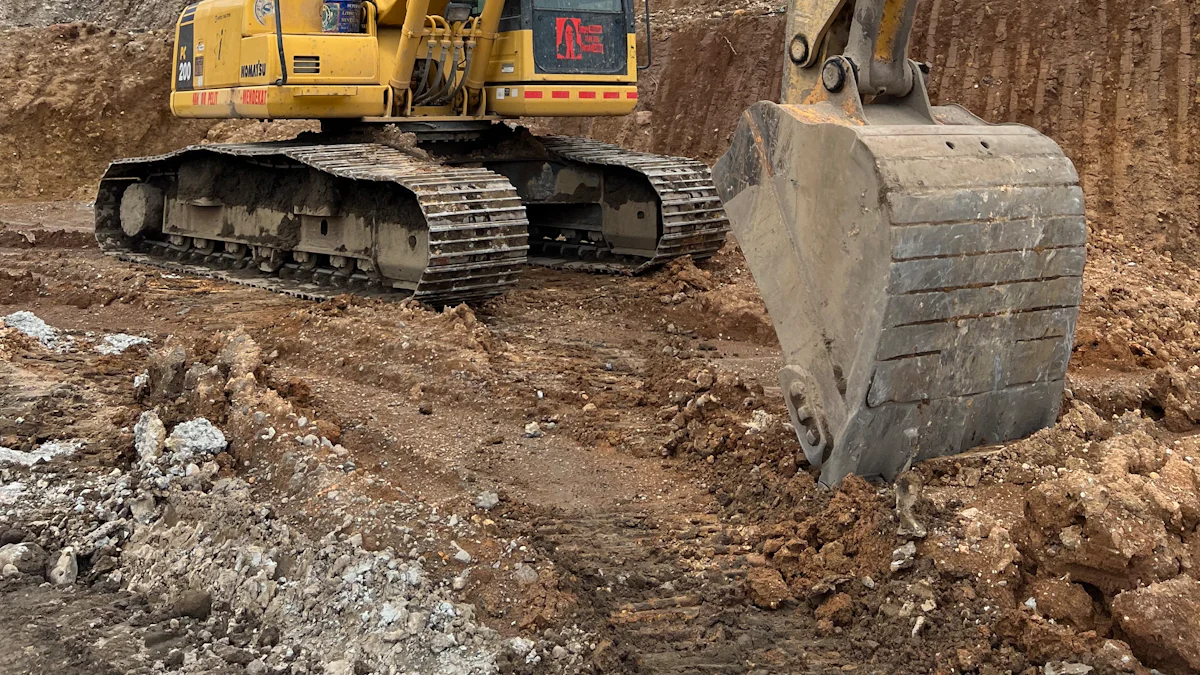
Excavators are marvels of engineering, designed to tackle demanding tasks such as digging, lifting, and moving heavy materials. The different parts of an excavator work in harmony to ensure seamless operation. The hydraulic system enables precise movements, while the engine provides the power required for every function. However, modern excavators operate at only 30% efficiency, with 70% of energy wasted in the hydraulic system. This inefficiency not only affects performance but also accounts for 50% of carbon dioxide emissions from construction machinery. Gaining a deeper understanding of the different parts of an excavator and their roles can help optimize performance and minimize waste.
Key Takeaways
Excavators operate with only 30% efficiency, highlighting the importance of understanding their components to optimize performance and reduce waste.
The undercarriage provides stability and mobility, essential for navigating various terrains; regular maintenance is crucial for its longevity.
The cab is designed for operator comfort and safety, featuring intuitive controls and visibility enhancements to ensure efficient operation.
The boom, arm, and bucket work in unison to perform digging and lifting tasks; understanding their roles can improve operational precision.
Hydraulic systems are vital for powering excavator movements; regular maintenance can prevent energy loss and enhance efficiency.
Choosing the right attachments for specific tasks can significantly increase an excavator’s versatility and efficiency on the job site.
Regular inspections and maintenance of all components, including couplings and hydraulic systems, are essential for maximizing the excavator’s performance and lifespan.
Overview of the Main Parts of an Excavator
Understanding the main parts of an excavator is essential for appreciating how these machines perform their tasks with precision and power. Each component plays a specific role, contributing to the overall functionality and efficiency of the equipment. Below is a breakdown of the key parts of an excavator and their functions.
Key Components of an Excavator
Undercarriage
The undercarriage forms the foundation of the excavator. It supports the machine’s weight and ensures stability during operation. Tracks, rollers, and idlers make up this critical component. Tracks provide excellent traction and distribute weight evenly, allowing the excavator to navigate rough terrains with ease. For smoother surfaces like asphalt, wheeled undercarriages offer greater mobility and agility. Proper maintenance of the undercarriage ensures the excavator remains stable and maneuverable across various environments.
Cab
The cab serves as the operator’s command center. Inside, you’ll find controls such as joysticks, levers, and pedals that allow precise management of the excavator’s movements. The cab also prioritizes operator comfort with ergonomic seating and intuitive interfaces. Visibility features enhance safety, enabling operators to monitor their surroundings effectively. This enclosed space ensures that you can operate the machine efficiently, even during extended work hours.
