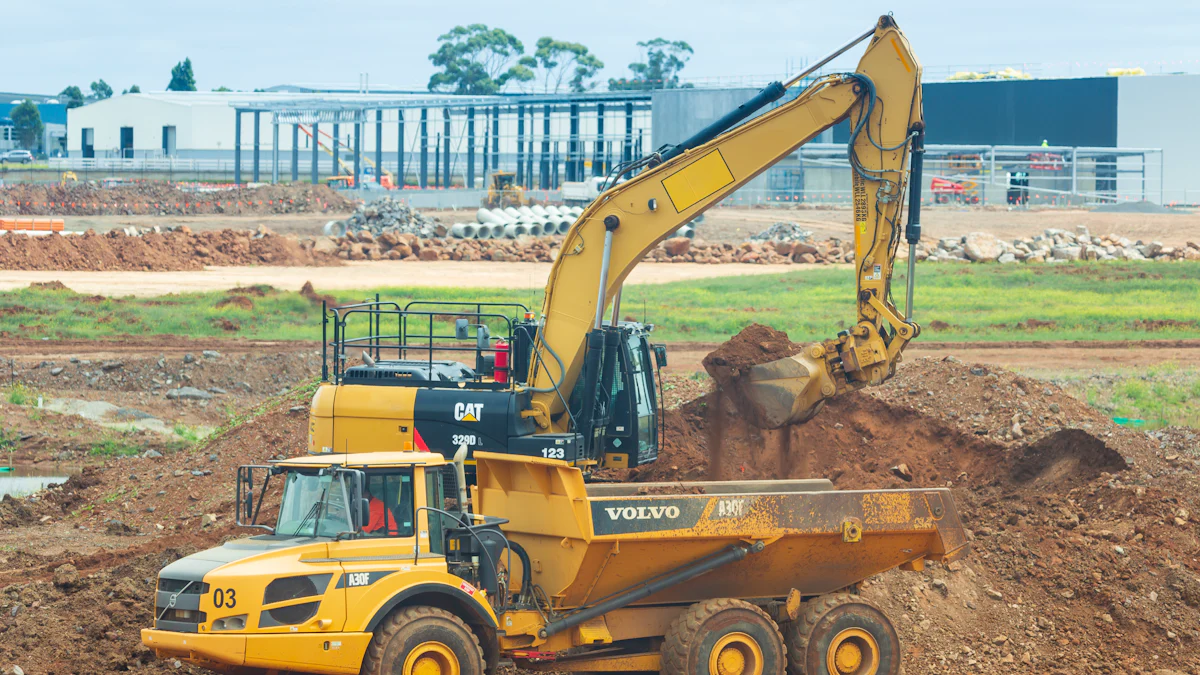
Excavator final drive parts serve as the backbone of an excavator’s mobility and efficiency. These components, including gears and hydraulic systems, endure immense stress during operation. Proper understanding of their functionality and maintenance ensures optimal performance and prevents costly downtime. Regular care, such as monitoring for wear and contamination, extends their lifespan significantly. YNF Machinery, with over 35 years of expertise, stands as a trusted provider of high-quality final drive parts. Their commitment to reliability and precision helps excavator owners maintain peak operational efficiency while reducing unexpected failures.
Key Takeaways
Understanding the key components of excavator final drive parts is crucial for optimal performance and longevity.
Regular inspections of hydraulic connections, such as flow and return lines, can prevent leaks and ensure consistent pressure.
Maintaining face seals is essential to prevent contamination, which can lead to increased wear and costly repairs.
Routine lubrication of the gearbox and motor assembly components helps reduce friction and prolongs their lifespan.
Identifying and addressing common issues, such as oil degradation and bearing wear, can significantly enhance the efficiency of the final drive system.
Implementing preventative maintenance practices, like regular cleaning and timely replacements, ensures the reliability of excavator operations.
Partnering with a trusted provider like YNF Machinery can help ensure access to high-quality components and expert support for maintaining excavator performance.
