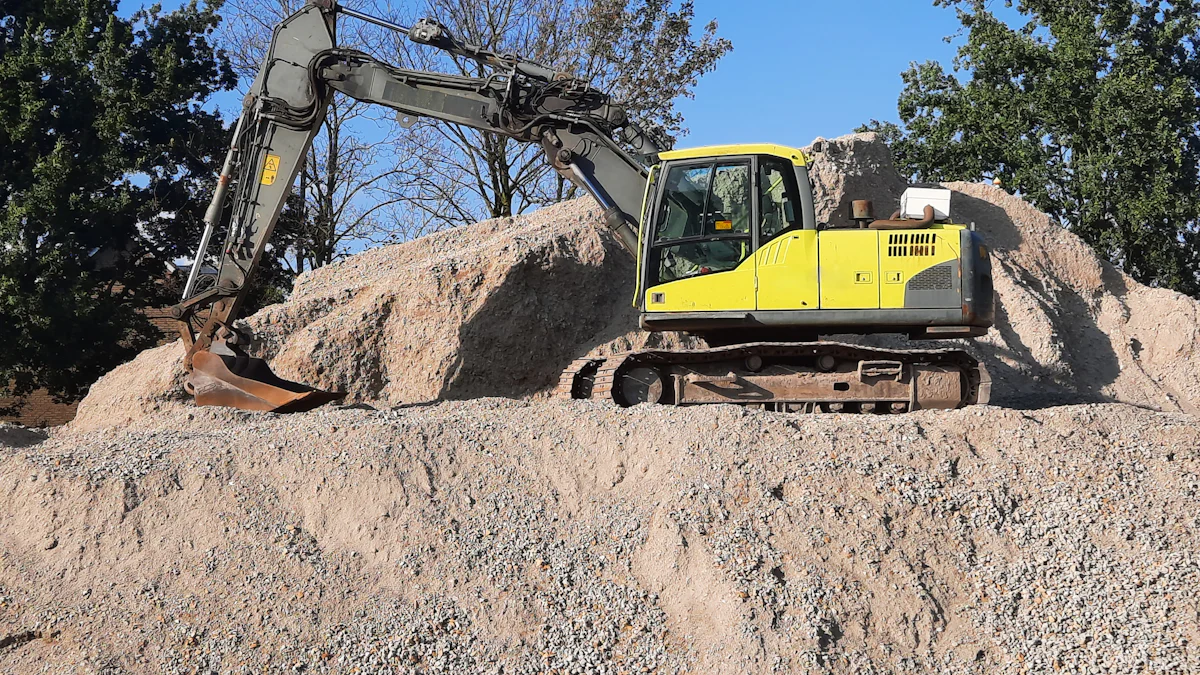
Durable Construction and High-Strength Materials
Excavator jaw crusher buckets are engineered with durability in mind. Manufacturers often use materials like HARDOX steel, known for its exceptional wear resistance and strength. This robust construction ensures the bucket can withstand the rigors of crushing hard materials such as concrete, rock, and brick. For example, some models incorporate crushing plates made of 18% manganese cast, enhancing their ability to endure heavy-duty operations. These features make the buckets reliable tools for demanding environments, reducing the need for frequent maintenance and replacements.
Compatibility with Various Excavator Models
One of the standout features of excavator jaw crusher buckets is their adaptability. These buckets are designed to fit a wide range of excavator models, from compact machines to larger equipment. This compatibility allows contractors to use the same bucket across multiple projects, maximizing their investment. Additionally, the hydraulic systems of excavators power these buckets, eliminating the need for external energy sources. This integration simplifies the setup process and ensures seamless operation, regardless of the excavator’s size or brand.