Boom and Arm
The boom and arm are the most prominent excavator components, responsible for the machine’s reach and digging capabilities. The boom extends outward from the body, providing the lifting power needed to position the arm and bucket. The arm, often referred to as the stick or dipper, connects the boom to the bucket. It offers precision and control, allowing you to dig at specific depths or angles. Together, the boom and arm form the backbone of the excavator’s digging and material-handling functions.
Bucket
The bucket is one of the most versatile attachments on an excavator. It is designed for digging, scooping, and moving materials such as soil, debris, or rocks. Buckets come in various shapes and sizes, tailored to different excavation tasks. For example, a trenching bucket is ideal for narrow digs, while a rock bucket handles heavy-duty tasks. Choosing the right bucket ensures that your excavator performs efficiently for the job at hand.
Hydraulic System
The hydraulic system powers the movements of the boom, arm, and bucket. This intricate network of pumps, hoses, valves, and cylinders delivers the force needed for heavy-duty tasks. It allows you to control the excavator with precision, whether you’re digging, lifting, or rotating. Regular maintenance of the hydraulic system ensures smooth operation and prevents energy loss, maximizing the machine’s efficiency.
Counterweight
The counterweight is located at the rear of the excavator. It balances the machine during operation, preventing it from tipping over when lifting heavy loads. This component is crucial for maintaining stability, especially when the boom and arm are fully extended. A well-designed counterweight ensures that the excavator remains safe and steady, even under challenging conditions.
Engine
The engine is the powerhouse of the excavator. It converts fuel into mechanical energy, driving all the machine’s functions. Most excavators use diesel engines, known for their durability and ability to generate high torque. A reliable engine ensures that the excavator operates efficiently, providing the power needed for demanding tasks.
The Undercarriage: Stability and Mobility in Excavators
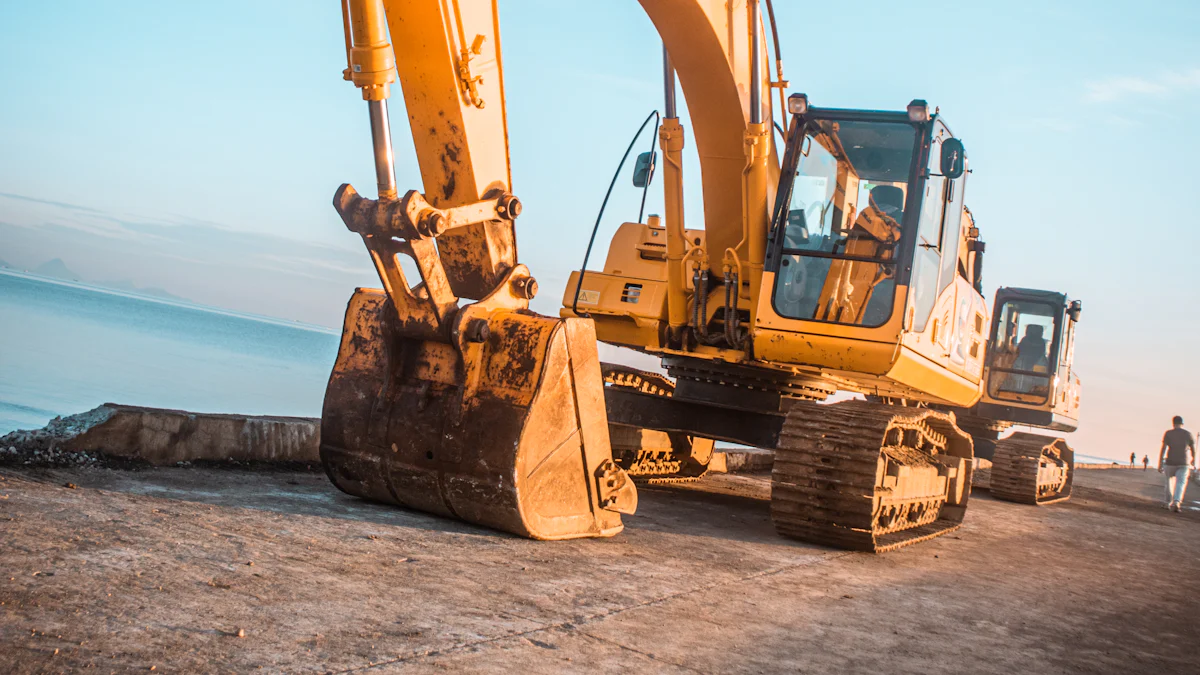
The excavator undercarriage plays a crucial role in ensuring both stability and mobility. It consists of several components that work together to support the machine’s weight and facilitate movement across various terrains. Understanding these components will help you appreciate how they contribute to the excavator’s overall performance.
Tracks and Their Role in Terrain Adaptability
Excavator tracks are essential for providing traction and stability. They allow the machine to adapt to different terrains, whether rough or smooth. The wide base of the tracks distributes the weight evenly, preventing the excavator from sinking into soft ground. Steel tracks offer durability and are ideal for rugged environments, while rubber tracks are better suited for paved surfaces. By choosing the right type of tracks, you can ensure that your excavator operates efficiently in any setting.