Key Components of Excavator Final Drive Parts
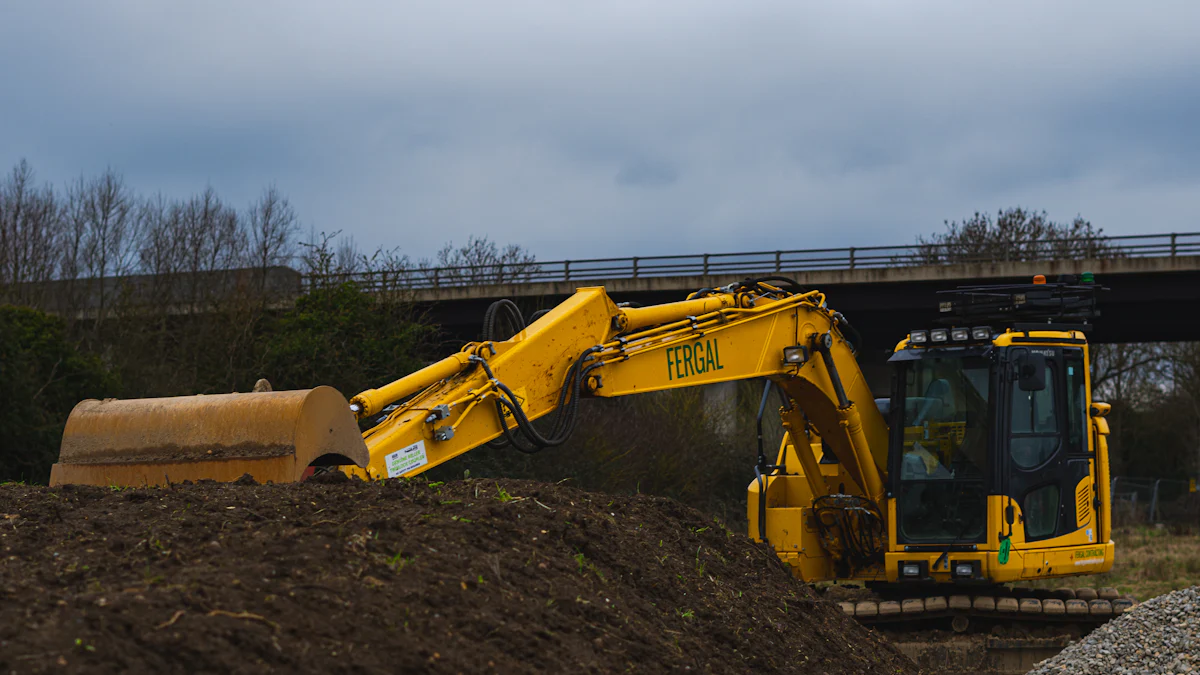
Understanding the key components of excavator final drive parts is essential for ensuring optimal performance and longevity. Each component plays a vital role in transferring power and maintaining the machine’s mobility. Below is an in-depth look at these critical elements.
Hydraulic Connections in Excavator Final Drive Parts
Hydraulic connections are integral to the functionality of excavator final drive parts. They ensure the smooth transfer of hydraulic power, enabling the machine to operate efficiently.
Flow and Return Lines
Flow and return lines transport hydraulic fluid between the pump and the final drive motor. These lines must remain free from leaks or blockages to maintain consistent pressure and flow. Regular inspections help identify wear or damage early, preventing operational disruptions.
Case Drain Lines
Case drain lines carry excess hydraulic fluid back to the reservoir. This process prevents pressure build-up within the motor, which could otherwise lead to damage. Proper maintenance of these lines ensures the motor operates without unnecessary strain.
Speed Lines
Speed lines regulate the speed of the excavator’s tracks. They control the hydraulic flow rate, allowing the operator to adjust the machine’s movement according to the task. Faulty speed lines can result in uneven or erratic track movement.
Brake Lines
Brake lines play a crucial role in the safety of the excavator. They activate the braking system, ensuring the machine stops when required. Any issues with these lines could compromise the operator’s control over the equipment.
Gearbox Assembly in Excavator Final Drive Parts
The gearbox assembly is a mechanical powerhouse within the final drive system. It converts hydraulic energy into mechanical force, driving the excavator’s tracks.
Planetary Gears
Planetary gears are the heart of the gearbox assembly. Their design allows for efficient torque transfer, enabling the excavator to handle heavy loads. Proper lubrication and alignment are essential to prevent gear wear and ensure smooth operation.