Efficient Crushing Mechanism Powered by Hydraulic Systems
The hydraulic-powered crushing mechanism is a defining characteristic of excavator jaw crusher buckets. This system enables the bucket to deliver high crushing force, efficiently breaking down materials on-site. The design typically includes a fixed jaw and a movable jaw, which work together to compress and crush materials. Some models feature reversible running directions, minimizing downtime caused by blockages. Adjustable jaw plates further enhance efficiency by allowing users to customize the output size based on specific project requirements. This flexibility ensures optimal performance in various applications, from demolition to material recycling.
Adjustable Jaw Plates for Versatile Crushing
Excavator jaw crusher buckets feature adjustable jaw plates, offering unmatched versatility for various crushing tasks. These plates allow operators to modify the output size of crushed materials, ensuring compatibility with specific project requirements. For instance, some models provide options for standard, fine, and ultra-fine crushing, with tooth pitches ranging from 30mm to as small as 10mm. This adaptability makes the buckets suitable for diverse applications, such as recycling concrete, processing natural stone, or crushing demolition debris.
The ability to adjust jaw plates enhances operational efficiency by reducing the need for additional equipment. Contractors can switch between different crushing specifications without delays, streamlining workflows on-site. Furthermore, the replaceable nature of these plates ensures prolonged usability, as worn components can be swapped out promptly. This feature minimizes downtime and maintenance costs, making these buckets a cost-effective solution for material processing.
Ease of Installation and User-Friendly Operation
Excavator jaw crusher buckets are designed for seamless integration with excavators, prioritizing ease of installation and operation. These buckets attach directly to the excavator’s hydraulic system, eliminating the need for external power sources. This setup simplifies the installation process, allowing operators to get started with minimal effort. Additionally, the hydraulic-powered mechanism ensures smooth and efficient performance, even in demanding environments.
Manufacturers emphasize user-friendly designs to enhance operator experience. Features such as reversible running directions help prevent blockages, reducing interruptions during operation. Some models also include dust suppression systems, improving visibility and safety on-site. The intuitive controls and straightforward maintenance requirements make these buckets accessible to operators with varying levels of expertise. By combining simplicity with functionality, these attachments empower contractors to achieve optimal results with minimal training or technical challenges.
Technical Specifications of Excavator Jaw Crusher Buckets
Bucket Capacity and Weight Variations
Excavator jaw crusher buckets come in a variety of capacities and weights to suit different project requirements. These buckets typically range from compact models designed for smaller excavators to larger options capable of handling heavy-duty tasks. For instance, some models are compatible with excavators weighing between 10 and 54 tons, ensuring flexibility across various equipment sizes. The bucket capacity often determines the volume of material that can be processed in a single cycle, with some units capable of crushing up to 18 cubic yards per hour.
Manufacturers design these buckets with wear-resistant materials like HARDOX steel to maintain durability despite their weight. This ensures that even the heaviest buckets remain reliable under demanding conditions. Operators should consider both the bucket’s weight and their excavator’s lifting capacity to ensure safe and efficient operation.
Crushing Force and Hydraulic Pressure Requirements
The crushing force of excavator jaw crusher buckets depends on the hydraulic pressure supplied by the excavator. These buckets utilize the excavator’s hydraulic system to power their crushing mechanism, which typically includes a fixed jaw and a movable jaw. The hydraulic pressure requirements vary by model, with some units demanding pressures as high as 250 bar to achieve optimal performance.
A strong crushing force enables these buckets to process tough materials like concrete, rock, and brick efficiently. Features such as reversible running directions and adjustable jaw plates enhance the crushing process by minimizing blockages and allowing operators to customize the output size. This adaptability ensures that the bucket performs effectively across a range of applications, from demolition to material recycling.
Recommended Excavator Size and Power Compatibility
Selecting the right excavator size is crucial for maximizing the performance of jaw crusher buckets. These attachments are designed to work with excavators of specific sizes and power outputs. For example, some models are compatible with machines weighing between 22.5 and 36 tons, while others cater to smaller or larger excavators.