Drive Motors and Sprockets: Powering Movement
Drive motors and sprockets are vital for powering the movement of the excavator. The drive motors convert hydraulic energy into mechanical motion, propelling the tracks forward or backward. Sprockets engage with the tracks, ensuring smooth and controlled movement. This combination allows you to maneuver the excavator with precision, whether navigating tight spaces or traversing challenging terrains. Regular maintenance of these components ensures reliable performance and minimizes downtime.
How the Undercarriage Supports Excavator Operations
The excavator undercarriage provides a stable foundation for all operations. It supports the machine’s weight, allowing it to lift heavy loads without tipping over. The undercarriage also absorbs shocks and vibrations, protecting the excavator from damage during operation. By maintaining the undercarriage in good condition, you can enhance the machine’s longevity and ensure safe and efficient performance.
The Cab: The Operator’s Command Center
The cab of an excavator serves as the operator’s command center, where every function of the machine comes under your control. Modern cabs are designed to enhance safety, precision, and comfort, ensuring you can operate efficiently even during long work hours. Let’s explore how the cab’s features contribute to the overall performance of the excavator.
Controls and Interfaces for Precision
The controls inside the cab are your primary tools for managing the excavator’s movements. These include joysticks, pedals, and levers, which allow you to operate the boom, arm, bucket, and undercarriage with precision. Advanced excavators feature intuitive interfaces that simplify complex tasks. For example, touchscreens and digital displays provide real-time data on machine performance, fuel levels, and hydraulic pressure. The main controls are strategically placed to ensure easy access, enabling you to focus on the task without unnecessary distractions. By mastering these controls, you can achieve greater accuracy and efficiency in your operations.
Safety and Visibility Features
Safety is a top priority in any excavator cab. Modern designs incorporate reinforced glass and rollover protection systems to shield you from potential hazards. High-visibility windows and strategically placed mirrors give you a clear view of your surroundings, reducing blind spots and enhancing operational safety. Some cabs also include cameras and proximity sensors, which provide additional layers of protection when working in confined spaces or near other equipment. These features ensure that you can operate the excavator confidently, knowing that safety measures are in place.
Operator Comfort and Ergonomics
Comfort plays a crucial role in maintaining productivity during extended work hours. Excavator cabs now come equipped with ergonomic seating that supports your posture and reduces fatigue. Adjustable seats, armrests, and control panels allow you to customize the workspace to your preferences. Climate control systems, such as air conditioning and heating, create a comfortable environment regardless of external weather conditions. Noise insulation further enhances the experience by minimizing distractions, allowing you to concentrate fully on the task at hand. These advancements ensure that you can work efficiently without compromising your well-being.
The Boom, Arm, and Bucket: The Workhorse of an Excavator
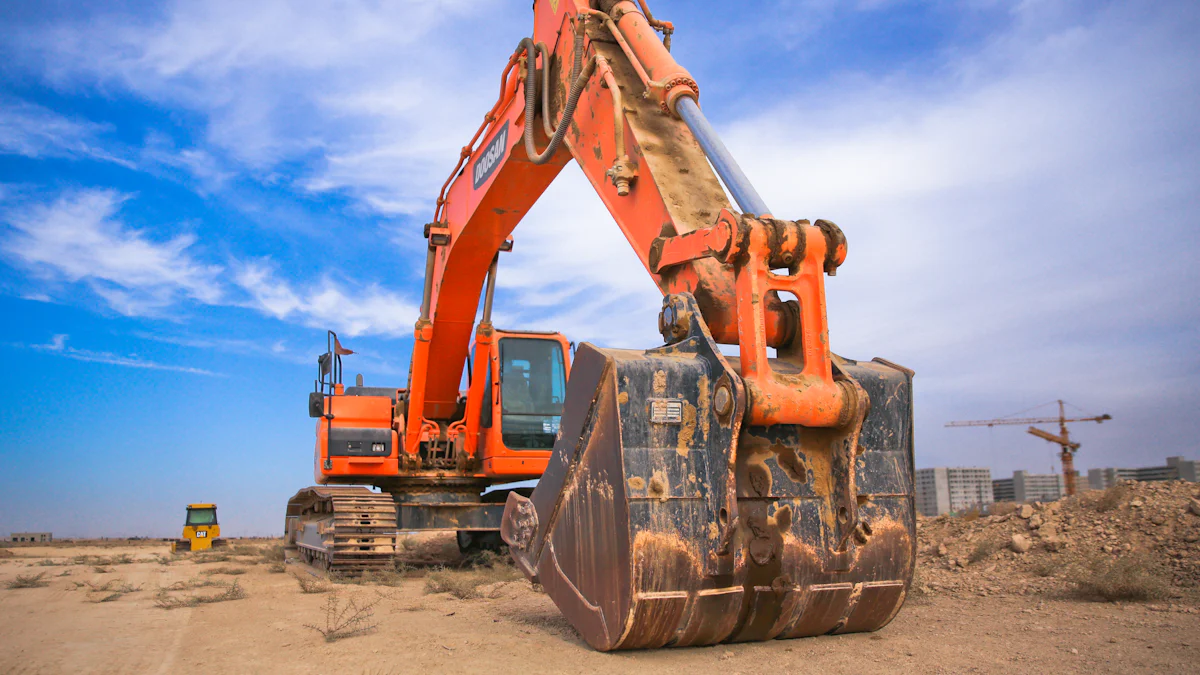
The boom, arm, and bucket form the core of an excavator’s functionality. These components work together to handle digging, lifting, and material movement with precision and power. Understanding their individual roles helps you maximize the efficiency of your machine.