Bearings and Seals
Bearings and seals support the gearbox’s moving parts while preventing contamination. Bearings reduce friction, while seals keep dirt and debris out of the system. Regular maintenance of these components extends the gearbox’s lifespan.
Rotator Group
The rotator group facilitates the rotation of the gearbox, ensuring seamless movement of the tracks. This component must remain in excellent condition to avoid disruptions in the excavator’s mobility.
Motor Assembly in Excavator Final Drive Parts
The motor assembly is the driving force behind the final drive system. It converts hydraulic energy into mechanical motion, powering the excavator’s tracks.
Hydraulic Motor
The hydraulic motor is a critical component that drives the tracks. It must deliver consistent power to ensure smooth and efficient operation. Insufficient lubrication can lead to motor failure, emphasising the importance of regular maintenance.
Drive Shaft
The drive shaft transfers power from the hydraulic motor to the gearbox. It must remain robust and free from damage to handle the stress of heavy-duty operations. Routine inspections help detect potential issues before they escalate.
Snap Rings and Their Role
Snap rings secure various components within the motor assembly. They prevent parts from shifting during operation, ensuring the system remains stable. Proper installation and inspection of snap rings are vital to avoid mechanical failures.
Face Seals in Excavator Final Drive Parts
Face seals play a pivotal role in the performance and longevity of excavator final drive parts. These seals act as a barrier, preventing external contaminants from entering the system and ensuring the internal components remain protected.
Importance of Face Seals in Preventing Contamination
Face seals are designed to shield the internal mechanisms of the final drive from dirt, debris, and moisture. These contaminants, if allowed to infiltrate, can cause significant damage to the gears, bearings, and other critical components. By maintaining a secure seal, face seals help preserve the integrity of the hydraulic and mechanical systems.
“Final drives are critical components in excavators, responsible for transferring power from the hydraulic motor to the tracks, allowing the machine to move efficiently.”
The effectiveness of face seals directly impacts the overall efficiency of the excavator. A well-maintained seal ensures that the hydraulic motor and gearbox operate without interference, reducing the risk of wear and tear. Regular inspections of face seals are essential to identify any signs of damage or misalignment that could compromise their function.
Common Wear Issues and Their Impact
Face seals are subjected to constant stress during operation, making them prone to wear over time. Common issues include cracking, deformation, and loss of elasticity. These problems often arise due to prolonged exposure to extreme temperatures, abrasive materials, or insufficient lubrication.
When face seals wear out, contaminants can enter the final drive system, leading to:
Increased friction: Dirt and debris can cause excessive friction between moving parts, accelerating wear.
Hydraulic fluid contamination: Contaminants can degrade the quality of hydraulic fluid, reducing its effectiveness and causing potential damage to the motor.
Component failure: Prolonged exposure to contaminants can result in the failure of gears, bearings, and other vital parts.
To mitigate these risks, operators should prioritise routine maintenance. Cleaning the seals, checking for visible damage, and replacing worn-out seals promptly can prevent costly repairs and downtime.
Face seals are indispensable for maintaining the performance and reliability of excavator final drive parts. Their role in preventing contamination ensures the smooth operation of the entire system, highlighting the importance of regular inspections and timely replacements.
Insights from Real-World Inspections of Excavator Final Drive Parts
Real-world inspections of excavator final drive parts reveal critical insights into their performance and maintenance needs. These inspections help identify common issues, enabling operators to take proactive measures to prevent costly repairs and downtime.
Common Issues with Gear Oil in Excavator Final Drive Parts
Contamination and its Effects
Contamination in gear oil often results from dirt, debris, or water entering the system. This issue compromises the oil’s ability to lubricate effectively, leading to increased friction and wear on internal components. Contaminated oil can also cause overheating, which accelerates the degradation of gears and bearings. Operators must ensure that seals remain intact and that oil reservoirs are free from external pollutants. Regular oil analysis can detect contamination early, allowing for timely corrective actions.
Signs of Oil Degradation
Degraded gear oil loses its viscosity and protective properties, making it less effective at reducing friction. Common signs of oil degradation include discolouration, a burnt smell, and the presence of metal particles. These indicators suggest that the oil is no longer providing adequate lubrication, which can lead to severe damage to the final drive system. Routine oil changes and monitoring help maintain optimal performance and extend the lifespan of excavator final drive parts.