The excavator’s hydraulic power plays a significant role in the bucket’s efficiency. Units with robust hydraulic systems can deliver higher crushing forces, enabling faster material processing. Operators should consult the manufacturer’s specifications to ensure compatibility between the bucket and their excavator. This alignment not only enhances performance but also reduces wear and tear on both the bucket and the excavator.
Material Throughput Rates and Efficiency
Excavator jaw crusher buckets excel in material throughput, offering impressive efficiency for on-site crushing tasks. These attachments can process a wide range of materials, including concrete, rock, and demolition debris, with throughput rates varying based on the bucket model and excavator size. Some models handle up to 18 cubic yards of material per hour, making them ideal for high-demand projects. The crushing mechanism, powered by the excavator’s hydraulic system, ensures consistent performance even under heavy workloads.
The adjustable jaw plates play a pivotal role in optimizing throughput. Operators can modify the output size to match project requirements, ensuring efficient material processing without additional equipment. For instance, buckets equipped with standard, fine, and ultra-fine jaw plates allow users to achieve particle sizes ranging from 30mm to as small as 10mm. This adaptability enhances productivity by reducing downtime and enabling seamless transitions between tasks.
Features like reversible running directions further boost efficiency by minimizing blockages during operation. Dust suppression systems, included in some models, improve visibility and safety, allowing operators to maintain steady workflows. By combining high throughput rates with user-friendly features, these buckets deliver exceptional value for construction, demolition, and recycling projects.
Dimensions and Design Options
Excavator jaw crusher buckets come in various dimensions and designs to accommodate diverse operational needs. Manufacturers offer models compatible with excavators ranging from compact machines to heavy-duty equipment, ensuring flexibility across different job sites. For example, some buckets are designed for excavators weighing between 10 and 54 tons, providing options for both small-scale and large-scale projects.
The design of these buckets prioritizes durability and functionality. Many models feature HARDOX steel construction, known for its superior wear resistance and strength. This robust material ensures the bucket withstands the rigors of crushing hard materials like rock and concrete. Additionally, the inclusion of bolt-mounted wear plates simplifies maintenance by allowing quick replacements, reducing downtime.
Innovative design elements, such as hinged mechanisms and toggle plates, enhance the crushing process. Some buckets incorporate a figure-eight motion in the swing jaw plate, enabling efficient crushing at both the upper and lower sections of the chamber. Optional features, like iron separators for removing rebar, further expand the versatility of these attachments. By offering a range of dimensions and customizable design options, excavator jaw crusher buckets meet the unique demands of various industries.
Benefits and Applications of Excavator Jaw Crusher Buckets