Boom: Providing Lifting Power
The boom serves as the primary lifting mechanism of the excavator. It extends outward from the machine’s body, providing the strength needed to raise and position the arm and bucket. The design of the boom allows it to handle heavy loads while maintaining stability. Whether you’re lifting debris or reaching over obstacles, the boom ensures that the excavator performs with reliability. Regular inspection of the boom is essential to maintain its structural integrity and ensure safe operation.
Arm: Extending Reach and Precision
The arm, also known as the stick or dipper, connects the boom to the bucket. It plays a crucial role in controlling the depth and precision of excavation tasks. By extending or retracting the arm, you can adjust the distance between the boom and the bucket, allowing for precise digging, grading, or lifting. The length of the arm varies depending on the size of the excavator. For tight spaces, shorter arms provide better maneuverability, while longer arms are ideal for deep excavations. The arm works seamlessly with the boom to position the bucket accurately, ensuring efficient material handling.
Bucket: Digging and Material Handling
The bucket is the attachment that performs the actual digging and material handling. It is designed to scoop, lift, and move materials such as soil, rocks, or debris. Buckets come in various shapes and sizes, each tailored to specific tasks. For instance:
Trenching buckets are ideal for creating narrow, precise trenches.
Rock buckets handle heavy-duty tasks like breaking through tough surfaces.
Grading buckets are perfect for leveling and smoothing surfaces.
Hydraulic cylinders control the bucket’s movement, enabling you to dig and dump materials with precision. Choosing the right bucket for your task ensures optimal performance and reduces wear on the machine.
Attachments for Versatility Beyond the Bucket
Excavators are not limited to digging and scooping. With the right attachments, you can transform your machine into a versatile tool for a wide range of tasks. These attachments expand the capabilities of your excavator, making it suitable for specialized jobs in construction, demolition, landscaping, and more.
Common Excavator Attachments and Their Uses
Hydraulic Breakers
Hydraulic breakers, also known as hammers, are essential for breaking through tough materials like concrete, asphalt, or rocks. These attachments deliver powerful blows, making them ideal for demolition projects or roadwork.Grapples
Grapples are perfect for handling irregularly shaped materials such as logs, scrap metal, or debris. They provide a firm grip, allowing you to lift and move objects with precision. Grapples are widely used in recycling, forestry, and waste management industries.Augers
Augers are designed for drilling holes into the ground. Whether you’re installing fence posts, planting trees, or setting up utility poles, augers make the task quick and efficient. They come in various sizes to match the depth and diameter of the holes you need.Thumb Attachments
Thumb attachments work in tandem with the bucket to secure materials during lifting. They are especially useful for picking up large rocks, logs, or other bulky items that might slip out of the bucket.Tiltrotators
Tiltrotators add flexibility to your excavator by allowing the bucket or other attachments to rotate 360 degrees and tilt at various angles. This feature enhances precision and efficiency, particularly in grading, trenching, or landscaping tasks.Rippers
Rippers are used to break up hard soil, ice, or compacted ground. They are a valuable tool for preparing sites for excavation or construction.
Benefits of Using Attachments
Attachments enhance the functionality of your excavator, enabling you to tackle diverse tasks without investing in additional machinery. By swapping out the bucket for a specialized attachment, you can adapt your excavator to meet the demands of specific projects. This versatility not only saves time but also reduces operational costs.
“The right attachment can turn your excavator into a multi-functional powerhouse, increasing its value on any job site.”
Choosing the Right Attachments
When selecting attachments, consider the nature of your project and the specifications of your excavator. Factors such as hydraulic flow, weight capacity, and compatibility play a crucial role in ensuring optimal performance. For example, a hydraulic breaker requires sufficient hydraulic pressure to operate effectively, while a grapple must match the size and lifting capacity of your machine.
Regular maintenance of attachments is equally important. Inspect hydraulic connections, moving parts, and wear points to ensure they remain in good condition. Proper care extends the lifespan of your attachments and maintains their efficiency.
YNF Machinery: Supporting Your Attachment Needs
At YNF Machinery, we understand the importance of high-quality attachments for maximizing your excavator’s potential. Our extensive range of excavator parts, including couplings and hydraulic components, ensures seamless integration and reliable performance. Whether you need a durable hydraulic breaker or a versatile tiltrotator, we provide solutions tailored to your needs.
By equipping your excavator with the right attachments, you can unlock its full potential and take on a variety of challenges with confidence.