Face Seal Wear and Damage in Excavator Final Drive Parts
Causes of Premature Wear
Face seals endure constant stress during operation, making them susceptible to wear. Premature wear often occurs due to improper maintenance, exposure to abrasive materials, or extreme temperature fluctuations. Unbalanced seals, for instance, experience higher face loads, which can increase wear rates. Additionally, inadequate lubrication exacerbates the problem by causing excessive friction between the seal faces.
How to Identify and Address Seal Damage
Operators can identify seal damage by inspecting for visible cracks, deformation, or oil leaks. Damaged seals allow contaminants to enter the system, leading to further complications such as gear oil contamination and component failure. Addressing seal damage promptly involves replacing worn-out seals and ensuring proper installation. Regular inspections and timely replacements prevent extensive damage and maintain the efficiency of the final drive system.
“Regular inspection and timely replacement of seals are necessary to prevent final drive damage caused by oil leaks, inadequate lubrication, and contamination due to seal failure.”
Needle Bearing Damage in Excavator Final Drive Parts
Symptoms of Bearing Failure
Needle bearings play a crucial role in supporting the rotational movement within the final drive system. Symptoms of bearing failure include unusual noises, increased vibration, and reduced operational efficiency. These signs often indicate excessive wear or misalignment, which can lead to further damage if left unaddressed. Operators should remain vigilant for these symptoms during routine maintenance checks.
Preventative Maintenance Tips
Preventative maintenance ensures the longevity of needle bearings. Lubricating the bearings regularly reduces friction and prevents overheating. Keeping the system free from contaminants also minimises wear. Operators should follow manufacturer guidelines for maintenance intervals and use high-quality lubricants to enhance performance. Early detection of potential issues through regular inspections helps avoid costly repairs and prolongs the life of excavator final drive parts.
Common Failures and Preventative Measures for Excavator Final Drive Parts
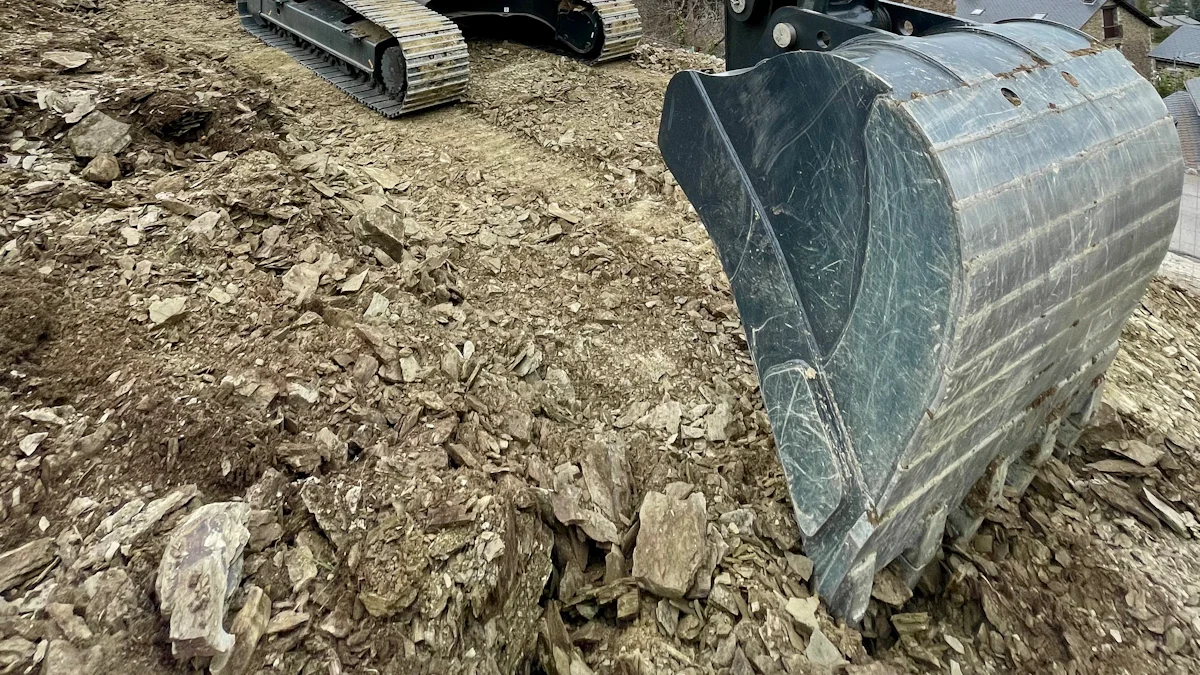
Excavator final drive parts are vital for the efficient operation of heavy machinery. However, these components often face failures due to wear, improper maintenance, or operational stress. Understanding common issues and implementing preventative measures can significantly enhance their lifespan and performance.