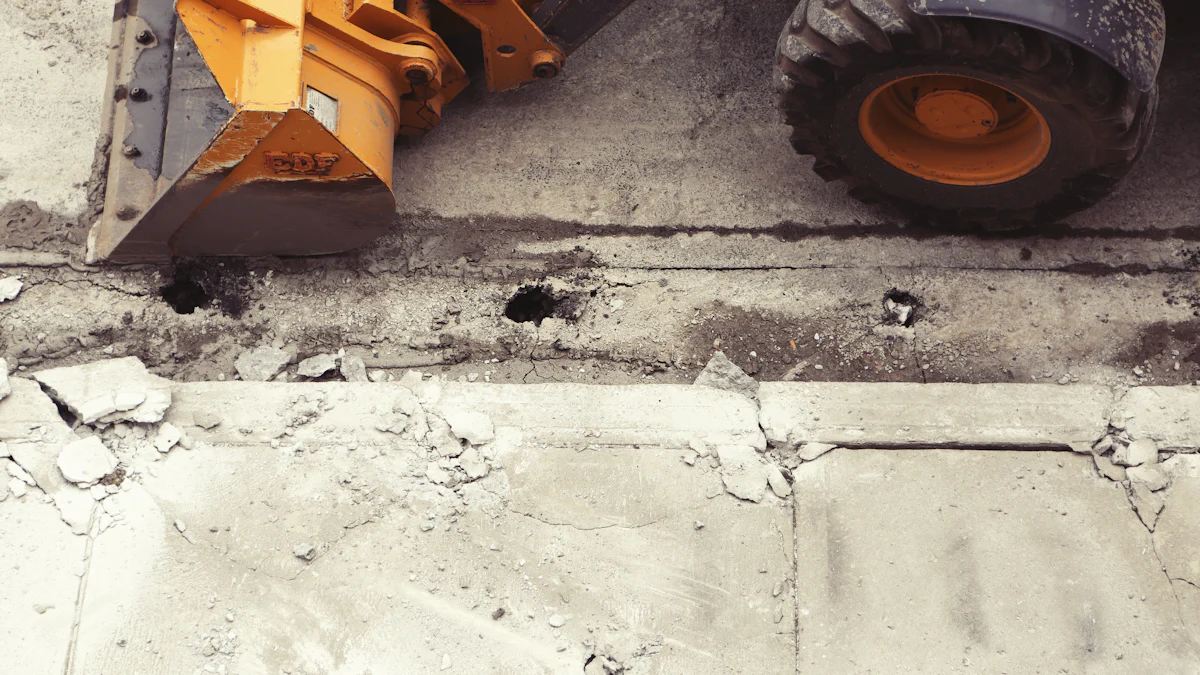
On-Site Material Recycling for Cost Efficiency
Excavator jaw crusher buckets enable efficient on-site material recycling, transforming waste into reusable resources. These attachments crush concrete, rock, and debris directly at the job site, eliminating the need to transport materials to external processing facilities. For instance, a bucket with a capacity of 1.30 cubic yards can handle significant volumes of material in a single cycle, reducing operational delays. Contractors can repurpose crushed materials for backfilling, road base, or other construction needs, minimizing the expense of purchasing new materials. This recycling capability not only lowers project costs but also supports sustainable construction practices.
Reduced Transportation and Disposal Costs
By processing materials on-site, excavator jaw crusher buckets significantly reduce transportation and disposal expenses. Hauling debris to off-site locations often involves high fuel costs and logistical challenges. With these buckets, contractors can eliminate the need for additional vehicles and trips. For example, a bucket weighing 2,900 pounds can efficiently crush and process heavy materials, reducing the volume of waste that requires disposal. This efficiency translates into lower landfill fees and fewer environmental impacts. The ability to manage waste directly at the source streamlines operations and enhances overall project profitability.
Versatility Across Construction, Demolition, and Mining Projects
Excavator jaw crusher buckets offer unmatched versatility, making them indispensable tools across various industries. In construction, they simplify tasks such as breaking down concrete structures and preparing materials for reuse. Demolition projects benefit from their ability to handle mixed debris, including reinforced concrete and brick. Mining operations utilize these buckets to crush rocks and extract valuable minerals efficiently. Their compatibility with excavators of different sizes ensures adaptability to diverse project requirements. Whether working on urban construction sites or remote mining locations, these buckets deliver reliable performance and flexibility.
Environmental Benefits of Waste Reduction
Excavator jaw crusher buckets contribute significantly to environmental sustainability by reducing construction waste. These attachments process materials like concrete, rock, and debris directly on-site, transforming them into reusable resources. This eliminates the need to transport waste to landfills, which decreases fuel consumption and lowers carbon emissions. For example, a bucket with a capacity of 1.30 cubic yards can handle substantial volumes of material in a single cycle, minimizing the environmental footprint of construction projects.
By recycling materials on-site, contractors reduce the demand for new raw materials. This practice conserves natural resources and supports eco-friendly construction methods. Additionally, the reduced reliance on external processing facilities helps limit the environmental impact of heavy machinery operations. The ability to manage waste efficiently aligns with modern sustainability goals, making these buckets an essential tool for environmentally conscious projects.