The Hydraulic System: Powering the Different Parts of an Excavator
The hydraulic system serves as the lifeblood of an excavator, powering its essential movements and enabling it to perform heavy-duty tasks with precision. This system transforms hydraulic energy into mechanical force, ensuring that components like the boom, arm, and bucket operate seamlessly. A well-maintained hydraulic system not only enhances performance but also extends the lifespan of your machine.
Hydraulic Pumps and Cylinders
Hydraulic pumps and cylinders form the core of the excavator’s hydraulic system. The pump generates pressurized fluid, which flows through hoses and valves to power the machine’s movements. Most excavators use variable displacement pumps, which adjust the flow rate based on the task’s demands, ensuring efficiency.
Hydraulic cylinders convert this pressurized fluid into mechanical motion. These cylinders control the movement of the boom, arm, and bucket. For example:
Boom cylinders lift and lower the boom.
Arm cylinders extend and retract the arm.
Bucket cylinders tilt the bucket for digging or dumping.
The coordination between pumps and cylinders ensures smooth and precise operation. Regular inspection of these components helps prevent leaks and maintains consistent performance.
How Hydraulics Enable Movement
The hydraulic system enables the excavator to perform complex tasks by transmitting power to various components. When you operate the controls in the cab, hydraulic fluid flows through a network of hoses and valves to the desired part of the machine. This fluid movement creates the force needed to lift, dig, or rotate.
For instance, when you move the joystick to lift the boom, the hydraulic pump sends pressurized fluid to the boom cylinder. The cylinder then extends, raising the boom. Similarly, rotating the cab or moving the tracks relies on hydraulic motors powered by the same system. This seamless integration allows you to control the excavator with precision, even in challenging conditions.
Hydraulic systems also power attachments like breakers, grapples, and augers. These tools rely on the same pressurized fluid to deliver high-impact force or rotational motion, expanding the excavator’s versatility.
“Hydraulics make it possible for excavators to handle tasks that require immense power and precision, from breaking concrete to digging trenches.”
Maintenance Tips for Hydraulic Efficiency
Proper maintenance of the hydraulic system is crucial for ensuring efficiency and preventing costly downtime. Follow these tips to keep your excavator’s hydraulics in top condition:
Inspect Hydraulic Hoses and Connections
Check hoses regularly for signs of wear, cracks, or leaks. Tighten loose connections to prevent fluid loss and maintain pressure.Monitor Hydraulic Fluid Levels
Maintain the correct fluid levels to ensure smooth operation. Use high-quality hydraulic fluid recommended by the manufacturer to reduce wear and tear.Replace Filters Periodically
Hydraulic filters remove contaminants from the fluid. Replace them as per the maintenance schedule to prevent blockages and maintain system efficiency.Check for Overheating
Overheating can damage hydraulic components. Monitor the system’s temperature during operation and address any issues promptly.Lubricate Moving Parts
Proper lubrication reduces friction and extends the life of hydraulic cylinders and other components.Schedule Regular Maintenance
Conduct routine inspections and servicing to identify potential issues early. Partnering with a reliable supplier like YNF Machinery ensures access to high-quality hydraulic parts and expert support.
By following these maintenance practices, you can maximize the efficiency of your excavator’s hydraulic system and reduce operational costs.
Integration of Parts: How Excavators Perform Tasks
Excavators are remarkable machines, designed to perform complex tasks by integrating their various components seamlessly. Each part works in harmony to ensure precision, power, and efficiency. Whether you are digging trenches, lifting heavy loads, or navigating challenging terrains, understanding how these parts collaborate can help you maximize the machine’s potential.
Digging: Coordination of Boom, Arm, and Bucket
Digging is one of the primary functions of an excavator. The boom, arm, and bucket work together to achieve this task with precision and efficiency. The boom provides the initial lifting power, allowing you to position the arm and bucket at the desired angle. The arm extends or retracts to control the depth and reach of the excavation. Finally, the bucket scoops up the material, whether it’s soil, rocks, or debris.
The hydraulic system plays a vital role in this coordination. When you operate the controls, hydraulic fluid flows through the system, powering the cylinders that move the boom, arm, and bucket. This seamless integration ensures that you can dig with accuracy, even in tight spaces or challenging conditions. Regular maintenance of the hydraulic system, such as checking fluid levels and inspecting hoses, keeps these movements smooth and efficient.
“The boom, arm, and bucket form the backbone of an excavator’s digging capabilities, working in perfect sync to handle even the toughest excavation tasks.”
Lifting and Moving: Role of Counterweight and Hydraulics
Lifting heavy loads requires a delicate balance of power and stability. The counterweight, located at the rear of the excavator, plays a crucial role in maintaining this balance. It offsets the weight of the boom, arm, and bucket when they are extended, preventing the machine from tipping over. This stability allows you to lift and move materials safely and efficiently.
Hydraulics provide the power needed for lifting. The hydraulic pump generates pressurized fluid, which powers the cylinders responsible for raising and lowering the boom and arm. This system ensures that you can lift heavy loads with precision, whether you’re moving construction materials or clearing debris. By combining the counterweight’s stability with the hydraulic system’s power, you can handle lifting tasks with confidence.