Snap Ring Failures in Excavator Final Drive Parts
Causes of Snap Ring Dislodgement
Snap rings secure various components within the final drive system. Dislodgement often occurs due to excessive vibration, improper installation, or wear over time. Technicians frequently observe that insufficient lubrication exacerbates this issue, as it increases friction and stress on the snap rings. Additionally, exposure to contaminants such as dirt or debris can weaken the structural integrity of these rings, leading to premature failure.
“Neglecting regular maintenance often results in snap ring dislodgement, causing severe damage to the final drive system,” emphasised experts at Vikfin.
How to Prevent Snap Ring Issues
Preventative measures play a crucial role in avoiding snap ring failures. Operators should ensure proper installation during assembly, as misaligned rings are more prone to dislodgement. Regular inspections help detect early signs of wear or damage. Lubricating the system adequately reduces friction and minimises stress on the snap rings. Keeping the final drive system clean and free from contaminants also prevents unnecessary wear. Following these practices ensures the stability and reliability of the snap rings.
Rotator Group Damage in Excavator Final Drive Parts
Signs of Wear in the Rotator Group
The rotator group facilitates the smooth rotation of the gearbox, making it a critical component of the final drive system. Signs of wear include unusual noises, reduced efficiency, and uneven track movement. Engineers often identify these issues during routine inspections, noting that prolonged exposure to abrasive materials or insufficient lubrication accelerates wear.
“Operators must remain vigilant for early signs of rotator group damage to prevent costly repairs,” advised technicians and engineers.
Maintenance Practices to Extend Lifespan
Proper maintenance significantly extends the lifespan of the rotator group. Regular lubrication reduces friction and prevents overheating. Cleaning the system thoroughly removes abrasive particles that could cause damage. Operators should also monitor the alignment of the rotator group, as misalignment increases wear. Adhering to manufacturer-recommended maintenance schedules ensures optimal performance and longevity.
Hydraulic Line Failures in Excavator Final Drive Parts
Identifying Leaks and Blockages
Hydraulic lines transport fluid essential for the operation of excavator final drive parts. Leaks often result from worn-out seals or damaged hoses, while blockages occur due to the accumulation of debris or degraded hydraulic fluid. Common symptoms include reduced hydraulic pressure, erratic track movement, and visible fluid leaks. Early detection of these issues prevents further complications.
“Hydraulic line failures are a frequent cause of downtime in excavators, highlighting the importance of regular inspections,” stated experts at Vikfin.
Best Practices for Hydraulic Line Maintenance
Maintaining hydraulic lines involves several key practices. Operators should inspect hoses and connections regularly for signs of wear or damage. Replacing worn-out seals promptly prevents leaks. Flushing the hydraulic system periodically removes contaminants and ensures smooth fluid flow. Using high-quality hydraulic fluid enhances the performance of the system and reduces the risk of blockages. These measures minimise the likelihood of hydraulic line failures and ensure the efficient operation of the final drive system.
Understanding and maintaining excavator final drive parts is essential for ensuring the machine’s efficiency and longevity. Regular care, such as inspecting seals and lubricating components, prevents common issues like contamination and wear. Neglecting maintenance often leads to failures, including bearing damage and hydraulic line leaks, which disrupt operations.
YNF Machinery plays a pivotal role in providing reliable, high-quality components. Their expertise and commitment to precision help operators maintain peak performance. Proper care of the final drive system not only reduces downtime but also extends the excavator’s lifespan, ensuring consistent productivity in demanding environments.