Time-Saving in Project Execution
Excavator jaw crusher buckets streamline project timelines by enabling on-site material processing. These attachments eliminate the need for transporting materials to off-site facilities, saving valuable time. With a bucket weight of 2,900 pounds, operators can efficiently crush and process heavy materials without delays. This capability ensures that projects progress smoothly, even under tight deadlines.
The adjustable jaw plates enhance operational efficiency by allowing contractors to customize output sizes quickly. This adaptability reduces downtime associated with switching between equipment or processing methods. Features like reversible running directions further minimize interruptions, ensuring continuous workflows. By integrating these buckets into their operations, contractors can complete tasks faster and achieve higher productivity levels.
How to Choose the Right Excavator Jaw Crusher Bucket
Selecting the right excavator jaw crusher bucket requires careful consideration of several factors. Making an informed decision ensures optimal performance, cost efficiency, and compatibility with your equipment and project needs. Below are key aspects to evaluate when choosing the ideal bucket for your operations.
Ensuring Compatibility with Your Excavator
Compatibility between the excavator and the jaw crusher bucket is crucial for seamless operation. Contractors must verify that the bucket matches the excavator’s size, weight, and hydraulic power. For instance, some crusher buckets are designed for excavators weighing between 22.5 and 36 tons, while others cater to smaller or larger machines. Ensuring this alignment prevents operational inefficiencies and reduces wear on both the bucket and the excavator.
Hydraulic pressure and flow rate also play a significant role in compatibility. Crusher buckets rely on the excavator’s hydraulic system to power their crushing mechanisms. Models with high-displacement radial piston hydraulic motors often require specific pressure levels to function effectively. Operators should consult the manufacturer’s specifications to confirm that their excavator meets these requirements. Proper compatibility guarantees reliable performance and extends the lifespan of the equipment.
Evaluating Material Type and Volume for Processing
Understanding the type and volume of materials to be processed is essential when selecting a crusher bucket. Different models excel at handling specific materials, such as reinforced concrete, rock, or demolition debris. For example, buckets equipped with a rotor system perform exceptionally well with deformable parts and wet or humid materials. Others feature replaceable jaw plates for fine or standard crushing, making them suitable for diverse applications.
The volume of material to be processed also influences the choice of bucket. Some models can crush up to 18 cubic yards of material per hour, making them ideal for high-demand projects. Contractors working on smaller-scale tasks may prefer compact buckets with lower capacities. Evaluating these factors ensures that the chosen bucket meets the project’s requirements without overburdening the equipment.
Considering Project-Specific Requirements
Every project has unique demands, and the right crusher bucket should align with these requirements. Features like adjustable jaw plates allow operators to customize the output size of crushed materials, ensuring compatibility with specific project needs. For instance, some buckets offer options for standard, fine, and ultra-fine crushing, providing flexibility for various tasks.
Additional features, such as dust suppression systems and iron separators, enhance the bucket’s functionality. Dust suppression improves visibility and safety on-site, while iron separators remove rebar from crushed materials, streamlining recycling processes. Contractors should assess whether these features add value to their operations.
Durability is another critical factor. Buckets constructed with HARDOX steel or similar high-strength materials withstand the rigors of heavy-duty use. Centralized greasing systems and bolt-mounted wear plates simplify maintenance, reducing downtime and extending the bucket’s service life. By considering these project-specific factors, contractors can select a bucket that delivers efficiency, reliability, and long-term value.
Budgeting for Long-Term Cost Efficiency
Investing in an excavator jaw crusher bucket requires careful financial planning to ensure long-term cost efficiency. These attachments, while initially requiring a significant investment, offer substantial savings over time by reducing operational expenses and enhancing productivity. Contractors and equipment owners must evaluate both upfront costs and the potential for long-term returns when budgeting for these tools.