Mobility: Undercarriage and Engine Working Together
Mobility is essential for any excavator, and the undercarriage and engine work together to ensure smooth movement across various terrains. The undercarriage, which includes tracks, rollers, and drive motors, provides the traction and stability needed for navigating rough or uneven surfaces. Tracks distribute the machine’s weight evenly, preventing it from sinking into soft ground. Steel tracks are ideal for rugged environments, while rubber tracks are better suited for paved surfaces.
The engine powers the undercarriage, converting fuel into mechanical energy that drives the tracks. Hydraulic motors transfer this energy to the tracks, enabling you to move the excavator forward, backward, or turn in place. This collaboration between the undercarriage and engine ensures that you can position the machine precisely, whether you’re working on a construction site or in a confined space.
“The undercarriage and engine form the foundation of an excavator’s mobility, allowing it to adapt to different terrains and complete tasks efficiently.”
By understanding how these parts integrate, you can operate your excavator more effectively. Regular maintenance of the hydraulic system, counterweight, and undercarriage ensures that the machine performs at its best, reducing downtime and increasing productivity.
The Role of Excavator Couplings in Power Transmission (YNF Machinery)
Excavator couplings play a vital role in ensuring smooth and efficient power transmission between the engine and the hydraulic pump system. These components act as the bridge that transfers mechanical energy, enabling the hydraulic system to perform essential tasks like digging, lifting, and rotating. Without reliable couplings, the excavator’s performance would suffer, leading to inefficiencies and potential downtime.
How Excavator Couplings Work
Couplings connect the engine’s rotational movement to the hydraulic pump. This connection allows the hydraulic system to generate the pressurized fluid needed to power the boom, arm, bucket, and other attachments. By compensating for slight misalignments between the engine and pump, couplings ensure consistent power delivery without causing undue stress on the machinery.
“The hydraulic pump is the heart of the excavator, and couplings are the arteries that keep it running efficiently.”
High-quality couplings also absorb vibrations and shocks generated during operation. This feature protects the engine and hydraulic pump from wear and tear, extending their lifespan and maintaining optimal performance. The ability to handle misalignment and dampen vibrations makes couplings indispensable for heavy-duty excavators.
Types of Excavator Couplings
Different types of couplings are designed to meet specific operational needs. Each type offers unique benefits, ensuring compatibility with various excavator models and applications. Some common types include:
Flexible Couplings: These couplings compensate for angular and axial misalignments while reducing vibrations. They are ideal for maintaining smooth power transmission in demanding conditions.
Jaw Couplings: Known for their simplicity and durability, jaw couplings provide reliable performance in standard excavator operations.
Disc Couplings: These couplings offer high torque capacity and are suitable for heavy-duty applications.
Fluid Couplings: Designed for smooth acceleration, fluid couplings use hydraulic fluid to transmit power, reducing mechanical stress.
YNF Machinery specializes in providing a wide range of excavator couplings, including Centaflex-A, Centaflex-H, Bowex, and Monolastic models. Each coupling is crafted to deliver exceptional durability and performance, ensuring your excavator operates at its best.
Benefits of High-Quality Couplings
Investing in high-quality excavator couplings offers several advantages:
Enhanced Efficiency
Reliable couplings ensure seamless power transmission, reducing energy loss and improving overall machine efficiency.Reduced Downtime
Durable couplings minimize the risk of mechanical failures, keeping your excavator operational for longer periods.Extended Equipment Lifespan
By absorbing vibrations and compensating for misalignments, couplings protect critical components like the engine and hydraulic pump from premature wear.Versatility
With various types and models available, you can find couplings tailored to your specific excavator and application needs.
YNF Machinery: Your Partner for Reliable Couplings
At YNF Machinery, we understand the importance of dependable excavator parts. Our couplings are manufactured using high-quality materials and advanced processes, ensuring they withstand the toughest working conditions. Whether you need a flexible coupling for vibration isolation or a high-torque model for heavy-duty tasks, we have the right solution for you.
Our couplings are designed for easy installation and maintenance, saving you time and effort. With options for custom manufacturing, we can also meet unique requirements for specialized applications. By choosing YNF Machinery, you gain access to products that enhance your excavator’s performance and reliability.
“Reliable couplings are the backbone of efficient excavator operations. YNF Machinery ensures you get the quality and support you need to keep your equipment running smoothly.”
Maintaining Your Excavator Couplings
To maximize the lifespan and efficiency of your couplings, follow these maintenance tips:
Inspect Regularly: Check for signs of wear, cracks, or misalignment. Address issues promptly to prevent further damage.
Lubricate as Needed: Some couplings require periodic lubrication to reduce friction and wear. Follow the manufacturer’s guidelines.
Monitor Vibrations: Excessive vibrations may indicate coupling issues. Investigate and resolve the cause to maintain smooth operation.
Replace When Necessary: Over time, even the best couplings may wear out. Replace them with high-quality options from YNF Machinery to ensure continued performance.
By prioritizing maintenance and investing in durable couplings, you can enhance your excavator’s efficiency and reduce operational costs. YNF Machinery stands ready to support you with top-tier products and expert guidance.
Types of Excavators and Their Specialized Parts
Excavators come in various designs, each tailored to specific tasks and environments. Understanding the different types of excavators and their specialized parts helps you choose the right machine for your needs. Below, we explore three common types and their unique features.
Crawler Excavators: Stability on Rough Terrain
Crawler excavators are built for challenging terrains. Their tracks provide excellent stability and traction, making them ideal for uneven or soft ground. The wide base of the tracks distributes the machine’s weight evenly, preventing it from sinking into mud or sand. This feature ensures reliable performance in construction, mining, and forestry projects.
The hydraulic system in crawler excavators powers the boom, arm, and bucket with precision. The boom provides the lifting strength, while the arm, often called the dipper, extends the reach for digging or material handling. The bucket, attached at the end, scoops and moves materials efficiently. These components work together seamlessly, enabling the machine to perform heavy-duty tasks with ease.
Crawler excavators also feature a robust counterweight at the rear. This counterweight balances the machine during operation, ensuring stability even when lifting heavy loads. If you need a machine that can handle rough terrain and demanding tasks, a crawler excavator is an excellent choice.
Wheeled Excavators: Mobility and Speed
Wheeled excavators offer unmatched mobility and speed. Unlike crawler excavators, these machines use wheels instead of tracks, allowing them to move quickly across paved roads and urban environments. Their agility makes them perfect for tasks like road construction, utility work, and landscaping.
The hydraulic system in wheeled excavators powers the same essential components: the boom, arm, and bucket. The boom provides the lifting power, while the arm (or dipper) ensures precise control during digging or grading. The bucket handles material movement, just as in other excavator types. These parts work in harmony, delivering efficiency and accuracy.
Wheeled excavators often include stabilizers to enhance balance during operation. These stabilizers prevent tipping when the machine is stationary and performing heavy tasks. If your project requires frequent relocation or work on hard surfaces, a wheeled excavator offers the versatility you need.
Mini Excavators: Compact and Versatile
Mini excavators are compact machines designed for tight spaces. Their small size allows them to navigate areas where larger excavators cannot operate. Despite their size, mini excavators pack impressive power, making them suitable for tasks like trenching, digging, and demolition in confined spaces.
The hydraulic system in mini excavators ensures smooth operation of the boom, arm, and bucket. The boom provides the lifting capability, while the arm (or dipper) extends the reach for precise excavation. The bucket handles material movement efficiently, just like in larger models. These components work together to deliver reliable performance in small-scale projects.
Mini excavators often feature rubber tracks, which minimize damage to delicate surfaces like lawns or pavements. Their lightweight design reduces ground pressure, making them ideal for landscaping and residential construction. If you need a machine that combines power with maneuverability, a mini excavator is the perfect solution.
“Choosing the right type of excavator depends on your project’s requirements. Each type offers unique advantages, ensuring you can tackle any challenge with confidence.”
Long-Reach Excavators: Extended Reach for Specialized Tasks
Long-reach excavators are designed to handle tasks that require extended reach and precision. These machines excel in specialized applications such as dredging, deep excavation, and demolition in hard-to-access areas. The elongated boom and arm provide the extra reach needed to perform tasks that standard excavators cannot handle effectively.
The extended boom and arm allow you to work at greater distances without repositioning the machine. This feature proves invaluable when working on projects like riverbank reinforcement or clearing debris from tall structures. The hydraulic system ensures smooth and controlled movements, even when the boom and arm are fully extended. This precision minimizes the risk of errors and enhances efficiency.
Long-reach excavators also maintain stability during operation. The counterweight at the rear balances the machine, preventing tipping when handling heavy loads at extended distances. Tracks or wheels provide mobility, allowing you to position the excavator accurately for optimal performance. Regular maintenance of the hydraulic system and structural components ensures the machine operates reliably in demanding conditions.
“When your project demands extended reach and precision, long-reach excavators deliver unmatched performance and versatility.”
Demolition Excavators: Heavy-Duty Performance
Demolition excavators are built to withstand the rigors of heavy-duty tasks. These machines are equipped with reinforced booms, arms, and attachments designed to handle the stress of tearing down structures. Whether you’re demolishing buildings, bridges, or industrial facilities, demolition excavators provide the power and durability needed for the job.
The hydraulic system in demolition excavators powers specialized attachments like hydraulic breakers, shears, and pulverizers. These tools enable you to break through concrete, cut steel beams, and crush debris efficiently. The reinforced structure of the boom and arm ensures they can handle the high-impact forces generated during demolition.
Safety features play a crucial role in demolition excavators. The cab is often equipped with protective guards and reinforced glass to shield you from falling debris. High-visibility windows and cameras enhance situational awareness, allowing you to operate the machine safely in hazardous environments.
Tracks or wheels provide stability and mobility, enabling you to navigate uneven terrain or confined spaces. The counterweight ensures balance during operation, even when using heavy attachments. Regular inspection and maintenance of the hydraulic system and attachments keep the machine performing at its best.