To maximize cost efficiency, consider the following factors:
Durability and Maintenance Costs: High-quality crusher buckets, such as those made with HARDOX steel, provide exceptional wear resistance. This durability minimizes the need for frequent repairs or replacements, reducing maintenance expenses. Features like centralized greasing systems and bolt-mounted wear plates further simplify upkeep, ensuring consistent performance with minimal downtime.
Operational Savings: Crusher buckets eliminate the need for transporting materials to off-site processing facilities. By crushing materials directly on-site, contractors save on fuel, labor, and disposal fees. For example, models equipped with adjustable jaw plates allow operators to customize output sizes, reducing the need for additional equipment and streamlining workflows.
Versatility and Reusability: The ability to process a wide range of materials, including reinforced concrete and demolition debris, enhances the value of these attachments. Crushed materials can be reused for backfilling, road base, or other construction purposes, reducing the need to purchase new materials. This versatility translates into significant cost savings across multiple projects.
Energy Efficiency: Crusher buckets powered by the excavator’s hydraulic system eliminate the need for external energy sources. This integration not only simplifies operation but also reduces energy consumption, contributing to lower operational costs.
By considering these aspects, contractors can make informed decisions that align with their budgetary constraints while ensuring long-term financial benefits.
Choosing a Reliable Manufacturer like YNF Machinery
Selecting a dependable manufacturer is crucial when investing in an excavator jaw crusher bucket. A reliable supplier ensures high-quality products, excellent customer support, and long-term value. YNF Machinery stands out as a trusted partner for contractors and equipment owners worldwide.
YNF Machinery offers several advantages:
Proven Expertise: With over 35 years of experience in the excavator parts industry, YNF Machinery has established itself as a leader in providing durable and efficient solutions. Their expertise ensures that customers receive products designed to meet the demands of heavy-duty operations.
High-Quality Materials: YNF Machinery prioritizes quality by using robust materials like HARDOX steel in their products. This commitment to durability guarantees that their crusher buckets withstand the rigors of demanding environments, delivering reliable performance over time.
Customizable Features: YNF Machinery provides crusher buckets with adjustable jaw plates, reversible running directions, and optional iron separators. These features enhance versatility and efficiency, allowing contractors to tailor the equipment to their specific project needs.
Competitive Pricing: YNF Machinery offers competitive pricing without compromising on quality. Their low minimum order quantities make it easier for contractors to access high-quality parts, even for smaller-scale projects.
Comprehensive Support: YNF Machinery provides end-to-end support, including logistics assistance and detailed product documentation. This ensures a seamless purchasing experience and reliable after-sales service.
Choosing YNF Machinery guarantees access to premium crusher buckets that deliver exceptional performance and cost efficiency. Their dedication to quality and customer satisfaction makes them a preferred choice for contractors seeking reliable solutions.
Maintenance Tips for Excavator Jaw Crusher Buckets
Regular Inspection for Wear and Tear
Routine inspections play a vital role in maintaining the efficiency and longevity of excavator jaw crusher buckets. Operators should examine the bucket for visible signs of wear, such as cracks, dents, or deformation in the jaw plates and other structural components. Hydraulic connections and hoses also require close attention to ensure there are no leaks or damage that could compromise performance.
A systematic inspection schedule helps identify potential issues before they escalate into costly repairs. For example, checking the alignment of the jaws ensures consistent crushing performance and prevents uneven wear. By addressing minor problems early, contractors can avoid unexpected downtime and extend the lifespan of their equipment.
Cleaning and Lubrication of Moving Parts
Keeping the moving parts clean and well-lubricated is essential for the smooth operation of excavator jaw crusher buckets. Dust, debris, and crushed material often accumulate in the crushing chamber and around the hydraulic components. Regular cleaning prevents blockages and reduces the risk of abrasive particles causing premature wear.
Lubrication minimizes friction between moving parts, ensuring efficient operation and reducing the likelihood of mechanical failures. Operators should use manufacturer-recommended lubricants and follow the specified intervals for application. Centralized greasing systems, available on some models, simplify this process by allowing quick and even distribution of lubricant. Proper cleaning and lubrication not only enhance performance but also contribute to the overall durability of the bucket.