“Demolition excavators combine power, precision, and safety, making them indispensable for heavy-duty tasks.”
How YNF Machinery Supports Different Excavator Types with Engine Parts
At YNF Machinery, we understand the importance of reliable engine parts for maximizing the performance of different excavator types. The engine serves as the heart of the excavator, providing the power needed to operate the hydraulic system, boom, arm, and attachments. High-quality engine parts ensure your machine runs efficiently, reducing downtime and maintenance costs.
YNF Machinery offers a wide range of engine parts compatible with various excavator models, including long-reach and demolition excavators. Our selection includes pistons, cylinders, crankshafts, and bearings, all designed to withstand the demands of heavy-duty applications. These parts are made from durable materials, ensuring they perform reliably under high temperatures and pressure.
We also provide engine overhaul kits, gaskets, and turbochargers to meet your specific needs. These components enhance fuel efficiency and reduce emissions, helping you lower operating costs while maintaining environmental compliance. Our parts undergo rigorous quality inspections to ensure they meet or exceed industry standards.
“With YNF Machinery’s engine parts, you can keep your excavator running smoothly, no matter the type or application.”
Our commitment to customer satisfaction extends beyond providing high-quality products. We offer expert support to help you select the right parts for your excavator. Whether you need components for a long-reach excavator or a demolition machine, YNF Machinery ensures you have access to reliable solutions that enhance performance and longevity.
Excavators are intricate machines where the different parts of an excavator work in unison to deliver exceptional performance. Each component, from the undercarriage to the hydraulic system, plays a vital role in ensuring the machine operates efficiently. Understanding the parts of an excavator and their specific functions empowers you to make informed decisions about operation, maintenance, and equipment selection. By choosing high-quality components, such as those offered by YNF Machinery, you can enhance reliability and extend the lifespan of your excavator, ensuring it meets the demands of any project with precision and durability.
FAQ
What is the primary purpose of an excavator?
An excavator is a versatile machine designed for tasks like digging, lifting, grading, and demolition. Its adaptability comes from its various attachments, such as buckets, hydraulic breakers, and augers, which allow it to perform a wide range of functions in construction, mining, and landscaping.
How do I choose the right type of excavator for my project?
To select the right excavator, consider the terrain and the nature of your project. For rough or uneven ground, crawler excavators with tracks provide stability and traction. If speed and maneuverability on smooth surfaces are essential, wheeled excavators are a better choice. For tight spaces, mini excavators offer compact efficiency. Evaluate your project’s specific needs to make the best decision.
What are the most common attachments for excavators?
Excavators can use a variety of attachments to enhance their functionality. Common options include:
Buckets for digging and material handling.
Hydraulic breakers for breaking concrete or rocks.
Augers for drilling holes.
Grapples for handling irregularly shaped materials.
Tiltrotators for increased flexibility in movement.
Each attachment serves a unique purpose, making excavators adaptable to different tasks.
How does the hydraulic system in an excavator work?
The hydraulic system powers the excavator’s movements by converting hydraulic energy into mechanical force. Pressurized fluid flows through hoses and valves to operate components like the boom, arm, and bucket. This system ensures precision and power, enabling the excavator to handle heavy-duty tasks efficiently.
What maintenance does an excavator require?
Regular maintenance keeps your excavator running smoothly. Key tasks include:
Inspecting hydraulic hoses and connections for leaks.
Monitoring fluid levels and replacing filters.
Checking tracks or wheels for wear.
Lubricating moving parts to reduce friction.
Scheduling routine inspections to identify potential issues early.
Proper care extends the lifespan of your machine and minimizes downtime.
Can excavators operate on all types of terrain?
Yes, but the type of excavator determines its suitability for specific terrains. Crawler excavators excel on rough or uneven ground due to their tracks, which provide stability and prevent sinking. Wheeled excavators, on the other hand, are ideal for paved surfaces and urban environments where speed and agility are crucial.
What is the role of the counterweight in an excavator?
The counterweight, located at the rear of the excavator, balances the machine during operation. It offsets the weight of the boom, arm, and bucket when extended, preventing tipping. This stability is essential for safe and efficient lifting and digging tasks.
How do I maximize the efficiency of my excavator?
To optimize efficiency:
Use the right attachment for the task.
Maintain the hydraulic system to prevent energy loss.
Choose the appropriate excavator type for the terrain.
Train operators to use controls precisely.
Perform regular maintenance to avoid unexpected breakdowns.
These steps ensure your excavator operates at peak performance.
What makes YNF Machinery’s excavator parts reliable?
YNF Machinery provides high-quality excavator parts designed for durability and performance. Their products, such as hydraulic components and couplings, undergo rigorous quality checks to meet industry standards. With a focus on reliability and customer satisfaction, YNF Machinery ensures your excavator remains efficient and productive.
Can I customize excavator parts for specific needs?
Yes, YNF Machinery offers custom manufacturing options for specialized applications. Whether you need unique couplings, hydraulic components, or engine parts, they can tailor solutions to meet your requirements. This flexibility ensures compatibility and optimal performance for your excavator.