Replacing Worn Components Promptly
Timely replacement of worn components is critical to maintaining the functionality of excavator jaw crusher buckets. Jaw plates, in particular, experience significant wear due to constant contact with hard materials like concrete and rock. Operators should monitor the condition of these plates and replace them when they show signs of excessive wear or reduced crushing efficiency.
Other components, such as bolts, pins, and hydraulic seals, also require periodic replacement to ensure optimal performance. Using high-quality replacement parts, such as those offered by trusted manufacturers, guarantees compatibility and reliability. Promptly addressing worn components minimizes downtime and prevents further damage to the bucket or excavator.
By following these maintenance tips, contractors can maximize the efficiency, reliability, and lifespan of their excavator jaw crusher buckets. Regular care ensures that these attachments continue to deliver exceptional performance across various projects.
Following Manufacturer Guidelines for Maintenance
Adhering to manufacturer guidelines ensures the optimal performance and longevity of an excavator jaw crusher bucket. These guidelines provide detailed instructions on proper usage, maintenance schedules, and safety protocols. Operators should familiarize themselves with the manual provided by the manufacturer to avoid operational inefficiencies or potential damage.
Manufacturers often recommend specific intervals for inspecting and servicing the bucket. For example, regular checks on hydraulic connections, jaw plates, and wear components help identify issues early. Following these schedules minimizes downtime and prevents costly repairs. Additionally, using manufacturer-approved lubricants and replacement parts ensures compatibility and maintains the bucket’s efficiency.
Proper training for operators is another critical aspect of following these guidelines. Manufacturers typically outline best practices for installation, operation, and troubleshooting. By adhering to these instructions, contractors can maximize productivity while ensuring the safety of their team. Ignoring these recommendations may lead to equipment failure or void warranties, resulting in unnecessary expenses.
Partnering with YNF Machinery for Quality Replacement Parts
YNF Machinery offers a reliable solution for sourcing high-quality replacement parts for excavator jaw crusher buckets. Their extensive experience in the industry ensures that contractors receive durable and efficient components tailored to their needs. Partnering with YNF Machinery guarantees access to parts that meet rigorous quality standards, enhancing the performance and lifespan of the equipment.
The company provides a wide range of replacement parts, including jaw plates, hydraulic seals, and wear-resistant components. These parts are crafted from robust materials like HARDOX steel, ensuring they withstand the demands of heavy-duty operations. Contractors can rely on YNF Machinery for prompt delivery and comprehensive support, reducing downtime and maintaining project timelines.
YNF Machinery also offers competitive pricing and low minimum order quantities, making it easier for businesses of all sizes to access premium parts. Their commitment to customer satisfaction extends to providing detailed product documentation and logistics assistance. This level of service simplifies the procurement process and ensures a seamless experience for clients worldwide.
By choosing YNF Machinery, contractors gain a trusted partner dedicated to supporting their operations with reliable and cost-effective solutions. Their expertise and high-quality products make them an invaluable resource for maintaining excavator jaw crusher buckets.
Why Choose YNF Machinery for Excavator Jaw Crusher Buckets
Over 35 Years of Industry Expertise
YNF Machinery has built a reputation as a trusted supplier in the excavator parts industry. With over three decades of experience, the company has consistently delivered innovative solutions tailored to meet the demands of heavy-duty operations. Their expertise extends to understanding the unique challenges faced by contractors in construction, demolition, and mining sectors. This deep knowledge allows YNF Machinery to design and supply excavator jaw crusher buckets that excel in performance and durability.
The company’s long-standing presence in the market reflects its commitment to quality and customer satisfaction. For example, contractors using YNF Machinery products have reported significant improvements in operational efficiency. By leveraging their extensive industry experience, YNF Machinery ensures that every product meets the highest standards of reliability and functionality.
High-Quality Parts with Rigorous Quality Inspections
YNF Machinery prioritizes quality at every stage of production. Each excavator jaw crusher bucket undergoes rigorous quality inspections to ensure it meets strict performance criteria. The use of high-strength materials, such as HARDOX steel, guarantees durability even under the most demanding conditions. This attention to detail minimizes the risk of equipment failure and reduces maintenance costs for contractors.
The company’s dedication to quality is evident in the success stories of its customers. For instance, a contractor in Egypt utilized a jaw crusher bucket to crush unused basalt directly on-site. This approach not only reduced waste but also enhanced project efficiency. Such outcomes highlight the reliability of YNF Machinery’s products in real-world applications.
Competitive Pricing and Low Minimum Order Quantities
YNF Machinery offers competitive pricing without compromising on quality. This affordability makes their excavator jaw crusher buckets accessible to businesses of all sizes. The company also provides low minimum order quantities, enabling contractors to procure high-quality parts without overextending their budgets. This flexibility supports small-scale projects while maintaining the same level of excellence expected in larger operations.
The cost-effectiveness of YNF Machinery’s products extends beyond initial purchase prices. By eliminating the need for additional equipment, their crusher buckets help contractors save on operational expenses. For example, a customer in Italy used a jaw crusher bucket to process aggregates directly on-site, eliminating transportation costs and boosting profitability. These practical benefits make YNF Machinery a preferred choice for contractors seeking value-driven solutions.
Comprehensive Support and Logistics Assistance
YNF Machinery provides comprehensive support to ensure a seamless experience for contractors and equipment owners. Their team assists clients at every stage, from selecting the right excavator jaw crusher bucket to post-purchase services. This level of support minimizes operational challenges and enhances customer satisfaction.
Logistics assistance is another cornerstone of YNF Machinery’s service. The company ensures timely delivery of products, regardless of the client’s location. For instance, contractors in remote areas benefit from YNF Machinery’s efficient shipping network, which reduces delays and keeps projects on schedule. Detailed product documentation accompanies each shipment, simplifying installation and operation for users.
The company’s commitment to support extends to after-sales services. YNF Machinery offers guidance on maintenance practices, ensuring that customers maximize the lifespan of their equipment. Their team remains accessible for troubleshooting and technical advice, fostering long-term relationships with clients. This dedication to customer care sets YNF Machinery apart as a reliable partner in the industry.
Trusted by Excavator Owners and Contractors Worldwide
Excavator owners and contractors across the globe trust YNF Machinery for their high-quality products and dependable service. The company’s reputation stems from its consistent delivery of durable and efficient solutions tailored to diverse project needs. Contractors in industries such as construction, demolition, and mining rely on YNF Machinery to enhance their operations.
Real-world applications highlight the trust placed in YNF Machinery. In Italy, a contractor used a jaw crusher bucket to process aggregates for concrete production directly on-site. This approach eliminated the need for additional equipment, resulting in a more profitable operation. Similarly, in Egypt, a customer installed a crusher bucket to crush unused basalt in a quarry. The crushed material was reused on-site, reducing waste and saving money.
These examples demonstrate the versatility and reliability of YNF Machinery’s products. Contractors value the company’s ability to provide solutions that streamline workflows and reduce costs. By consistently meeting the demands of challenging environments, YNF Machinery has earned the trust of clients worldwide.
Understanding the features, specifications, and benefits of excavator jaw crusher buckets is essential for optimizing material processing and project efficiency. Selecting the right bucket ensures compatibility with equipment and aligns with specific project requirements. YNF Machinery stands out as a trusted provider of high-quality excavator parts, offering durable and efficient solutions tailored to industry needs. Contractors and equipment owners can rely on YNF Machinery for expert guidance and customized recommendations. Consulting their team guarantees access to reliable products and exceptional support for achieving operational success.